Current sensing techniques
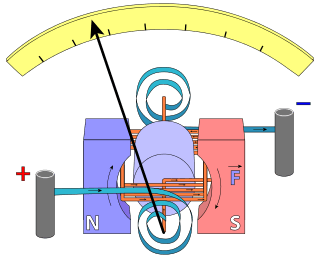
Current sensing is a vital task in electrical sector, where the current information is required for monitoring and control purposes. The measurement of current ranges from picoamps to several hundreds of amps depending upon the application in which the current is being measured and differentiated from one another based on required specifications such as the measurement of peak to peak value, RMS value, accuracy, bandwidth, robustness, cost, isolation or size and many different current measurement methods have been developed to satisfy these demands. Today, current information increasingly needs to be available in digital form for digital control or monitoring purposes. This requires the output signal of a particular current sensing technique to be acquired by an analog-to-digital converter.
Since the use of the first current indicating instrument called galvanometer, metrology have been developed and presently there are different technologies available to measure electric current which includes the shunt resistor based on the Ohm’s Law, AC current measurements carried out by traditional current transformers and Rogowski coils, Magnetic-field based transducers and there are other emerging technologies like the magneto-resistance effect (MR) Transducers.
Requirements in current measurement
Current sensing technologies must fulfill various requirements, for various applications. Generally, the common requirements are:
- High sensitivity
- High accuracy and linearity
- Wide bandwidth
- DC and AC measurement
- Low temperature drift
- Interference rejection
- IC packaging
- Low power consumption
- Low price
Current Sensing Techniques
In term of products today available on the market, the measurement of the electric current can be made with devices of different designs or technologies, and it can be classified depending upon the underlying fundamental physical principles such as,
- Ohm's Law of Resistance
- Faraday's Law of Induction
- Magnetic field sensors
- Faraday Effect
Current sensors Based on Ohm's Law
Ohm's Law the voltage drop across a resistor is proportional to the current going through it.The reformulation of Ohm's law by Gustav Kirchhoff is given by,
where J is the current density at a given location in a resistive material, E is the electric field at that location, and σ is the conductivity. This relationship can be used to sense currents. Sensors based on this simple relationship are well known for their lower costs, and reliability due to this simple principle.
Shunt Resistor
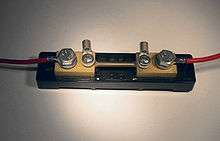
The common and simple approach to current sensing is the use of a shunt resistor. The voltage drop across the shunt is proportional to its current flow. Both alternating currents (AC) and direct currents (DC) can be measured with the shunt resistor.The high performance coaxial shunt have been widely used for many applications fast rise-time transient currents and high amplitudes but, highly integrated electronic devices prefer low-cost surface mounted devices (SMDs),[1] because of their small sizes and relatively low prices. The parasitic inductance present in the shunt affects high precision current measurement. Although this affects only the magnitude of the impedance at relatively high frequency, but also its effect on the phase at line frequency causes a noticeable error at a low power factor. The low cost and high reliability make the low resistance current shunt a very popular choice for current measurement system. The major disadvantage of using the shunt is that fundamentally a shunt is a resistive element, the power loss is thus proportional to the square of the current passing through it and consequently it is a rarity amongst high current measurements. Fast-response for measuring high-impulse or heavy-surge currents is the common requirement for shunt resistors. In 1981 Malewski,[2] designed a circuit to eliminate the skin effect and later in 1999 the flap-strap sandwich shunt (FSSS)[3] was introduced from a flat-strap sandwich resistor. The properties of the FSSS in terms of response time, power loss and frequency characteristics, are the same as the shunt resistor but the cost is lower and the construction technique is less sophisticated, compared to Malewski and the coaxial shunt.
