ZBLAN
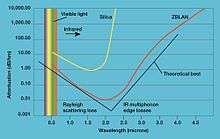

Heavy metal fluoride glasses were accidentally discovered in 1975 by Poulain and Lucas at the University of Rennes in France,[1] including a family of glasses ZBLAN with a composition ZrF4-BaF2-LaF3-AlF3-NaF.
Description
ZBLAN has a broad optical transmission window extending from 0.3 micrometers in the UV to 7 micrometers in the infrared, low refractive index (1.50), a relatively low glass transition temperature (Tg) of 260 °C, low dispersion and a low and negative dn/dT (temperature dependence of refractive index).[2]
ZBLAN glass is the most stable fluoride glass known and is most commonly used to make optical fiber. Recent advances by ZBLAN fiber manufacturers have demonstrated significant increases in mechanical properties (>100 kpsi or 700 MPa for 125 µm fiber) and attenuation as low as 3 dB/km at 2.6 µm. ZBLAN optical fibers are used in different applications such as spectroscopy and sensing, laser power delivery and fiber lasers and amplifiers.
Comparison with alternative fiber technologies
The advantages of ZBLAN over other glasses available in 1988, such as silica, is superior infrared transmittance. Their drawbacks are fragility and sensitivity to acids. ZBLAN glass resistance to water depends strongly on the acidity of the aqueous solution. Acidic solutions will attack it, whereas basic solutions will have no effect.[3] Atmospheric moisture has a very limited effect on fluoride glasses in general, and fluoride glass/fibers can be used in a wide range of operating environments over extended periods of time without any material degradation.[4]
A large variety of multicomponent fluoride glasses have been fabricated but few can be drawn into optical fiber. The fiber fabrication is similar to any glass-fiber drawing technology. All methods involve fabrication from the melt, which creates inherent problems such as the formation of bubbles, core-clad interface irregularities, and small preform sizes. The process occurs at 310 °C in a controlled atmosphere (to minimize contamination by moisture or oxygen impurities which significantly weaken the fiber) using a narrow heat zone compared to silica.[2] Drawing is complicated by a small difference (only 124 °C) between the glass transition temperature and the crystallization temperature. As a result, ZBLAN fibers often contain undesired crystallites. The concentration of crystallites was shown in 1998 to be reduced by growing ZBLAN in zero gravity (see figure) which reduces convection processes.[5]
In July 2016, a Silicon Valley aerospace company, Made In Space, announced that they plan to begin manufacturing ZBLAN in space for commercial purposes starting in 2017. [6]
References
- ↑ Poulain, M; Poulain, M; Lucas, J (1975). "Verres fluores au tetrafluorure de zirconium proprietes optiques d'un verre dope au Nd3+". Materials Research Bulletin. 10 (4): 243. doi:10.1016/0025-5408(75)90106-3.
- 1 2 Harrington, James A. "Infrared Fiber Optics" (PDF). Rutgers University.
- ↑ Guery, J., Chen, D. G., Simmons, C. J., Simmons, J. H., and Jcoboni, C. (1988). "Corrosion of uranium IV fluoride glasses in aqueous solutions". Phys. Chem. Glasses. 29: 30–36.
- ↑ K. Fujiura, K. Hoshino, T. Kanamori, Y. Nishida, Y. Ohishi, S. Sudo, Technical Digest of Optical Amplifiers and Their Applications, Davos, Switzerland. 15–17 June 1995 (Optical Society of America, Washington DC, USA, 1995)
- ↑ "ZBLAN continues to show promise". NASA. February 5, 1998. Retrieved 2009-06-06.
- ↑ "Made In Space plans to create a superior optical fiber in microgravity". Techcrunch. July 13, 2016. Retrieved 2016-07-13.