Kaizen
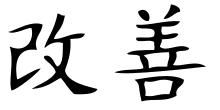
Kaizen, 改善, is Japanese for "improvement". When used in the business sense and applied to the workplace, kaizen refers to activities that continuously improve all functions and involve all employees from the CEO to the assembly line workers. It also applies to processes, such as purchasing and logistics, that cross organizational boundaries into the supply chain.[1] It has been applied in healthcare,[2] psychotherapy,[3] life-coaching, government, banking, fantasy hockey, and other industries.
By improving standardized programme and processes, kaizen aims to eliminate waste (see lean manufacturing). Kaizen was first implemented in several Japanese businesses, CL69 after the Second World War, influenced in part by American business and quality management teachers who visited the country. It has since spread throughout the world[4] and is now being implemented in environments outside of business and productivity.
Overview
The Sino-Japanese word "kaizen" simply means "change for better", with no inherent meaning of either "continuous" or "philosophy" in Japanese dictionaries or in everyday use. The word refers to any improvement, one-time or continuous, large or small, in the same sense as the English word "improvement".[5] However, given the common practice in Japan of labeling industrial or business improvement techniques with the word "kaizen" (for lack of a specific Japanese word meaning "continuous improvement" or "philosophy of improvement"), especially in the case of oft-emulated practices spearheaded by Toyota, the word "kaizen" in English is typically applied to measures for implementing continuous improvement, or even taken to mean a "Japanese philosophy" thereof. The discussion below focuses on such interpretations of the word, as frequently used in the context of modern management discussions. Two kaizen approaches have been distinguished:[6]
- flow kaizen;
- process kaizen.
The former is oriented towards the flow of materials and information, and is often identified with the reorganization of an entire production area, even a company. The latter means the improvement of individual workstands. Therefore, improving the way production workers do their job is a part of a process kaizen. The use of the kaizen model for continuous improvement demands that both flow and process kaizens are used, although process kaizens are used more often to focus workers on continuous small improvements. In this model, operators mostly look for small ideas which, if possible, can be implemented on the same day. This is in contrast to traditional models of work improvement, which generally have a long lag between concept development and project implementation. In the traditional model, the time between concept development and project implementation is very long. In the kaizen model, workers mostly look for small ideas and improvements which can be implemented on the same day.
Kaizen is a daily process, the purpose of which goes beyond simple productivity improvement. It is also a process that, when done correctly, humanizes the workplace, eliminates overly hard work ("muri"), and teaches people how to perform experiments on their work using the scientific method and how to learn to spot and eliminate waste in business processes. In all, the process suggests a humanized approach to workers and to increasing productivity: "The idea is to nurture the company's people as much as it is to praise and encourage participation in kaizen activities."[7] Successful implementation requires "the participation of workers in the improvement."[8] People at all levels of an organization participate in kaizen, from the CEO down to janitorial staff, as well as external stakeholders when applicable. Kaizen is most commonly associated with manufacturing operations, as at Toyota, but has also been used in non-manufacturing environments.[9] The format for kaizen can be individual, suggestion system, small group, or large group. At Toyota, it is usually a local improvement within a workstation or local area and involves a small group in improving their own work environment and productivity. This group is often guided through the kaizen process by a line supervisor; sometimes this is the line supervisor's key role. Kaizen on a broad, cross-departmental scale in companies, generates total quality management, and frees human efforts through improving productivity using machines and computing power.
While kaizen (at Toyota) usually delivers small improvements, the culture of continual aligned small improvements and standardization yields large results in terms of overall improvement in productivity. This philosophy differs from the "command and control" improvement programs (e g Business Process Improvement) of the mid-twentieth century. Kaizen methodology includes making changes and monitoring results, then adjusting. Large-scale pre-planning and extensive project scheduling are replaced by smaller experiments, which can be rapidly adapted as new improvements are suggested.
In modern usage, it is designed to address a particular issue over the course of a week and is referred to as a "kaizen blitz" or "kaizen event".[10][11] These are limited in scope, and issues that arise from them are typically used in later blitzes. A person who makes a large contribution in the successful implementation of kaizen during kaizen events is awarded the title of "Zenkai".
History
The small-step work improvement approach was developed in the USA under Training Within Industry program (TWI Job Methods).[12] Instead of encouraging large, radical changes to achieve desired goals, these methods recommended that organizations introduce small improvements, preferably ones that could be implemented on the same day. The major reason was that during WWII there was neither time nor resources for large and innovative changes in the production of war equipment.[6] The essence of the approach came down to improving the use of the existing workforce and technologies.