Trace Resistance sensing
The intrinsic resistance of a conducting element, usually a copper trace in Printed circuit Board(PCB) can use be used as sensing element instead of a shunt resistor.[4] Since no additional resistor is required this approach promises a low-cost and space saving configuration with no additional power losses either. Naturally, the voltage drop of a copper trace is very low due to its very low resistance, making the presence of a high gain amplifier mandatory in order to get a useful signal. There are several physical effects which may alter the current measurement process: thermal drift of the copper trace, initial conditions of the trace resistance etc. Therefore, this approach is not suitable for applications that require a reasonable accuracy due to the large thermal drift. In order to overcome the problems associated with the temperature drift, a digital controller can be used for thermal drift compensation and calibration of the copper trace.[5] A significant drawback of this kind of current sensor is the unavoidable electrical connection between the current to be measured and the sense circuit. By employing a so-called isolation amplifier, electrical isolation can be added. However, these amplifiers are expensive and can also deteriorate the bandwidth, accuracy and thermal drift of the original current sensing technique. For these reasons, current sensing techniques based on physical principles that provide intrinsic electrical isolation deliver a better performance at lower costs in applications where isolation is required.
Current sensor based on Faraday's Law
Faraday's Law of induction – that states: the total electromotive force induced in a closed circuit is proportional to the time rate of change of the total magnetic flux linking the circuit – has been largely employed in current sensing techniques. Two major sensing devices based on Faraday’s law are Current transformers (CTs) and Rogowski coils. These sensors provide an intrinsic electrical isolation between the current to be measured and the output signal, thus making these current sensing devices mandatory, where safety standards demand electrical isolation.
Current Transformer

The CT is based on the principle of a transformer and converts a high primary current into a smaller secondary current and is common among high AC current measurement system. As this device is a passive device, no extra driving circuitry is needed in its implementation. Another major advantage is that it can measure very high current while consuming little power. The disadvantage of the CT is that a very high primary current or a substantial DC component in the current can saturate the ferrite material used in the core ultimately corrupting the signal. Another problem is that once the core is magnetized, it will contain hysteresis and the accuracy will degrade unless it is demagnetized again.
Rogowski coil
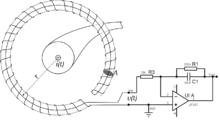
Rogowski coil is based on the principle of Faraday’s law of induction and the output voltage Vout of the Rogowski coil is determined by integrating the current Ic to be measured. It is given by,
where A is the cross-sectional area of the coil N is the number of turns, The Rogowski coil has a low sensitivity and is due to the absence of a high permeability magnetic core, that the current transformer can take advantage of. However, this can be compensated by adding more windings on the Rogowski coil or using an integrator with a higher gain k. More windings increase the self-capacitance and self-inductance, and higher integrator gain means an amplifier with a large gain-bandwidth product. As always in engineering, trade-offs must be made depending on specific applications.
Magnetic Field Sensors
Hall Effect Sensor
Hall effect sensors are devices based on the Hall-effect, which was discovered by Edwin Hall in 1879 based on the physical principle of the Lorentz force. They are activated by an external magnetic field. In this generalized device, the Hall sensor senses the magnetic field produced by the magnetic system. This system responds to the quantity to be sensed (current, temperature, position, velocity, etc.) through the input interface. The Hall element is the basic magnetic field sensor. It requires signal conditioning to make the output usable for most applications. The signal conditioning electronics needed are an amplifier stage and temperature compensation. Voltage regulation is needed when operating from an unregulated supply. If the Hall voltage is measured when no magnetic field is present, the output should be zero. However, if voltage at each output terminal is measured with respect to ground, a non-zero voltage will appear. This is the common mode voltage (CMV), and is the same at each output terminal. The output interface then converts the electrical signal from the Hall sensor; the Hall voltage: a signal that is significant to the application context. The Hall voltage is a low level signal on the order of 30 μvolts in the presence of one gauss magnetic field. This low-level output requires an amplifier with low noise, high input impedance and moderate gain. A differential amplifier with these characteristics can be readily integrated with the Hall element using standard bipolar transistor technology. Temperature compensation is also easily integrated.
Flux gate sensors
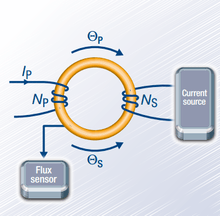
Flux gate sensors or Saturable inductor current sensors work on the same measurement principle as Hall-effect-based current sensors: the magnetic field created by the primary current to be measured is detected by a specific sensing element. The design of the saturable inductor current sensor is similar to that of a closed-loop Hall-effect current sensor; the only difference is that this method uses the saturable inductor instead of the Hall-effect sensor in the air gap.
