5S (methodology)
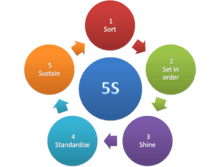
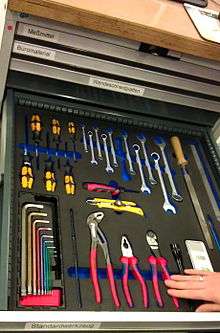
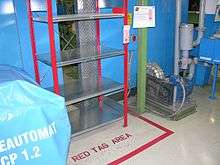
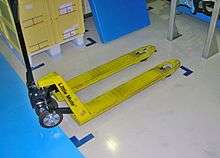
5S is the name of a workplace organization method that uses a list of five Japanese words: seiri, seiton, seiso, seiketsu, and shitsuke. Transliterated into Roman script, they all start with the letter "S".[1] The list describes how to organize a work space for efficiency and effectiveness by identifying and storing the items used, maintaining the area and items, and sustaining the new order.[2] The decision-making process usually comes from a dialogue about standardization, which builds understanding among employees of how they should do the work.
In some quarters, 5S has become 6S, the sixth element being safety.[3]
Other than a specific stand-alone methodology, 5S is frequently viewed as an element of a broader construct known as visual control,[4] visual workplace,[5] or visual factory.[6][7] Under those (and similar) terminologies, Western companies were applying underlying concepts of 5S before publication, in English, of the formal 5S methodology. For example, a workplace-organization photo from Tennant Company (a Minneapolis-based manufacturer) quite similar to the one accompanying this article appeared in a manufacturing-management book in 1986.[8]
The 5 S
There are five 5S phases: They can be translated from the Japanese as "sort", "set in order", "shine", "standardize", and "sustain". Other translations are possible.
Sort (Seiri)
- Make work easier by eliminating obstacles.
- Reduce chances of being disturbed with unnecessary items.
- Prevent accumulation of unnecessary items.
- Evaluate necessary items with regard to cost or other factors.
- Remove all parts or tools that are not in use.
- Segregate unwanted material from the workplace.
- Define Red-Tag area to place unnecessary items that cannot immediately be disposed of. Dispose of these items when possible.
- Need fully skilled supervisor for checking on a regular basis.
- Waste removal.
Set In Order (Seiton)
- Arrange all necessary items so that they can be easily selected for use.
- Prevent loss and waste of time by arranging work station in such a way that all tooling / equipment is in close proximity.
- Make it easy to find and pick up necessary items.
- Ensure first-in-first-out FIFO basis.
- Make workflow smooth and easy.
- All of the above work should be done on a regular basis.
- Maintain safety.
- Place components according to their uses, with the frequently used components bring nearest to the work place.
Shine (Seiso)
- Clean your workplace on daily basis completely or set cleaning frequency
- Use cleaning as inspection.
- Prevent machinery and equipment deterioration.
- Keep workplace safe and easy to work.
- Keep workplace clean and pleasing to work in.
- When in place, anyone not familiar to the environment must be able to detect any problems within 50 feet in 5 secs.
Standardize (Seiketsu)
- Standardize the best practices in the work area.
- Maintain high standards in workplace organization at all times.
- Maintain orderliness. Maintain everything in order and according to its standard.
- Everything in its right place.
- Every process has a standard.
Sustain (Shitsuke)
- Not harmful to anyone.
- Also translates as "do without being told".
- Perform regular audits.
- Training and discipline.
- Training is goal-oriented process. Its resulting feedback is necessary monthly.
- Self discipline
The Origins of 5S

5S was developed in Japan and was identified as one of the techniques that enabled Just in Time manufacturing.[9]
Two major frameworks for understanding and applying 5S to business environments have arisen, one proposed by Osada, the other by Hirano.[10][11] Hirano provided a structure to improve programs with a series of identifiable steps, each building on its predecessor. As noted by John Bicheno,[12] Toyota's adoption of the Hirano approach was '4S', with Seiton and Seiso combined.
In case of development of the Japanese system of management were used Alexey Gastev's development and the Central Institute of Labour (CIT) in Moscow.[13]
Variety of 5S Applications
5S methodology has expanded from manufacturing and is now being applied to a wide variety of industries including health care, education, and government. Visual management and 5S can be particularly beneficial in health care because a frantic search for supplies to treat an in-trouble patient (a chronic problem in health care) can have dire consequences.[14] Although the origins of the 5S methodology are in manufacturing, it can also be applied to knowledge-economy work, with information, software, or media in the place of physical product.[15]
5S in Lean Product & Process Development
The output of engineering and design in a lean enterprise is information, the theory behind using 5S here is "Dirty, cluttered, or damaged surfaces attract the eye, which spends a fraction of a second trying to pull useful information from them every time we glance past. Old equipment hides the new equipment from the eye and forces people to ask which to use"[16]
See also
References
- ↑ "What Is 5S? - Sort, Set In Order, Shine, Standardize, Sustain".
- ↑ "5S Comprehensive Education and Resource Center".
- ↑ Gapp, R., Fisher, R., Kobayashi, K. 2008. Implementing 5S within a Japanese Context: An Integrated Management System, Management Decision. 46(4): 565-579.
- ↑ Ortiz, Chris A. and Park, Murry. 2010. Visual Controls: Applying Visual Management to the Factory. New York: Productivity Press.
- ↑ Galsworth, Gwendolyn D. 2005. Visual Workplace: Visual Thinking. Portland, Ore: Visual-Lean Enterprise Press.
- ↑ Greif, Michel. 1989. The Visual Factory: Building Participation through Shared Information. Cambridge, Mass.: Productivity Press.
- ↑ Hirano, Hiroyuki, ed. 1988. JIT Factory Revolution: A Pictorial Guide to Factory Design of the Future. Cambridge, Mass.: Productivity Press.
- ↑ Schonberger, Richard J. 1986. World Class Manufacturing: The Lessons of Simplicity Applied. New York: Free Press, p. 27.
- ↑ Hirano, Hiroyuki. 1988. JIT Factory Revolution: A Pictorial Guide to Factory Design of the Future.
- ↑ Hirano, Hiroyuki (1995). 5 Pillars of the Visual Workplace. Cambridge, MA: Productivity Press. ISBN 978-1-56327-047-5.
- ↑ Osada, Takashi (1995). The 5S’s: Five keys to a Total Quality Environment. US: Asian Productivity Organization. ISBN 9283311167.
- ↑ Bicheno, John. New Lean Toolbox: Towards Fast, Flexible Flow. Buckingham: PICSIE. ISBN 978-0-9541244-1-0.
- ↑ Managing «modernity»: work, community, and authority in late-industrializing Japan and Russia, Rudra Sil, Publisher: Ann Arbor, Mich. : University of Michigan Press, 2002.
- ↑ Graban, Mark. 2012. Lean Hospitals: Improving Quality, Patient Safety, and Employee Engagement. Boca Raton, Fl: CRC Press.
- ↑ "CEITON – Profile".
- ↑ Ward, Allen (March 2014). Lean Product and Process Development (2nd ed.). Cambridge, MA: Lean Enterprise Institute. p. 215. ISBN 978-1-934109-43-4.