Membrane gas separation
Gas mixtures can be effectively separated by synthetic membranes made from polymers such as polyamide or cellulose acetate, or from ceramic materials.[1]

Membranes can be used for separating gas mixtures where they act as a permeable barrier through which different compounds move across at different rates or not move at all. The membranes can be nanoporous, polymer, etc. and the gas molecules penetrate according to their size, diffusivity, or solubility.
Membrane Governing Methodology
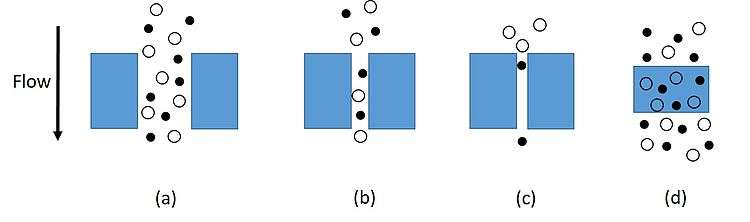
There are 3 main diffusion mechanisms. Molecular sieving is referred to the case where pores of the membrane are too small to let one component pass, which is not so practical in gas applications because the molecules are too small. Knudsen diffusion holds at very low pressures where lighter molecules move across faster in the stable larger pores.[2] In these cases the movement of molecules is best described by pressure-driven convective flow through capillaries, which is quantified by Darcy’s Law. However, the more general model in gas applications is the solution-diffusion where particles are first dissolved onto the membrane and then diffuse through it both at different rates. This model is employed when the pores in the polymer membrane appear and disappear faster relative to the movement of the particles.[3]
In a typical membrane system the incoming feed stream is separated into two components: permeant and retentate. Permeant is the gas that travels across the membrane and the retentate is what is left of the feed. On both sides of the membrane, a gradient of chemical potential is maintained by a pressure difference which is the driving force for the gas molecules to pass through. The ease of transport of each species is quantified by the permeability, Pi. With the assumptions of ideal mixing on both sides of the membrane, ideal gas law, constant diffusion coefficient and Henry’s Law, the flux of a species can be related to the pressure difference by Fick’s Law:[2]
where, (Ji) is the molar flux of species i across the membrane, (l) is membrane thickness, (Pi) is permeability of species i, (Di) is diffusivity, (Ki) is the Henry coefficient, and (pi') and (pi") represent the partial pressures of the species i at the feed and permeant side respectively. The product of DiKi is often expressed as the permeability of the species i, on the specific membrane being used.
The flow of a second species, j, can be defined as:
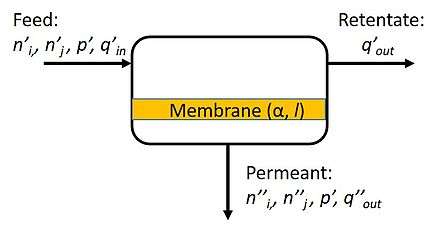
With the expression above, a membrane system for a binary mixture can be sufficiently defined. it can be seen that the total flow across the membrane is strongly dependent on the relation between the feed and permeate pressures. The ratio of feed pressure (p') over permeate pressure (p") is defined as the membrane pressure ratio (θ).
It is clear from the above, that a flow of species i or j across the membrane can only occur when:
In other words, the membrane will experience flow across it when there exists a concentration gradient between feed and permeate. If the gradient is positive, the flow will go from the feed to the permeate and species i will be separated from the feed.
Therefore, the maximum separation of species i results from:
Another important coefficient when choosing the optimum membrane for a separation process is the membrane selectivity αij defined as the ratio of permeability of species i with relation to the species j.
This coefficient is used to indicate the level to which the membrane is able to separates species i from j. It is obvious from the expression above, that a membrane selectivity of 1 indicates the membrane has no potential to separate the two gases, the reason being, both gases will diffuse equally through the membrane.
In the design of a separation process, normally the pressure ratio and the membrane selectivity are prescribed by the pressures of the system and the permeability of the membrane . The level of separation achieved by the membrane (concentration of the species to be separated) needs to be evaluated based on the aforementioned design parameters in order to evaluate the cost effectiveness of the system.
