Non-synchronous transmission
Transmission types |
---|
Manual |
Automatic |
Bicycle gearing |
A non-synchronous transmission is a form of transmission based on gears that do not use synchronizing mechanisms. They are found primarily in various types of agricultural and commercial vehicles. Because the gear boxes are engineered without "cone and collar" synchronizing technology, the non-synchronous transmission type requires an understanding of gear range, torque, engine power, range selector, multi-functional clutch, and shifter functions. Engineered to pull tremendous loads, often equal to or exceeding 40 tons, some vehicles may also use a combination of transmissions for different mechanisms. An example would be a power take-off.[1]
History
In 1890, Panhard used a chain-drive with a Daimler engine in a horseless carriage. Industrial marketing has since then coined spectacular names for various vehicle parts. Changing from the Locomobile,[2] a 1906 race-car to what is now called the automobile, advertisers used design wording from the engineering departments to give new ideas a desirable appeal for sales promotions. From 1932, synchronizer mechanisms began to appear in automotive transmissions. The split-off of automotive transmission types that has prevailed in engineering designs uses three major categories: automatic, manual, and non-synchronous. Some of the differences are improvements, including the continuously variable transmission installed in hybrid vehicles that are powered partly by an internal combustion engine, and partly by an electric motor. The concepts of transmission continue to employ methods for transferring the most conceivably efficient use of power.
How non-synchronization works
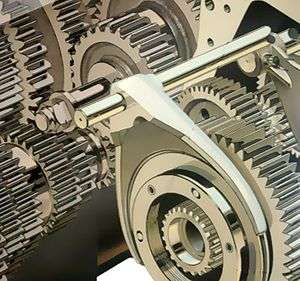
Non-synchronous transmissions are engineered[3] with the understanding that a trained operator will be shifting gears in a known coordination of timing. Commercial vehicle operators use a double-clutching technique that is taught in driver's trade schools. The most skillful drivers can shift these transmissions without using the clutch by bringing the engine to exactly the right rpm in neutral before attempting to complete a shift, a technique called "float-shifting." With payloads of cargo ranging in commercial freight of 80,000 lbs (40 tons (short) or 36.3 tonnes) or more, some heavy haulers have over 24 ″gears″ (i.e., combinations of gear ratios) that an operator will shift through before reaching a top cruising speed of 70 mph (113 km/h). Many low-low (creeper) gears are used in farm equipment to plow, till, or harvest. Also see Engineering vehicle. An inexperienced operator could suddenly find a piece of heavy equipment stuck in the wrong gear under full power, or even worse unable to shift a runaway vehicle from neutral into a gear for braking effect when headed down a steep slope, unless he or she possessed the synchronizing skill and understood torque issues in non-synchronous transmissions. Many mountain roads require heavy equipment operators to remain in gear and not shift while operating down a steep grade. For more details about steep grade operation see either jake brake, or engine brake. Many other circumstances face operators of non-synchronous transmissions. Safety and operator skills need to be learned before operating any of these types of vehicles.
Double clutching (commercial motor vehicle)

Operators of 18-wheelers, farm equipment, tractors and other heavy equipment learn to float the transmission in and out of gear, beginning with dis-engaging the clutch by pressing the clutch pedal only part way, enough to pull the transmission out of gear, re-engaging the clutch in neutral (between gears by letting the clutch pedal all the way back out) to let the engine revolutions decelerate enough for the idle sprockets to shift, and free gear shafts to slow their revolutions per minute (RPM), then dis-engage the clutch again (by pressing the clutch pedal only part way to the floor) a second time, and float the higher gear into engaging the drive coupling and flywheel and engaging the clutch plates. Professional operators of heavy equipment take extensive safety training before ever learning how to double-clutch. Once an operator is familiar with range, range selector, rpm, velocity, and torque of heavy equipment like an 18-wheeler, he can begin to anticipate when to shift gears. Operators become familiar with ranges of gears. They also learn not to leave their foot on the clutch while driving, because these types of transmissions use the clutch for some very different purposes. The depth the clutch is depressed to the floor will determine what the clutch will be doing as a synchronizing function.
Clutch brake
Unlike any other type of transmission, non-synchronous transmissions often have a mechanism for slowing down, or stopping an idle gear. In commercial motor vehicles, this mechanism is called the clutch brake, and is used by depressing the clutch all the way to the floor, or pressing a button on the top of the gear lever. This is useful in 18-wheelers that have just started their diesel engines, and are releasing parking locks, and engaging the transmission from a stop. The clutch brake not only slows or stops the idle gear axis, but can also prevent shifting into gear until the clutch pedal is released a few inches off the floor. In order to shift into gear, the clutch must be half way off the floor, otherwise the clutch brake will prevent the transmission from being shifted into or out of gear. Mechanics must often repair or replace the clutch brake in a non-synchronous transmission when an inexperienced operator wears it out, it becomes inoperable, or has lost its function.
Comparison of transmissions
Non-synchronous transmissions[4] are designed to depend upon an operator experienced in changing gears. The operators must understand how to shift the transmission into and out of gear. Many learn how to do this in certifying schools.
All automatic transmissions have synchronizing mechanisms. Most manual transmissions also have synchronizers.[5] But there are still other types of transmissions used mostly in commercial applications that are non-synchronous.
Fully synchronous, hydrau-pneumatic systems are designed to change gears based on engine performance and other velocity indicators, delivering torque to drive wheels. These transmissions have synchronizing mechanisms (called cone and collar synchronizers) that are designed to keep gear dog-teeth from being broken off.
Heavy equipment for industrial, military, or farm use has different torque and load issues. They have unique stress from massive horsepower that would make converter faces shear. For the reasons of engineering a dependable, longer-life piece of equipment, these machines often use non-synchronous transmissions.
Any transmission that requires the operator to manually synchronize engine crank-shaft revolutions (RPM) with drive-shaft revolutions is non-synchronous.
See also
Notes
- ↑ "6-10 Bolt Mechanical Power Takeoff". Retrieved 2007-07-16.
- ↑ "Edison & Ford Museum". Retrieved 2007-07-19.
- ↑ "transmission parts news: index". Retrieved 2007-07-16.
- ↑ "Sec.13Pg13-3Vehicles equipped with Non-synchronous transmission" (PDF). Retrieved 2007-07-18.
- ↑ "Synchronizers; graphic illustration of how they work". Retrieved 2007-07-18.
References
- Core Transmissions-for display only: this is not an endorsement
- ATA - American Trucking Association- not a global reference
- PTDI acronym for Professional Truck Driver Institute - pertains to U.S. only
- Federal Motor Carrier Safety Administration New Hampshire Dept. of Motor Vehicles 2005 Commercial Driver's License Manual, sec. 13.1.11 Section 13 page 13-3 says Double clutch if vehicle is equipped with non-synchronized transmission. (note: this file is a complete manual in Adobe Acrobat format with a file size of over 10 Megabytes).