Delamination
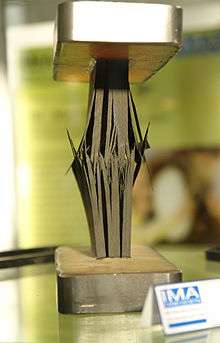
Delamination is a mode of failure for composite materials[1] and steel.[2] In laminated materials, repeated cyclic stresses, impact, and so on can cause layers to separate, forming a mica-like structure of separate layers, with significant loss of mechanical toughness. Delamination also occurs in reinforced concrete structures subject to reinforcement corrosion, in which case the oxidized metal of the reinforcement is greater in volume than the original metal. The oxidized metal therefore requires greater space than the original reinforcing bars, which causes a wedge-like stress on the concrete. This force eventually overcomes the relatively weak tensile strength of concrete, resulting in a separation (or delamination) of the concrete above and below the reinforcing bars.
Fiber pull-out (another form of failure mechanism) and delamination can occur, in part, due to weak adhesive bonding between the fibers and the polymer matrix.[3]
Delamination failure may be detected in the material by its sound; solid composite has bright sound, while delaminated part sounds dull, reinforced concrete sounds solid, whereas delaminated concrete will have a light drum-like sound when exposed to a dragged chain pulled across its surface. Bridge decks in cold climate countries which use de-icing salts and chemicals are commonly subject to delamination and as such are typically scheduled for annual inspection by chain-dragging as well as subsequent patch repairs of the surface. Other nondestructive testing methods are used, including embedding optical fibers coupled with optical time domain reflectometer testing of their state, testing with ultrasound, radiographic imaging, and infrared imaging.
Some manufacturers of carbon composite bike frames suggest disposing of the frame after a crash, because the impact could have created flaws inside the material.
As there is increasing use of composite materials in aircraft construction (e.g. the Boeing 787 and the Airbus A350), delamination is an air safety concern, especially in the tail sections of the airplanes.
For aircraft, satellite, and other critical components, the requirements for quality may be very strict. Using a test method, such as manual tap testing, to produce audible sounds is not reliable. Small defects, or those several layers deep, may be very difficult, if not impossible, to detect. The change in pitch becomes slight enough that the human ear cannot resolve it. Using sound is also subjective and dependent on the inspector's quality of hearing as well as judgement. Any intentional variations in the part may also change the pitch of the produced sound, influencing the inspection. Some of these variations include ply overlaps, ply count change gores, core density change (if used), and geometry. While these features can all exist in the same part and sound different from each other, none are defects. Inspection methods such as ultrasound, infrared thermography, shearography, and radiography produce quantifiable results and all have much higher resolution capability than manual tap testing.
References
- ↑ WJ Cantwell, J Morton (1991). "The impact resistance of composite materials -- a review". Composites. 22 (5): 347–62. doi:10.1016/0010-4361(91)90549-V.
- ↑ B. L. Bramfitt, A. R. Marder (1979). "A Study of the Delamination Behavior of aa Very Low-Carbon Steel". Metallurgical Transactions A.
- ↑ Serope Kalpakjian; Steven R. Schmid (2001). Manufacturing Engineering and Technology. ISBN 978-0-13-017440-6.
- ↑ Kvalbein, Martine; Thorvaldsen, Tom. "Non-destructive testing/inspection of composite materials – acoustic impact testing, TV holography and shearography" (PDF). Norwegian Defence Research Establishment (FFI). Retrieved 29 April 2016.