Alnico

Alnico is an acronym[1] referring to a family of iron alloys which in addition to iron are composed primarily of aluminium (Al), nickel (Ni) and cobalt (Co), hence al-ni-co. They also include copper, and sometimes titanium. Alnico alloys are ferromagnetic, with a high coercivity (resistance to loss of magnetism) and are used to make permanent magnets. Before the development of rare earth magnets in the 1970s, they were the strongest type of permanent magnet. Other trade names for alloys in this family are: Alni, Alcomax, Hycomax, Columax, and Ticonal.[2]
The composition of alnico alloys is typically 8–12% Al, 15–26% Ni, 5–24% Co, up to 6% Cu, up to 1% Ti, and the balance is Fe. The development of alnico began in 1931, when T. Mishima in Japan discovered that an alloy of iron, nickel, and aluminum had a coercivity of 400 oersted (Oe; 32 kA/m), double that of the best magnet steels of the time.[3]
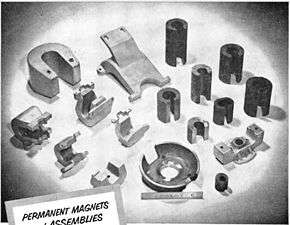
Properties
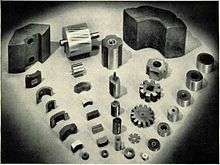
Alnico alloys make strong permanent magnets, and can be magnetised to produce strong magnetic fields. Of the more commonly available magnets, only rare-earth magnets such as neodymium and samarium-cobalt are stronger. Alnico magnets produce magnetic field strength at their poles as high as 1500 gauss (0.15 tesla), or about 3000 times the strength of Earth's magnetic field. Some brands of alnico are isotropic and can be efficiently magnetized in any direction. Other types, such as alnico 5 and alnico 8, are anisotropic, with each having a preferred direction of magnetization, or orientation. Anisotropic alloys generally have greater magnetic capacity in a preferred orientation than isotropic types. Alnico's remanence (Br) may exceed 12,000 G (1.2 T), its coercivity (Hc) can be up to 1000 oersted (80 kA/m), its energy product ((BH)max) can be up to 5.5 MG·Oe (44 T·A/m). This means alnico can produce a strong magnetic flux in closed magnetic circuits, but has relatively small resistance against demagnetization. The field strength at the poles of any permanent magnet depends very much on the shape and is usually well below the remanence strength of the material.
Alnico alloys have some of the highest Curie temperatures of any magnetic material, around 800 °C (1,470 °F), although the maximum working temperature is normally limited to around 538 °C (1,000 °F).[4] They are the only magnets that have useful magnetism even when heated red-hot.[5] This property, as well as its brittleness and high melting point, is the result of the strong tendency toward order due to intermetallic bonding between aluminium and its other constituents. They are also one of the most stable magnets if they are handled properly. Alnico magnets are electrically conductive, unlike ceramic magnets.
