UV degradation
Many natural and synthetic polymers are attacked by ultraviolet radiation, and products using these materials may crack or disintegrate if they are not UV-stable. The problem is known as UV degradation, and is a common problem in products exposed to sunlight. Continuous exposure is a more serious problem than intermittent exposure, since attack is dependent on the extent and degree of exposure.
Many pigments and dyes can also be affected, and the problem known as phototendering can affect textiles such as curtains or drapes.
Susceptible polymers
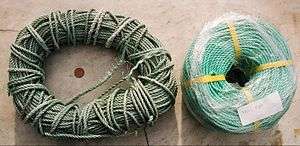
Common synthetic polymers that can be attacked include polypropylene and LDPE, where tertiary carbon bonds in their chain structures are the centres of attack. Ultraviolet rays interact with these bonds to form free radicals, which then react further with oxygen in the atmosphere, producing carbonyl groups in the main chain. The exposed surfaces of products may then discolour and crack, and in extreme cases, complete product disintegration can occur.
In fibre products like rope used in outdoor applications, product life will be low because the outer fibres will be attacked first, and will easily be damaged by abrasion for example. Discolouration of the rope may also occur, thus giving an early warning of the problem.
Polymers which possess UV-absorbing groups such as aromatic rings may also be sensitive to UV degradation. Aramid fibres like Kevlar, for example, are highly UV-sensitive and must be protected from the deleterious effects of sunlight.
Detection
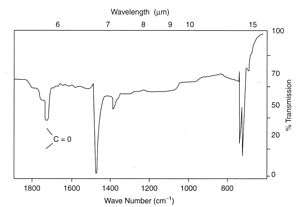
The problem can be detected before serious cracks are seen in a product using infrared spectroscopy, where attack occurs by oxidation of bonds activated by the UV radiation forming carbonyl groups in the polymer chains.
In the example shown at left, carbonyl groups were easily detected by IR spectroscopy from a cast thin film. The product was a road cone made by rotational moulding in LDPE, which had cracked prematurely in service. Many similar cones also failed because an anti-UV additive had not been used during processing. Other plastic products which failed included polypropylene mancabs used at roadworks which cracked after service of only a few months.
Prevention
UV attack by sunlight can be ameliorated or prevented by adding anti-UV chemicals to the polymer when mixing the ingredients, prior to shaping the product by injection moulding for example. UV stabilizers in plastics usually act by absorbing the UV radiation preferentially, and dissipating the energy as low-level heat. The chemicals used are similar to those in sunscreen products, which protect skin from UV attack. Frequently, glass can be a better alternative to polymers when it comes to UV degradation. Most of the commonly used glass types are highly resistant to UV radiation. Explosion protection lamps for oil rigs for example can be made either from polymer or glass. Here, the UV radiation and rough weathers belabor the polymer so much, that the material has to be replaced frequently.
Materials testing
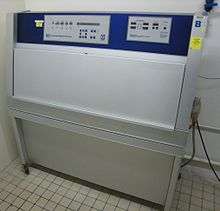
The effects of UV degradation on materials that require a long service life can be measured with accelerated exposure tests. With modern solar concentrator technologies, it is possible to simulate 63 years of natural UV radiation exposure on a test device in a single year.[1]
See also
- Photodegradation
- Forensic polymer engineering
- Polymer degradation
- Depolymerization
- Stress corrosion cracking
References
Further reading
- Lewis, Peter Rhys, Reynolds, K and Gagg, C, Forensic Materials Engineering: Case studies, CRC Press (2004)
External links
http://www.micomlab.com/uv-testing-guide/