After World War II, to help restore Japan, American occupation forces brought in American experts to help with the rebuilding of Japanese industry while the Civil Communications Section (CCS) developed a management training program that taught statistical control methods as part of the overall material. Homer Sarasohn and Charles Protzman developed and taught this course in 1949-1950. Sarasohn recommended W. Edwards Deming for further training in statistical methods.
The Economic and Scientific Section (ESS) group was also tasked with improving Japanese management skills and Edgar McVoy was instrumental in bringing Lowell Mellen to Japan to properly install the Training Within Industry (TWI) programs in 1951.
Prior to the arrival of Mellen in 1951, the ESS group had a training film to introduce the three TWI "J" programs (Job Instruction, Job Methods and Job Relations) - the film was titled "Improvement in 4 Steps" (Kaizen eno Yon Dankai). Thus "Kaizen" was introduced to Japan. For the pioneering, introduction, and implementation of Kaizen in Japan, the Emperor of Japan awarded the 2nd Order Medal of the Sacred Treasure to Dr. Deming in 1960. Subsequently, the Japanese Union of Science and Engineering (JUSE) instituted the annual Deming Prizes for achievement in quality and dependability of products.
On October 18, 1989, JUSE awarded the Deming Prize to Florida Power & Light Co. (FPL), based in the US, for its exceptional accomplishments in process and quality-control management. FPL became the first company outside Japan to win the Deming Prize.[13]
Implementation
The Toyota Production System is known for kaizen, where all line personnel are expected to stop their moving production line in case of any abnormality and, along with their supervisor, suggest an improvement to resolve the abnormality which may initiate a kaizen.
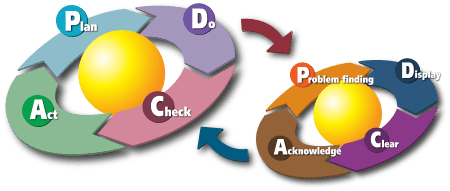
The cycle of kaizen activity can be defined as:
Plan→Do→Check→Act
This is also known as the Shewhart cycle, Deming cycle, or PDCA.
Another technique used in conjunction with PDCA is the 5 Whys, which is a form of root cause analysis in which the user asks a series of 5 "why" questions about a failure that has occurred, basing each subsequent question on the answer to the previous.[15][16] There are normally a series of causes stemming from one root cause,[17] and they can be visualized using fishbone diagrams or tables. The Five Whys can be used as a foundational tool in personal improvement, or as a means to create wealth.[18]
Masaaki Imai made the term famous in his book Kaizen: The Key to Japan's Competitive Success.[1]
Apart from business applications of the method, both Anthony Robbins[19][20] and Robert Maurer have popularized the kaizen principles into personal development principles. In the book One Small Step Can Change Your Life: The Kaizen Way, and CD set The Kaizen Way to Success, Maurer looks at how individuals can take a kaizen approach in both their personal and professional lives.[21][22]
In the Toyota Way Fieldbook, Liker and Meier discuss the kaizen blitz and kaizen burst (or kaizen event) approaches to continuous improvement. A kaizen blitz, or rapid improvement, is a focused activity on a particular process or activity. The basic concept is to identify and quickly remove waste. Another approach is that of the kaizen burst, a specific kaizen activity on a particular process in the value stream.[23] Kaizen facilitators generally go through training and certification before attempting a Kaizen project.
See also
- 5S
- Business process reengineering
- Hansei
- Kaikaku
- Kanban, Kanban Method
- Learning-by-doing
- Management fad
- Mottainai, a sense of regret concerning waste
- Muda
- Overall equipment effectiveness
- Quality circle
- Scrum, an agile methodology for managing product development
- Six Sigma
- Statistical process control
- Theory of constraints
- Total productive maintenance
- TRIZ, the theory of inventive problem solving
- Visual control
References
Notes
- 1 2 Imai, Masaaki (1986). Kaizen: The Key to Japan's Competitive Success. New York: Random House.
- ↑ Weed, Julie (July 10, 2010). "Factory Efficiency Comes to the Hospital". The New York Times.
- ↑ M. M. Feldman (1992). "Audit in psychotherapy: the concept of Kaizen" (PDF). Psychiatric Bulletin. Royal College of Psychiatrists. pp. 334–336.
- ↑ Europe Japan Centre, Kaizen Strategies for Improving Team Performance, Ed. Michael Colenso, London: Pearson Education Limited, 2000
- ↑ "Debunked: "kaizen = Japanese philosophy of continuous improvement"". Retrieved 2009-08-15.
- 1 2 Misiurek, Bartosz (2016). Standardized Work with TWI: Eliminating Human Errors in Production and Service Processes. New York: Productivity Press. ISBN 9781498737548.
