Concrete mixer
A concrete mixer (often mistakenly called a cement mixer) is a device that homogeneously combines cement, aggregate such as sand or gravel, and water to form concrete. A typical concrete mixer uses a revolving drum to mix the components. For smaller volume works portable concrete mixers are often used so that the concrete can be made at the construction site, giving the workers ample time to use the concrete before it hardens. An alternative to a machine is mixing concrete by hand. This is usually done in a wheelbarrow; however, several companies have recently begun to sell modified tarps for this purpose.
The concrete mixer was invented by Columbus industrialist Gebhardt Jaeger.[1]
Industrial mixers
Today's market increasingly requires consistent homogeneity and short mixing times for the industrial production of ready-mix concrete, and more so for precast/prestressed concrete. This has resulted in refinement of mixing technologies for concrete production. Different styles of stationary mixers have been developed, each with its own inherent strengths targeting different parts of the concrete production market. The most common mixers used today fall into 3 categories:
- Twin-shaft mixers, known for their high intensity mixing, and short mixing times. These mixers are typically used for high strength concrete, RCC and SCC, typically in batches of 2–6 m3 (2.6–7.8 cu yd).
- Vertical axis mixers, most commonly used for precast and prestressed concrete. This style of mixer cleans well between batches, and is favoured for coloured concrete, smaller batches (typically 0.75–3 m3 or 0.98–3.92 cu yd), and multiple discharge points. Within this category, the Pan mixers are losing popularity to the more efficient Planetary (or counter-current) mixers[2] as the additional mixing action helps in production of more critical concrete mixes (colour consistency, SCC, etc.).
- Drum mixers (reversing drum mixer and tilting drum mixers), used where large volumes (batch sizes of 3–9 m3 or 3.9–11.8 cu yd) are being produced. This type of mixer dominates the ready-mixed market as it is capable of high production speeds, ideal for slump concrete, and where overall cost of production is important. Drum mixers have the lowest maintenance and operating cost of the three styles of mixers.
All the mixer styles have their own inherent strengths and weaknesses, and all three styles of mixers are used throughout the world to varying degrees of popularity.
Trucks and trailers
Concrete mixing transport trucks

Special concrete transport trucks (in–transit mixers) are made to transport and mix concrete up to the construction site. They can be charged with dry materials and water, with the mixing occurring during transport. They can also be loaded from a "central mix" plant, with this process the material has already been mixed prior to loading. The concrete mixing transport truck maintains the material's liquid state through agitation, or turning of the drum, until delivery. The interior of the drum on a concrete mixing truck is fitted with a spiral blade. In one rotational direction, the concrete is pushed deeper into the drum. This is the direction the drum is rotated while the concrete is being transported to the building site. This is known as "charging" the mixer. When the drum rotates in the other direction, the Archimedes' screw-type arrangement "discharges", or forces the concrete out of the drum. From there it may go onto chutes to guide the viscous concrete directly to the job site. If the truck cannot get close enough to the site to use the chutes, the concrete may be discharged into a concrete pump, connected to a flexible hose, or onto a conveyor belt which can be extended some distance (typically ten or more metres). A pump provides the means to move the material to precise locations, multi-floor buildings, and other distance prohibitive locations. Buckets suspended from cranes are also used to place the concrete. The drum is traditionally made of steel but on some newer trucks as a weight reduction measure, fibreglass has been used.
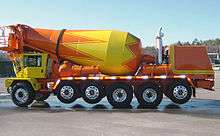

"Rear discharge" trucks require both a driver and a "chuteman" to guide the truck and chute back and forth to place concrete in the manner suitable to the contractor. Newer "front discharge" trucks have controls inside the cab of the truck to allow the driver to move the chute in all directions. The first front discharge mixer was designed and built by Royal W. Sims of Holladay, Utah.
Concrete mixers are equipped with anywhere from two axles and up. Four, five and six axle trucks are the most common with the number being determined by the load and local legislation governing allowable loads on the road. These are necessary to distribute the load evenly and allow operation on weight restricted roads and to reduce wear and tear on normal roads. A two or three axle truck during the winter when road weight limits are reduced has no usable payload in many jurisdictions. Other areas may require expensive permits to operate. Additional axles other than those used for steering ("steers") or drivetrain ("drives") may be installed between the steers and drives or behind the drives. Mixers commonly will have multiple steering axles as well, which generally result in very large turning radii. To facilitate maneuvering the additional axles may be "lift axles" which allows them to be raised off the ground so that they do not scrub (get dragged sideways across the ground) on tight turns, or increase the vehicle's turning radius. Axles installed behind the drives are known as "tag axles" or "booster axles", and are often equipped to turn opposite to the steering axle to reduce scrubbing and automatically lift when the truck is put into a reverse gear.
Tractor trailer combination mixers where the mixer is installed on a trailer instead of a truck chassis are used in some jurisdictions, such as the province of Quebec where even 6 axle trucks would have trouble carrying a useful load.
Concrete mixers generally do not travel far from their plant, as the concrete begins to set as soon as it is in the truck. Many contractors require that the concrete be in place within 90 minutes after loading. If the truck breaks down or for some other reason the concrete hardens in the truck, workers may need to enter the barrel with jackhammers.[3]
Stephen Stepanian filed a patent application for the first truck mixer in 1916.[4] Trucks weigh 20,000 to 30,000 pounds (9,070 to 13,600 kg), and can carry roughly 40,000 pounds (18,100 kg) of concrete although many varying sizes of Mixer Truck are currently in use. The most common truck capacity is 8 cubic yards (6.1 m3).
Most concrete mixers in the UK are limited to a speed of 56 miles per hour (90 km/h).
Concrete mixer trailers
A variant of standard concrete transportation is the concrete or cement mixing trailer. These small versions of a transit-mix truck are used to supply short loads of concrete. These cart-away style trailers have a concrete mixing drum with a capacity of between 1 and 1.75 cubic yards (0.76 and 1.34 m3). Cart-aways are usually pulled behind a pick-up truck and batched from smaller batching systems. The mixing trailer system is popular with rental yards and building material locations, who use them to supply ready-mix to their regular customer base.
Metered concrete trucks
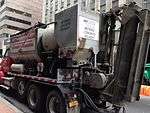
Metered concrete trucks or volumetric mobile mixers are trucks that contain concrete ingredient materials and water to be mixed on the truck at the job site to make and deliver concrete according to the amount needed.[5]
On-site and portable concrete mixers