Magnetic Materials | Density (g/cm) | Maximum Energy Product BH (max) (MGOe) | Residual Induction Br (G) | Coercive Force Hc (Oe) | Intrinsic Coercive Force Hc (Oe) | Normal Maximum Operating Temp |
---|---|---|---|---|---|---|
Alnico 5 (cast) | 7.3 | 5.5 | 12800 | 640 | 640 | 975 °F (524 °C) |
Alnico 8 (cast) | 7.3 | 5.3 | 8200 | 1650 | 1860 | 1,020 °F (549 °C) |
Alnico 5 (sintered) | 6.9 | 3.9 | 10900 | 620 | 630 | 975 °F (524 °C) |
Alnico 8 (sintered) | 7.0 | 4.0 | 7400 | 1500 | 1690 | 1,020 °F (549 °C) |
As of 2008, Alnico magnets cost about $44/kg ($20/pound) or $4.30/BHmax.[6]
Classification
Alnico magnets are traditionally classified using numbers assigned by the Magnetic Materials Producers Association (MMPA), for example, alnico 3 or alnico 5. These classifications indicate chemical composition and magnetic properties. (The classification numbers themselves do not have any direct relation to the properties of the magnet; for instance, a higher number does not necessarily indicate a stronger magnet.)[7]
These classification numbers, while still in use, have been deprecated in favor of a new system by the MMPA, which designates Alnico magnets based on maximum energy product in megagauss-oersteds and intrinsic coercive force as kilooersteds, as well as an IEC classification system.[7]
Manufacturing process

Alnico magnets are produced by casting or sintering processes.[8] Anisotropic alnico magnets are oriented by heating above a critical temperature, and cooling in the presence of a magnetic field. Both isotropic and anisotropic alnico require proper heat treatment to develop optimum magnetic properties—without it alnico's coercivity is about 10 Oe, comparable to technical iron, which is a soft magnetic material. After the heat treatment alnico becomes a composite material, named "precipitation material"—it consists of iron and cobalt rich[9] precipitates in rich-NiAl matrix.
Alnico's anisotropy is oriented along the desired magnetic axis by applying an external magnetic field to it during the precipitate particle nucleation, which occurs when cooling from 900 °C (1,650 °F) to 800 °C (1,470 °F), near the Curie point. Without an external field there are local anisotropies of different orientations, due to spontaneous magnetization. The precipitate structure is a "barrier" against magnetization changes, as it prefers few magnetization states requiring much energy to get the material into any intermediate state. Also, a weak magnetic field shifts the magnetization of the matrix phase only, and is reversible..
Uses
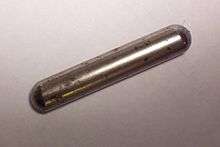
Alnico magnets are widely used in industrial and consumer applications where strong permanent magnets are needed; examples are electric motors, electric guitar pickups, microphones, sensors, loudspeakers, magnetron tubes, and cow magnets. In many applications they are being superseded by rare earth magnets, whose stronger fields (Br) and larger energy products (BHmax) allow smaller size magnets to be used for a given application.
References
- ↑ Hellweg, Paul. The Insomniac's Dictionary. Facts On File Publications. p. 115. ISBN 0-8160-1364-0.
- ↑ Brady, George Stuart; Clauser, Henry R; Vaccari, John A (2002). Materials Handbook: An Encyclopedia for Managers. McGraw-Hill Professional. p. 577. ISBN 0-07-136076-X.
- ↑ Cullity, B. D.; C. D. Graham (2008). Introduction to Magnetic Materials. Wiley-IEEE. p. 485. ISBN 0-471-47741-9.
- ↑ Arnold-Alnico Magnets. Arnoldmagnetics.com. Retrieved on 2011-07-30.
- ↑ Hubert, Alex; Rudolf Schäfer (1998). Magnetic domains: the analysis of magnetic microstructures. Springer. p. 557. ISBN 3-540-64108-4.
- ↑ Frequently Asked Questions. Magnetsales.com. Retrieved on 2011-07-30.
- 1 2 "Standard Specifications for Permanent Magnet Materials (MMPA Standard No. 0100-00)" (PDF). Magnetic Materials Producers Association. Retrieved 9 September 2015.
- ↑ Campbell, Peter (1996). Permanent magnet materials and their application. UK: Cambridge University Press. pp. 35–38. ISBN 0-521-56688-6.
- ↑ "Evolution of Fe-Co rich particles in Alnico 8 alloy thermomagnetically treated at 800°C". Materials science and technology. 16 (9): 1023–1028. 2000. doi:10.1179/026708300101508810.
Further reading
- Alnico Magnet Bars & Grades,
- Physical Review: 77p839_2, 80p112_2, 80p302_1, 81p478_1
- Review of Modern Physics 17p15, 25p316_1
- 29p299, 31pS82, 40p1308
- MMPA 0100-00, Standard Specifications for Permanent Magnet Materials