- ↑ Tozawa, Bunji; Japan Human Relations Association (1995). The improvement engine: creativity & innovation through employee involvement: the Kaizen teian system. Productivity Press. p. 34. ISBN 978-1-56327-010-9. Retrieved 6 February 2010.
- ↑ Laraia, Anthony C.; Patricia E. Moody; Robert W. Hall (1999). The Kaizen Blitz: accelerating breakthroughs in productivity and performance. John Wiley and Sons. p. 26. ISBN 978-0-471-24648-0. Retrieved 6 February 2010.
- ↑ "Five Reasons to Implement Kaizen in Non-Manufacturing". 6sigma.us. Retrieved March 31, 2015.
- ↑ Hamel, Mark (2010). Kaizen Event Fieldbook: Foundation, Framework, and Standard Work for Effective Events. Society Of Manufacturing Engineers. p. 36. ISBN 978-0-87263-863-1. Retrieved 20 April 2013.
- ↑ Karen Martin; Mike Osterling (October 5, 2007). The Kaizen Event Planner. Productivity Press. p. 240. ISBN 1563273519.
- ↑ Graupp P., Wrona B. (2015). The TWI Workbook: Essential Skills for Supervisors. New York: Productivity Press. ISBN 9781498703963.
- ↑ US National Archives - SCAP collection - PR News Wire
- ↑ "Taking the First Step with PDCA". 2 February 2009. Retrieved 17 March 2011.
- ↑ 5 Whys
- ↑ "Determine the Root Cause:5 Whys". Retrieved 24 October 2013.
- ↑ "An Introduction to 5-Why". 2 April 2009. Retrieved 1 February 2011.
- ↑ http://northdenvernews.com/what-are-realistic-ways-to-become-rich/
- ↑ Robbins, Anthony (1992). Awaken the Giant Within. New York: Simon & Schuster. pp. 544 pages. ISBN 0-671-79154-0.
- ↑ "Go Kaizen Yourself!". 31 October 2012. Retrieved 24 October 2013.
- ↑ Maurer, Robert (2004). One Small Step Can Change Your Life: The Kaizen Way. Workman. ISBN 978-0-7611-2923-3.
- ↑ Maurer, Robert. "One Small Step Can Change Your Life: The Kaizen Way".
- ↑ Liker, Jeffrey; Meier, David (2006). The Toyota Way Fieldbook. New York: McGraw-Hill.
Further reading
- Dinero, Donald (2005). Training Within Industry: The Foundation of. Productivity Press. ISBN 1-56327-307-1.
- Graban, Mark; Joe, Swartz (2012). Healthcare Kaizen: Engaging Front-Line Staff in Sustainable Continuous Improvements (1 ed.). Productivity Press. ISBN 1439872961.
- Maurer, Robert (2012). The Spirit of Kaizen: Creating Lasting Excellence One Small Step at a Time (1 ed.). McGraw-Hill. ISBN 978-0071796170.
- Emiliani, Bob; Stec, David; Grasso, Lawrence; Stodder, James (2007). Better Thinking, Better Results: Case Study and Analysis of an Enterprise-Wide Lean Transformation (2e. ed.). Kensington, CT, US: The CLBM, LLC. ISBN 978-0-9722591-2-5.
- Hanebuth, D. (2002). Rethinking Kaizen: An empirical approach to the employee perspective. In J. Felfe (Ed.), Organizational Development and Leadership (Vol. 11, pp. 59-85). Frankfurt a. M.: Peter Lang. ISBN 978-3-631-38624-8.
- Imai, Masaaki (1986). Kaizen: The Key to Japan's Competitive Success. McGraw-Hill/Irwin. ISBN 0-07-554332-X.
- Imai, Masaaki (1997-03-01). Gemba Kaizen: A Commonsense, Low-Cost Approach to Management (1e. ed.). McGraw-Hill. ISBN 0-07-031446-2.
- Scotchmer, Andrew (2008). 5S Kaizen in 90 Minutes. Management Books 2000 Ltd. ISBN 978-1-85252-547-7.
- Bodek, Norman (2010). How to do Kaizen: A new path to innovation - Empowering everyone to be a problem solver. Vancouver, WA, US: PCS Press. ISBN 978-0-9712436-7-5.
External links
![]() |
Look up kaizen in Wiktionary, the free dictionary. |
- Toyota stumbles but its "kaizen" cult endures, Reuters
- Warping Forward with Kaizen, Karn G. Bulsuk
- Kaizen, Joe Marshall
- Guide to Kaizen startup Best Practice Guide, Ben Geck
- Definition of Kaizen, Masaaki Imai
- Management by Stress, Jane Slaughter