For smaller jobs, such as residential repairs, renovations, or hobbyist-scale projects, many cubic yards of concrete are usually not required. Bagged cement is readily available in small-batch sizes, and aggregate and water are easily obtained in small quantities for the small work site. To service this small-batch concrete market, there are many types of small portable concrete mixers available
A typical portable concrete mixer uses a small revolving drum to mix the components. For smaller jobs the concrete made at the construction site has no time lost in transport, giving the workers ample time to use the concrete before it hardens.
Portable concrete mixers may be powered by a gasoline engine, although it is more common that they are powered by electric motors using standard mains current.
These concrete mixers are further divided based on their loading mechanism. Cement, sand and other aggregates are loaded in a hydraulically operated hopper and then poured in the mixing drum for final mixing and then can be unloaded by tilting the drum. While in Hand Feed Concrete Mixers, cement, sand and other aggregates are directly added to the mixing drum manually. These both type of concrete mixers are highly popular and used in regular construction activities in Africa, some Middle Eastern Countries and in the Indian subcontinent.
Self loading Concrete Mixers
Self Loading Concrete Mixers are unique machines designed to batch, mix and transport concrete. These mixers consist of a rotating drum mounted on an operator-driven cab-mounted chassis frame fitted with a loading bucket.

The operator of the Self Loading Concrete Mixer batches and introduces the ingredients required for mixing concrete viz., cement, stone aggregates etc., into the drum using the loading bucket. The drum is usually of reversible type, tilt type or a combination of both. A predetermined volume of water is discharged to the drum via a water dispensing unit. The mixture is rotated at mixing speeds within the drum until concrete discharge via a fitted chute.
Self-loading concrete mixers are suited for construction sites where Concrete batching plants are unavailable, underfoot conditions are not suited for Concrete transit mixer trucks or labor availability is scarce or constrained. Applications include urban and rural construction, concrete pavement maintenance, bridge and tunnel construction, township-level highways construction, foundation construction, national defense facilities, construction of high-speed railway etc.
In fiction
- In Thomas and Friends, Patrick is a concrete mixer who is dark red and cream.
- Bob the Builder - Dizzy is an orange on-site and portable concrete mixer and Tumbler is a yellow and green concrete transport truck (commonly called a cement truck). In the reboot of the series Two-Tonne has a concrete mixer trailer.
- In the various Transformers continuities, Mixmaster is a robot that can change into a cement truck.
- The Cement Truck, a gothic sculpture by Wim Delvoye.
Television
- On an episode of MythBusters, experiments were done to see if dynamite can be used to clean out hardened concrete from inside of a mixer truck, with limited practical results. For the finale, an excessive amount of explosive (800 lbs of commercial blasting agent) was used, and was detonated from a long distance away. The explosion left a very clear crater, and only the engine block was recovered.
- Nowadays the concrete buildup (hardened concrete in the drum) is removed by a remote controlled high pressure water robot. A device that contributes a solution to improve health and safety issues related to working in the confined spaces of the concrete mixerdrum.
- On an episode of Wrecked - Life In The Crash Lane, O'Hare Towing responds to a call on a construction site to recover a mixer truck that had become stuck in mud, continuing to sink and threatening to roll over. After several unsuccessful attempts to hoist the mixer using a heavy rotator wrecker, the foreman informs the wrecker driver that the mixing drum contains approximately 5 cubic yards of concrete, and asks whether emptying the drum would lighten the truck enough to enable the wrecker to recover it. After emptying the drum, the wrecker operator is able to winch the mixer truck out of the mud & onto solid ground.
- In season 5, episode 1 of TV series MacGyver, the series' main character uses an engine from a small portable gasoline powered concrete mixer, in order to build an aeroplane.[6]
See also
References
![]() |
Wikimedia Commons has media related to Cement mixers. |
- ↑ Hunker, Henry L. (2000). Columbus, Ohio: A Personal Geography. Ohio State University Press. p. 196. ISBN 978-0-8142-0857-1.
- ↑ "Photos planetary mixer". Rometa Editor.
- ↑ "Control Technology for Ready-mix Truck Drum Cleaning" (PDF). U.S. Department of Health and Human Services. 31 May 2001. Retrieved 21 October 2013.
- ↑ Portland Cement Association: History of Ready Mixed Concrete industry site
- ↑ Casey, Jon M. "Parmer Metered Concrete offers precision and quality". Hard Hat News. Retrieved 24 November 2014.
- ↑ ""MacGyver" Legend of the Holy Rose: Part 1 (TV Episode 1989) - IMDb". imdb.com. Retrieved 29 May 2016.