Saturable inductor current sensor is based on the detection of an inductance change. The saturable inductor is made of small and thin magnetic core wound with a coil around it. The saturable inductor operates into its saturation region. It is designed in such a way that the external and internal flux density will affect its saturation level. Change in the saturation level of a saturable inductor will alter core’s permeability and, consequently, its inductance L. The value of saturable inductance (L) is high at low currents (based on the permeability of the core) and low at high currents (the core permeability becomes unity when saturated).Fluxgate detectors rely on the property of many magnetic materials to exhibit a non-linear relationship between the magnetic field strength H and the flux density B.[6]
In this technique, high frequency performance is achieved by using two cores without air gaps. One of the two main cores is used to create a saturable inductor and the other is used to create a high frequency transformer effect. In another approach, three cores can be used without air gap. Two of the three cores are used to create saturable inductor, and the third core is used to create a high frequency transformer effect. Advantages of saturable inductor sensors include high resolution, high accuracy, low offset and gain drift, and large bandwidth (up to 500 kHz). Drawbacks of saturable inductor technologies include limited bandwidth for simpler design, relatively high secondary power consumption, and risk of current or voltage noise injection into the primary conductor.
Magneto Resistive current sensor
A magneto-resistor (MR) is a two terminal device which changes its resistance parabolically with applied magnetic field. This variation of the resistance of MR due to the magnetic field is known as the Magnetoresistive Effect effect. It is possible to build structures in which the electrical resistance varies as a function of applied magnetic field. These structures can be used as magnetic sensors. Normally these resistors are assembled in a bridge configuration to compensate for thermal drift.[7] Popular magneto resistance-based sensors are: Anisotropic Magneto Resistance (AMR), Giant Magneto Resistance (GMR), Giant Magneto Impendence (GMI) and Tunnel Magneto Resistance (TMR). All these MR-based sensors have higher sensitivity compared to Halleffect sensors. Despite of this, these sensors (GMR, CMR, and TMR) are still more expensive than Hall-effect devices, have serious drawbacks related with nonlinear behavior, distinct thermal drift, and a very strong external field can permanently alter the sensor behavior (GMR). GMI and TMR sensors are even more sensitive than GMR based sensors, but still in the test phase and no commercial version are available today.
See also
References
- ↑ Costa, F.; Poulichet, P.; Mazaleyrat, F.; Labouré, E. (1 February 2001). "The Current Sensors in Power Electronics, a Review". EPE Journal. 11 (1): 7–18. ISSN 0939-8368.
- ↑ Malewski, R.; Nguyen, C. T.; Feser, K.; Hylten-Cavallius, N. (1 March 1981). "Elimination of the Skin Effect Error in Heavy-Current Shunts". IEEE Transactions on Power Apparatus and Systems. PAS-100 (3): 1333–1340. ISSN 0018-9510.
- ↑ Castelli, F. (1 October 1999). "The flat strap sandwich shunt". IEEE Transactions on Instrumentation and Measurement. 48 (5): 894–898. ISSN 0018-9456.
- ↑ Spaziani, Larry (1997). "Using Copper PCB Etch for Low Value Resistance". Texas Instruments. DN-71.
- ↑ Ziegler, S.; Iu, H. H. C.; Woodward, R. C.; Borle, L. J. (1 June 2008). "Theoretical and practical analysis of a current sensing principle that exploits the resistance of the copper trace". 2008 IEEE Power Electronics Specialists Conference: 4790–4796.
- ↑ LEM International SA (June 2011). "High Precision Current Transducers Catalogue" (version 1).
- ↑ Ziegler, S.; Woodward, R. C.; Iu, H. H. C.; Borle, L. J. (1 April 2009). "Current Sensing Techniques: A Review". IEEE Sensors Journal. 9 (4): 354–376. ISSN 1530-437X.
External links
- Current measurement applications handbook
- Ensure the Safety of Door Openers with Current Measurement
- Sensing Elements for Current Measurements
- Hall Effect sensing and and application pdf
- Non-Intrusive Hall-Effect Current-Sensing Techniques
- Flux gate sensor explanation
- Basic Introduction to the use of Magnetoresistive Sensors
- Trace resistance calculator