Continuous stirred-tank reactor

The continuous flow stirred-tank reactor (CSTR), also known as vat- or backmix reactor, is a common ideal reactor type in chemical engineering. A CSTR often refers to a model used to estimate the key unit operation variables when using a continuous[†] agitated-tank reactor to reach a specified output. (See Chemical reactors.) The mathematical model works for all fluids: liquids, gases, and slurries.
The behavior of a CSTR is often approximated or modeled by that of a Continuous Ideally Stirred-Tank Reactor (CISTR). All calculations performed with CISTRs assume perfect mixing. In a perfectly mixed reactor, the output composition is identical to composition of the material inside the reactor, which is a function of residence time and rate of reaction. If the residence time is 5-10 times the mixing time, this approximation is valid for engineering purposes. The CISTR model is often used to simplify engineering calculations and can be used to describe research reactors. In practice it can only be approached, in particular in industrial size reactors.
Assume:
- perfect or ideal mixing, as stated above
Integral mass balance on number of moles Ni of species i in a reactor of volume V.
1. [1]
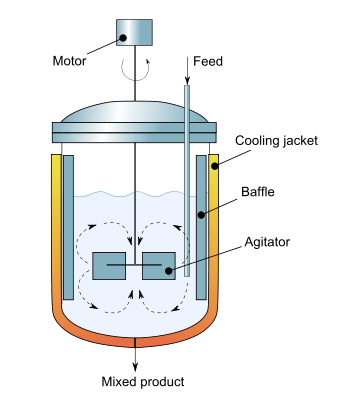
where Fio is the molar flow rate inlet of species i, Fi the molar flow rate outlet, and stoichiometric coefficient. The reaction rate, r, is generally dependent on the reactant concentration and the rate constant (k). The rate constant can be determined by using a known empirical reaction rates that is adjusted for temperature using the Arrhenius temperature dependence. Generally, as the temperature increases so does the rate at which the reaction occurs. Residence time, , is the average amount of time a discrete quantity of reagent spends inside the tank.
Assume:
- constant density (valid for most liquids; valid for gases only if there is no net change in the number of moles or drastic temperature change)
- isothermal conditions, or constant temperature (k is constant)
- steady state
- single, irreversible reaction (νA = -1)
- first-order reaction (r = kCA)
A → products
NA = CA V (where CA is the concentration of species A, V is the volume of the reactor, NA is the number of moles of species A)
2. [1]
The values of the variables, outlet concentration and residence time, in Equation 2 are major design criteria.
To model systems that do not obey the assumptions of constant temperature and a single reaction, additional dependent variables must be considered. If the system is considered to be in unsteady-state, a differential equation or a system of coupled differential equations must be solved.
CSTR's are known to be one of the systems which exhibit complex behavior such as steady-state multiplicity, limit cycles and chaos.
References
- 1 2 Schmidt, Lanny D. (1998). The Engineering of Chemical Reactions. New York: Oxford University Press. ISBN 0-19-510588-5.
Notes
† Chemical reactors often have significant heat effects, so it is important to be able to add or remove heat from them. In a CSTR (continuous stirred tank reactor) the heat is added or removed by virtue of the temperature difference between a jacket fluid and the reactor fluid. Often, the heat transfer fluid is pumped through agitation nozzle that circulates the fluid through the jacket at a high velocity. The reactant conversion in a chemical reactor is a function of a residence time or its inverse, the space velocity. For a CSTR, the product concentration can be controlled by manipulating the feed flow rate, which changes the residence time for a constant chemical reactor. Occasionally the term "continuous" is misinterpreted as a modifier for "stirred", as in 'continuously stirred'. This misinterpretation is especially prevalent in the civil engineering literature. As explained in the article,"continuous" means 'continuous-flow' — and hence these devices are sometimes called, in full, continuous-flow stirred-tank reactors (CFSTR's).