Machine press
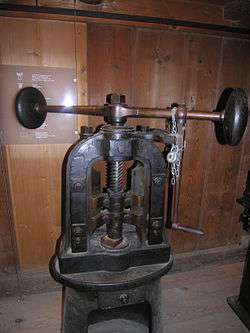

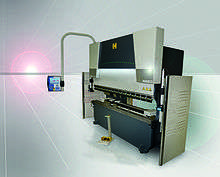

A forming press, commonly shortened to press, is a machine tool that changes the shape of a workpiece by the application of pressure.[1] Presses can be classified according to
- their mechanism: hydraulic, mechanical, pneumatic;
- their function: forging presses, stamping presses, press brakes, punch press, etc.
- their structure, e.g. Knuckle-joint press, screw press
- their controllability: conventional vs. servo-presses
An example of peculiar press structure: shop press
A simple frame, fabricated from steel, containing a bottle jack or simple hydraulic cylinder. Good for general-purpose work in the auto mechanic shop, machine shop, garage or basement shops, etc. Typically 1 to 30 tons of pressure, depending on size and expense. Classed with engine hoists and engine stands in many tool catalogs.
Some examples of presses by application
- A press brake is a special type of machine press that bends sheet metal into shape. A good example of the type of work a press brake can do is the backplate of a computer case. Other examples include brackets, frame pieces and electronic enclosures. Some press brakes have CNC controls and can form parts with accuracy to a fraction of a millimetre. Bending forces can range up to 3,000 tons.[2][3][4]
- A punch press is used to form holes.
- A screw press is also known as a fly press.
- A stamping press is a machine press used to shape or cut metal by deforming it with a die. It generally consists of a press frame, a bolster plate, and a ram.[5]
- Capping presses form caps from rolls of aluminium foil at up to 660 per minute.
An example of peculiar press control: servo-press
A servomechanism press, also known as a servo press or a 'electro press, is a press driven by an AC servo motor. The torque produced is converted to a linear force via a ball screw. Pressure and position are controlled through a load cell and an encoder. The main advantage of a servo press is its low energy consumption; its only 10-20% of other press machines.
When stamping, it's really about maximizing energy as opposed to how the machine can deliver tonnage. Up until recently, the way to increase tonnage between the die and workpiece on a mechanical press was through bigger machines with bigger motors.[6]
Types of presses
The press style used is in direct correlation to the end product. Press types are straightside, BG (back geared), geared, gap, OBI (open back inclinable) and OBS (open back stationary). Hydraulic and mechanical presses are classified by the frame the moving elements are mounted on. The most common are the gap-frame, also known as C-frame, and the straightside press. A straightside press has vertical columns on either side of the machine and eliminates angular deflection. A C-frame allows easy access to the die area on three sides and require less floor space. A type of gap-frame, the OBI pivots the frame for easier scrap or part discharge. The OBS timed air blasts, devices or conveyor for scrap or part discharge.[7][8]
Type of press | Type of frame | Position of frame | Action | Method of actuation | Type of drive | Suspension | Ram | Bed | ||||||||||||||||||||||||||
Open-back | Gap | Straight-side | Arch | Piller | Solid | Tie rod | Vertical | Horizontal | Inclinable | Inclined | Single | Double | Triple | Crank | Front-to-back crank | Eccentric | Toggle | Screw | Cam | Rack & pinion | Piston | Over direct | Geared, overdrive | Under direct | Geared, underdrive | One-point | Two-point | Four-point | Single | Multiple | Solid | Open | Adjustable | |
Bench | X | X | X | X | X | X | X | X | X | X | X | X | X | X | X | X | X | |||||||||||||||||
---|---|---|---|---|---|---|---|---|---|---|---|---|---|---|---|---|---|---|---|---|---|---|---|---|---|---|---|---|---|---|---|---|---|---|
Open-back inclinable | X | X | X | X | X | X | X | X | X | X | X | X | X | X | X | X | X | X | ||||||||||||||||
Gap-frame | X | X | X | X | X | X | X | X | X | X | X | X | X | X | X | X | X | X | X | X | X | X | X | X | ||||||||||
Adjustable-bed horn | X | X | X | X | X | X | X | X | X | X | X | X | X | X | X | |||||||||||||||||||
End-wheel | X | X | X | X | X | X | X | X | X | X | X | X | ||||||||||||||||||||||
