Roller burnishing
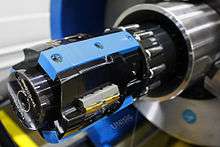
Roller burnishing is a method of cold working metal surfaces to induce compressive residual stresses and enhance surface roughness qualities. The tooling typically consists of a hardened sphere or cylindrical roller. These tools are pressed onto/across the part being processed. The part (or the tool in some applications) must be moving at a constant rate of speed, for example in the case of roller burnishing a part on a lathe, the part is spinning and the burnishing tool is moved across the surface as a constant rate; therefore, producing a very consistent finish across the part. Another application is thrust bearing surfaces of some production crankshafts. A dual roller (cylindrical) tool is moved into the thrust bearing journal of a crankshaft, while the crankshaft is spinning the tool is indexed (so each roller is perpendicular to the thrust surface while backing each other up) deforming the surfaces. So the diameters of each roller added together (compensated for elastic deformation) equals the finish dimension of the thrust bearing.
In deep hole machining, a roller burnishing tool is often combined with skiving knives on the same tool. The skiving knives pass first, scraping the inside layer of metal, followed by the burnishing rollers, which cold work the tube to create a mirror surface finish. Skive-burnishing is often used in hydraulic cylinder applications. This process can happen on a deep hole drilling machine or a dedicated skiving machine.