Membrane Performance
The concentration of species i and j across the membrane can be evaluated based on their respective diffusion flows across it.
In the case of a binary mixture, the concentration of species i across the membrane:
This can be further expanded to obtain an expression of the form:
Using the relations:
The expression can be rewritten as:
Then using
The solution to the above quadratic expression can be expressed as:
Finally, an expression for the permeant concentration is obtained by the following:
Along the separation unit, the feed concentration decays with the diffusion across the membrane causing the concentration at the membrane to drop accordingly. As a result, the total permeant flow (q"out) results from the integration of the diffusion flow across the membrane from the feed inlet (q'in) to feed outlet (q'out). A mass balance across a differential length of the separation unit is therefore:
where:
Because of the binary nature of the mixture, only one species needs to be evaluated. Prescribing a function n'i=n'i(x), the species balance can be rewritten as:
Where:
Lastly, the area required per unit membrane length can be obtained by the following expression:
Membrane Materials for Carbon Capture in Flue Gas Streams
The material of the membrane plays an important role in its ability to provide the desired performance characteristics. It is optimal to have a membrane with a high permeability and sufficient selectivity and it is also important to match the membrane properties to that of the system operating conditions (for example pressures and gas composition).
Synthetic membranes are made from a variety of polymers including polyethylene, polyamides, polyimides, cellulose acetate, polysulphone and polydimethylsiloxan.[5]
Polymer Membranes
Polymeric membranes are a common option for use in the capture of CO2 from flue gas because of the maturity of the technology in a variety of industries, namely petrochemicals. The ideal polymer membrane has both a high selectivity and permeability. Polymer membranes are examples of systems that are dominated by the solution-diffusion mechanism. The membrane is considered to have holes which the gas can dissolve (solubility) and the molecules can move from one cavity to the other (diffusion).[2]
It was discovered by Robeson in the early 1990s that polymers with a high selectivity have a low permeability and opposite is true; materials with a low selectivity have a high permeability. This is best illustrated in a Robeson plot where the selectivity is plotted as a function of the CO2 permeation. In this plot, the upper bound of selectivity is approximately a linear function of the permeability. It was found that the solubility in polymers is mostly constant but the diffusion coefficients vary significantly and this is where the engineering of the material occurs. Somewhat intuitively, the materials with the highest diffusion coefficients have a more open pore structure, thus losing selectivity.[6][7] There are two methods that researchers are using to break the Robeson limit, one of these is the use of glassy polymers whose phase transition and changes in mechanical properties make it appear that the material is absorbing molecules and thus surpasses the upper limit. The second method of pushing the boundaries of the Robeson limit is by the facilitated transport method. As previously stated, the solubility of polymers is typically fairly constant but the facilitated transport method uses a chemical reaction to enhance the permeability of one component without changing the selectivity.[2][8]
Nanoporous Membranes
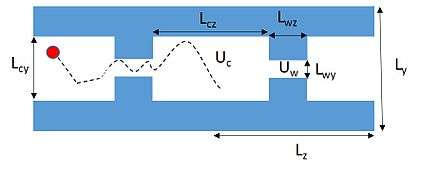
Nanoporous membranes are fundamentally different than polymer-based membranes in that their chemistry is different and that they do not follow the Robeson limit for a variety of reasons. The simplified figure of a nanoporous membrane shows a small portion of an example membrane structure with cavities and windows. The white portion represents the area where the molecule can move and the blue shaded areas represent the walls of the structure. In the engineering of these membranes, the size of the cavity (Lcy x Lcz) and window region (Lwy x Lwz) can be modified so that the desired permeation is achieved. It has been shown that the permeability of a membrane is the production of adsorption and diffusion. In low loading conditions, the adsorption can be computed by the Henry coefficient.[2]
If the assumption is made that the energy of a particle does not change when moving through this structure, only the entropy of the molecules changes based on the size of the openings. If we first consider changes the cavity geometry, the larger the cavity, the larger the entropy of the absorbed molecules which thus makes the Henry coefficient larger. For diffusion, an increase in entropy will lead to a decrease in free energy which in turn leads to a decrease in the diffusion coefficient. Conversely, changing the window geometry will primarily effect the diffusion of the molecules and not the Henry coefficient.
