Smokebox

.jpg)
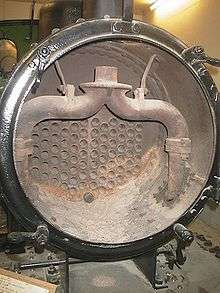
A smokebox is one of the major basic parts of a steam locomotive exhaust system. Smoke and hot gases pass from the firebox through tubes where they pass heat to the surrounding water in the boiler. The smoke then enters the smokebox, and is exhausted to the atmosphere through the chimney (or funnel). Early locomotives had no smokebox and relied on a long chimney to provide natural draught for the fire but smokeboxes were soon included in the design for two main reasons. Firstly and most importantly, the blast of exhaust steam from the cylinders, when directed upwards through an airtight smokebox with an appropriate design of exhaust nozzle, effectively draws hot gases through the boiler tubes and flues and, consequently, fresh combustion air into the firebox. Secondly, the smokebox provides a convenient collection point for ash and cinders ("char") drawn through the boiler tubes, which can be easily cleaned out at the end of a working day. Without a smokebox, all char must pass up the chimney or will collect in the tubes and flues themselves, gradually blocking them.
Blower
To assist the passage of the smoke and hot gases, a blower is often used. This is a pipe ending in a ring containing pin-sized holes, which creates a "ring" of steam jets. The steam forces out the smoke and draws further gases through the tubes. This in turn causes air to be drawn through the grate and firehole, making the fire burn hotter.
Blastpipe
When the locomotive is in motion, exhaust steam passes through the blastpipe, which is located within the smokebox. The steam is ejected through the chimney, again drawing the fire. The blastpipe is what produces the characteristic "chuff" sound.
Smokebox door
Ashes and soot which may be present in the smoke are often deposited in the smokebox. The front of the smokebox has a door which is opened to remove these deposits at the end of each locomotive's working day. The handle(s) must be tightened fully to prevent air leaks, which would reduce the draw on the fire and can also allow any unburnt char at the bottom of the smokebox to catch fire there. Some smokebox doors have a single handle in the form of a wheel; many British-built locomotives have a pair of smokebox door handles resembling the hands of a clock; other designs also exist. On many steamrollers an extension to the body of the smokebox also houses the bearing which supports the front roller. Due to limitations of space, these rollers usually have a drop-down flap instead of a circular smokebox door.
Steam pipes
The smokebox incorporates the main steam pipes from the regulator (or superheater header), one leading to each valve chest, a part of the cylinder casting. These may pass through the smokebox wall to join with the cylinder (outside steam pipes) or may stay within the profile of the smokebox (inside steam pipes). Inside steam pipes do not require lagging as the smokebox keeps them warm, but outside steam pipes are more common for locomotives with cylinders outside the frames. Some locomotive classes used both types depending on the date the batch was constructed (e.g. LNER Class V2).
Lagging
Because heat losses from the smokebox are of little consequence, it is not usually lagged. In most cases it appears to be the same diameter as the boiler in the finished locomotive but this only because of the boiler cladding; the boiler is narrower. Tank engines usually had their water tanks stop short of the unlagged smokebox as it could raise the temperature of the water sufficiently to cause problems with the injectors.
Self-cleaning smokebox
British Railways standard classes use this design, where a robust mesh grille is incorporated into the smokebox, forming a filter between the front tubeplate and the exhaust. Any large pieces of char passing through the boiler tubes tend to be broken up on impact with the mesh, creating finer particles which are swept up the chimney instead of accumulating in the bottom of the smokebox. This does not negate the need to clean out the smokebox but reduces the amount of work that has to be done. In the best case, smokebox cleaning could be avoided between boiler washouts, typically at intervals of two weeks.
Locomotive layout
The classic layout of a steam locomotive has the smokebox and chimney at the front of the locomotive, referred to as travelling "smokebox-first". Some designs reversed the layout to avoid problems (asphyxiation and poor visibility) caused by having the exhaust blowing back onto the crew; these were called cab forward locomotives.
Spark arrester
A spark arrester is often installed within the smokebox. This may take the form of a cylindrical mesh running from the top of the blast pipe to the bottom of the chimney. The purpose of a spark arrester is to prevent excessively large fragments of hot ash from being exhausted into the environment where they may pose a fire risk. For this reason, spark arresters are generally installed on locomotives running through dry environments. They should not be confused with the external spark arrestors fitted to some locomotives. The presence of a spark arrester may have a thermodynamic effect, distorting the draw of air over the fire and thereby reducing total power output. Thus their use can be contentious.
Superheating

Locomotives fitted with a superheater will usually have a superheater header in the smokebox. Steam enters the header as "wet" (saturated) steam, and then passes through a superheater element. This takes the form of a pipe which runs twice through an enlarged smoke tube in the boiler. The steam enters a separate chamber in the header, this time as superheated or dry steam. The advantage of superheating is that the steam has greater expansive properties when entering the cylinders, so more power can be gained from a smaller amount of water and fuel.
References
![]() |
Wikimedia Commons has media related to Smokeboxes. |