Arch-frame | X | X | X | X | X | X | X | X | X | X | X | X | ||||||||||||||||||||||
Straight-side | X | X | X | X | X | X | X | X | X | X | X | X | X | X | X | X | X | X | X | X | X | X | X | X | X | X | ||||||||
Reducing | X | X | X | X | X | X | X | X | X | X | X | X | X | X | X | |||||||||||||||||||
Knuckle-lever | X | X | X | X | X | X | X | X | X | X | X | X | X | X | X | X | ||||||||||||||||||
Toggle-draw | X | X | X | X | X | X | X | X | X | X | X | X | X | X | X | X | ||||||||||||||||||
Cam-drawing | X | X | X | X | X | X | X | X | X | X | X | X | X | X | X | |||||||||||||||||||
Two-point single-action | X | X | X | X | X | X | X | X | X | X | X | X | X | X | X | |||||||||||||||||||
High-production | X | X | X | X | X | X | X | X | X | X | X | X | X | X | ||||||||||||||||||||
Dieing machine | X | X | X | X | X | X | X | X | X | X | ||||||||||||||||||||||||
Transfer | X | X | X | X | X | X | X | X | X | X | X | X | X | X | X | |||||||||||||||||||
Flat-edge trimming | X | X | X | X | X | X | X | X | ||||||||||||||||||||||||||
Hydraulic | X | X | X | X | X | X | X | X | X | X | X | X | X | X | X | X | X | X | ||||||||||||||||
Press brake | X | X | X | X | X | X | X | X | X | X | X | X |
History
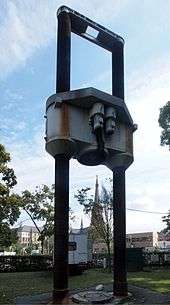
Historically, metal was shaped by hand using a hammer. Later, larger hammers were constructed to press more metal at once, or to press thicker materials. Often a smith would employ a helper or apprentice to swing the sledgehammer while the smith concentrated on positioning the workpiece. Adding windmill or steam power yielded still larger hammers such as steam hammers. Drop hammers utilize an electric motor to lift the hammer, which then falls by gravity onto the work. Most modern machine presses use a combination of electric motors and hydraulics to achieve the necessary pressure. Along with the evolution of presses came the evolution of the dies used within them.[9]
Hammers were the tool of choice for any Blacksmith, until the turning point in 1784 when a man called James Watt (a Scottish inventor and Mechanical Engineer) described the Steam Hammer. James Watt had a keen interest in steam engines and the mechanics behind it, and his invention of the steam condenser helped other engineers evolve this principle into other industries.
Eventually the steam hammer was built in 1840 based on a design by British Inventor James Nasmyth, which was revolutionary and a turning point for manufacturing with steel.
As the steam hammer was used, people made improvements and in 1891 the Bethlehem Iron Company made an enhancement that meant the steam hammer could deliver a 125-ton blow.[10]
Safety
Machine presses can be hazardous, so safety measures must always be taken. Bi-manual controls (controls the use of which requires both hands to be on the buttons to operate) are a very good way to prevent accidents, as are light sensors that keep the machine from working if the operator is in range of the die.
References
- ↑ Press, retrieved 2009-11-24.
- ↑ Press Brake Tonnage Table, American Machine Tools Co. Web site (http://www.americanmachinetools.com/pressure_table.htm). Retrieved 7-26-14.
- ↑ Press Brakes, Pacific Press Technologies Web site (http://www.pacific-press.com/brakes.html). Retrieved 7-26-14.
- ↑ Parker, Dana T. Building Victory: Aircraft Manufacturing in the Los Angeles Area in World War II, pp. 29, 83, Cypress, California, 2013. ISBN 978-0-9897906-0-4.
- ↑ Parker, Dana T. Building Victory: Aircraft Manufacturing in the Los Angeles Area in World War II, pp. 87, Cypress, California, 2013. ISBN 978-0-9897906-0-4.
- ↑ http://www.thefabricator.com/author/tim-heston (2008-01-15). "The science behind the servo press". www.thefabricator.com. Retrieved 2016-02-03.
- ↑ "Metal Stamping Equipment And Machines - American Industrial". American Industrial. Retrieved 2016-02-03.
- ↑ "SME.org PDF". www.sme.org. Retrieved 3 February 2016.
- ↑ Parker, Dana T. Building Victory: Aircraft Manufacturing in the Los Angeles Area in World War II, pp. 20, 29, 48, 83, 85, 87, Cypress, California, 2013. ISBN 978-0-9897906-0-4.
- ↑ Punch Press Services Ltd http://www.punchpressuk.com/page/10091/article/668
External links
![]() |
Wikimedia Commons has media related to Presses. |