In summary, by using the above simplified analysis, it is possible to understand why the upper limit of the Robeson line does not hold for nanostructures. In the analysis, both the diffusion and Henry coefficients can be modified without effecting the permeability of the material which thus can exceed the upper limit for polymer membranes.:[2]
Other Membrane Technologies
In special cases other materials can be utilized; for example, palladium membranes permit transport solely of hydrogen.[9] In addition to palladium membranes (which are typically palladium silver alloys to stop embrittlement of the alloy at lower temperature) there is also a significant research effort looking into finding non-precious metal alternatives. Although slow kinetics of exchange on the surface of the membrane and tendency for the membranes to crack or disintegrate after a number of duty cycles or during cooling are problems yet to be fully solved.[10]
Construction
Membranes are typically contained in one of three modules:[5]
- Hollow fibre bundles in a metal module
- Spiral wound bundles in a metal module
- plate and frame module constructed like a plate and frame heat exchanger
Uses
Membranes are employed in:[1]
- The separation of nitrogen or oxygen from air. (Generally only up to 99.5%)
- Separation of hydrogen from gases like nitrogen and methane
- Recovery of hydrogen from product streams of ammonia plants
- Recovery of hydrogen in oil refinery processes
- Separation of methane from the other components of biogas
- Enrichment of air by oxygen for medical or metallurgical purposes
- Enrichment of ullage by nitrogen in Inerting systems designed to prevent fuel tank explosions
- Removal of water vapor from natural gas and other gasesFurther information: Membrane driers
- Removal of SO2, CO2 and H2S from natural gas (polyamide membranes)
- Removal of volatile organic liquids (VOL) from air of exhaust streams
Current Status of CO2 Capture with Membranes
A great deal of research has been undertaken to utilize membranes instead of absorption or adsorption for carbon capture from flue gas streams, however, no current project exist that utilizes membranes. Very clever process engineering along with new developments in materials have shown that membranes have the greatest potential for low energy penalty and cost compared to competing technologies.
References
- 1 2 Kerry, Frank (2007). Industrial Gas Handbook: Gas Separation and Purification. CRC Press. pp. 275–280. ISBN 9780849390050.
- 1 2 3 4 5 6 Berend Smit; Jeffrey A. Reimer; Curtis M. Oldenburg; Ian C. Bourg (2014). Introduction to Carbon Capture and Sequestration. Imperial College Press. pp. 281–354. ISBN 978-1-78326-328-8.
- ↑ Richard W. Baker (2004). Membrane Technology and Applications. John Wiley & Sons Ltd. pp. 15–21. ISBN 0-470-85445-6.
- ↑ Wilcox, Jennifer. Carbon Capture. Springer. ISBN 978-1-4939-0125-8.
- 1 2 Isalski, W. H. (1989). Separation of Gases. Monograph on Cryogenics. 5. New York: Oxford University Press. pp. 228–233.
- ↑ Robeson, L.M. (1991). "Correlation of separation factor versus permeability for polymeric membranes". Journal of Membrane Science. 62 (165).
- ↑ Robeson, L.M. (2008). "The upper bound revisited". Journal of Membrane Science. 320 (390).
- ↑ Merkel, Tim C., Lin, Haiqing., Baker, Richard (2010). "Power plant post-combustion carbon dioxide capture: An opportunity for membranes". Journal of Membrane Science. 359: 126–139.
- ↑ Yun, S.; Ted Oyama, S. (2011). "Correlations in palladium membranes for hydrogen separation: A review". Journal of Membrane Science. 375: 28. doi:10.1016/j.memsci.2011.03.057.
- ↑ Dolan, Michael D.; Kochanek, Mark A.; Munnings, Christopher N.; McLennan, Keith G.; Viano, David M. (February 2015). "Hydride phase equilibria in V–Ti–Ni alloy membranes". Journal of Alloys and Compounds. 622: 276–281. doi:10.1016/j.jallcom.2014.10.081.
- Vieth, W.R. (1991). Diffusion in and through Polymers. Munich: Hanser Verlag. ISBN 9783446155749.