Pitting corrosion
Pitting corrosion, or pitting, is a form of extremely localized corrosion that leads to the creation of small holes in the metal. The driving power for pitting corrosion is the depassivation of a small area, which becomes anodic while an unknown but potentially vast area becomes cathodic, leading to very localised galvanic corrosion. The corrosion penetrates the mass of the metal, with a limited diffusion of ions. The mechanism of pitting corrosion is probably the same as crevice corrosion.
Mechanism
The more conventional explanation for pitting corrosion is that it is an autocatalytic process. Metal oxidation results in localised acidity that is maintained by the spatial separation of the cathodic and anodic half-reactions, which creates a potential gradient and electromigration of aggressive anions into the pit.[1] For example, when a metal is present in an oxygenated NaCl electrolyte, the pit acts as anode and the metal surface acts as cathode. The localised production of positive metal ions in the pit gives a local excess of positive charge which attracts the negative chlorine ions from the electrolyte to produce charge neutrality. The pit contains a high concentration of MCl molecules which react with water to produce HCl, the metal hydroxide, and H+ ions, accelerating the corrosion process.In the pit, the oxygen concentration is essentially zero and all of the cathodic oxygen reactions take place on the metal surface outside the pit. The pit is anodic and the locus of rapid dissolution of the metal.[2] The metal corrosion initiation is autocatalytic in nature however it's propagation isn't.
This kind of corrosion is extremely insidious, as it causes little loss of material with the small effect on its surface, while it damages the deep structures of the metal. The pits on the surface are often obscured by corrosion products.
Pitting can be initiated by a small surface defect, being a scratch or a local change in composition, or a damage to the protective coating. Polished surfaces display higher resistance to pitting.
Susceptible alloy / environment combinations
Pitting Corrosion is defined by localised attack (microns - millimetres in diameter) in an otherwise passive surface and only occurs for specific alloy / environment combinations. Thus, this type of corrosion typically occurs in alloys that are protected by a tenacious (passivating) oxide film such as stainless steels, nickel alloys, aluminium alloys in environments that contain an aggressive species such as chlorides (Cl-). In contrast, alloy / environment combinations where the passive film is not very protective usually will not produce pitting corrosion. A good example of the importance of environment / alloy combinations is carbon steel. In environments where the pH is less than 10, carbon steel does not form a passivating oxide film and the addition of chloride results in uniform attack over the entire surface. However, at pH greater than 10 the oxide is very protecting and the addition of chloride results in pitting corrosion.
Besides chlorides, other anions implicated in pitting include thiosulfates (S2O32−), fluorides and iodides. Stagnant water conditions favour pitting. Thiosulfates are particularly aggressive species and are formed by partial oxidation of pyrite, or partial reduction of sulfate. Thiosulfates are a concern for corrosion in many industries: sulfide ores processing, oil wells and pipelines transporting soured oils, Kraft paper production plants, photographic industry, methionine and lysine factories.
Corrosion inhibitors, when present in sufficient amount, will provide protection against pitting. However, too low level of them can aggravate pitting by forming local anodes.
Engineering failures due to pitting corrosion
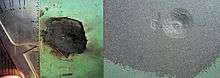
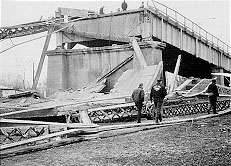
A single pit in a critical point can cause a great deal of damage. One example is the explosion in Guadalajara, Mexico on April 22, 1992, when gasoline fumes accumulated in sewers destroyed kilometres of streets. The vapours originated from a leak of gasoline through a single hole formed by corrosion between a steel gasoline pipe and a zinc-plated water pipe.[3] Firearms can also suffer from pitting, most notably in the bore of the barrel when corrosive ammunition is used and the barrel is not cleaned soon afterwards. Deformities in the bore caused by pitting can greatly reduce the firearm's accuracy. To prevent pitting in firearm bores, most modern firearms have a bore lined with chromium.
Pitting corrosion can also help initiate stress corrosion cracking, as happened when a single eyebar on the Silver Bridge, West Virginia failed and ended up killing 46 people on the bridge in December, 1967.[4]
See also
References
- ↑ ASM Handbook, Volume 13, "Corrosion", ISBN 0-87170-007-7, ASM International, 1987
- ↑ https://www.princeton.edu/~maelabs/mae324/12/pitcorrosion.htm
- ↑ "Sewer Explosion due to Corrosion". Corrosion Doctors.
- ↑ Silver Bridge Collapse, Corrosion Doctors, read May 13, 2016
External links
- Pitting Corrosion - Corrosion Doctors
- Pitting Corrosion Pitting Corrosion Theory