Plasticizer
Plasticizers (UK: plasticisers) or dispersants are additives that increase the plasticity or viscosity of a material. Over the last 60 years more than 30,000 different substances have been evaluated for their plasticizing properties. Of these, only a small number – approximately 50 - are today in commercial use. The dominant applications are for plastics, especially polyvinyl chloride (PVC). The properties of other materials are also improved when blended with plasticizers including concrete, clays, and related products. According to 2014 data, the total global market for plasticizers was 8.4 million metric tonnes [1] including 1.3 million metric tonnes in Europe.
For plastics
Plasticizers for plastics are additives, most commonly phthalate esters in PVC applications. Almost 90% of plasticizers are used in PVC, giving this material improved flexibility and durability.[2] The majority is used in films and cables.[3] It was commonly thought that plasticizers work by embedding themselves between the chains of polymers, spacing them apart (increasing the "free volume"),[4][5] and thus significantly lowering the glass transition temperature for the plastic and making it softer; however it was later shown that the free volume explanation could not account for all of the effects of plasticization.[6] For plastics such as PVC, the more plasticizer added, the lower their cold flex temperature will be. Plastic items containing plasticizers exhibit improved flexibility and durability. Plasticizers can become available for exposure due to migration and abrasion of the plastic since they are not bound to the polymer matrix. The "new car smell" is often attributed to plasticizers or their degradation products.[7] However, multiple studies on the makeup of the smell do not find phthalates in appreciable amounts, likely due to their extremely low volatility and vapor pressure.[8]
Plasticizers make it possible to achieve improved compound processing characteristics, while also providing flexibility in the end-use product. Ester plasticizers are selected based upon cost-performance evaluation. The rubber compounder must evaluate ester plasticizers for compatibility, processibility, permanence and other performance properties. The wide variety of ester chemistries that are in production include sebacates, adipates, terephthalates, dibenzoates, gluterates, phthalates, azelates, and other specialty blends. This broad product line provides an array of performance benefits required for the many elastomer applications such as tubing and hose products, flooring, wall-coverings, seals and gaskets, belts, wire and cable, and print rolls. Low to high polarity esters provide utility in a wide range of elastomers including nitrile, polychloroprene, EPDM, chlorinated polyethylene, and epichlorohydrin. Plasticizer-elastomer interaction is governed by many factors such as solubility parameter, molecular weight, and chemical structure. Compatibility and performance attributes are key factors in developing a rubber formulation for a particular application.[9]
Plasticizers also function as softeners, extenders, and lubricants, and play a significant role in rubber manufacturing.
Antiplasticizers
Antiplasticizers (Anti Plasticizers) exhibit similar, but sometimes opposite, effects as plasticizers on polymer systems. The effect of plasticizers on modulus is dependent on both temperature and plasticizer concentration. Below a certain concentration, referred to as the crossover concentration, a plasticizer can increase the modulus of a material. The material's glass transition temperature will decrease however, at all concentrations. In addition to a crossover concentration a crossover temperature exists. Below the crossover temperature the plasticizer will also increase the modulus. Antiplasticizers can be defined as any small molecule or oligomer additive which increases the modulus while decreasing the glass transition temperature.
phthalate.png)
Ester plasticizers
Plasticizers used in PVC and other plastics are often based on esters of polycarboxylic acids with linear or branched aliphatic alcohols of moderate chain length. These compounds are selected on the basis of many critieria including low toxicity, compatibility with the host material, nonvolatility, and expense. Phthalate esters of straight-chain and branched-chain alkyl alcohols meet these specifications and are common plasticizers. Ortho-phthalate esters have traditionally been the most dominant plasticizers, but regulatory concerns have led to the move away from classified substances to non-classified which includes high molecular weight ortho-phthalates and other plasticisers, especially in Europe.
For concrete
Plasticizers or water reducers, and superplasticizer or high range water reducers, are chemical admixtures that can be added to concrete mixtures to improve workability. Unless the mix is "starved" of water, the strength of concrete is inversely proportional to the amount of water added or water-cement (w/c) ratio. In order to produce stronger concrete, less water is added (without "starving" the mix), which makes the concrete mixture less workable and difficult to mix, necessitating the use of plasticizers, water reducers, superplasticizers or dispersants. [10]
Plasticizers are also often used when pozzolanic ash is added to concrete to improve strength. This method of mix proportioning is especially popular when producing high-strength concrete and fiber-reinforced concrete.
Adding 1-2% plasticizer per unit weight of cement is usually sufficient. Adding an excessive amount of plasticizer will result in excessive segregation of concrete and is not advisable. Depending on the particular chemical used, use of too much plasticizer may result in a retarding effect.
Plasticizers are commonly manufactured from pop lignosulfonates, a by-product from the paper industry. Superplasticizers have generally been manufactured from sulfonated naphthalene condensate or sulfonated melamine formaldehyde, although newer products based on polycarboxylic ethers are now available. Traditional lignosulfonate-based plasticisers, naphthalene and melamine sulfonate-based superplasticisers disperse the flocculated cement particles through a mechanism of electrostatic repulsion (see colloid). In normal plasticisers, the active substances are adsorbed on to the cement particles, giving them a negative charge, which leads to repulsion between particles. Lignin, naphthalene and melamine sulfonate superplasticisers are organic polymers. The long molecules wrap themselves around the cement particles, giving them a highly negative charge so that they repel each other.
Polycarboxylate ether superplasticizer (PCE) or just polycarboxylate (PC), work differently from sulfonate-based superplasticizers, giving cement dispersion by steric stabilisation, instead of electrostatic repulsion. This form of dispersion is more powerful in its effect and gives improved workability retention to the cementitious mix.[11]
In ancient times, the Romans used animal fat, milk and blood to improve workability of concrete mixes.[12]
For gypsum wallboard production
Plasticizers can be added to wallboard stucco mixtures to improve workability. In order to reduce the energy in drying wallboard, less water is added, which makes the gypsum mixture very unworkable and difficult to mix, necessitating the use of plasticizers, water reducers or dispersants. Some studies also show that too much of lignosulfonate dispersant could result in a set-retarding effect. Data showed that amorphous crystal formations occurred that detracted from the mechanical needle-like crystal interaction in the core, preventing a stronger core. The sugars, chelating agents in lignosulfonates such as Aldonic acids and extractive compounds are mainly responsible for set retardation. These low range water reducing dispersants are commonly manufactured from lignosulfonates, a by-product from the paper industry.
High range superplasticizers (dispersants) have generally been manufactured from sulfonated naphthalene condensate, although polycarboxylic ethers represent more modern alternatives. Both of these high range water reducers are used at 1/2 to 1/3 of the lignosulfonate types.[13]
Traditional lignosulfonate and naphthalene sulfonate based plasticisers disperse the flocculated gypsum particles through a mechanism of electrostatic repulsion (see colloid). In normal plasticisers, the active substances are adsorbed on to the gypsum particles, giving them a negative charge, which leads to repulsion between particles. Lignin and naphthalene sulfonate plasticizers are organic polymers. The long molecules wrap themselves around the gypsum particles, giving them a highly negative charge so that they repel each other.[14]
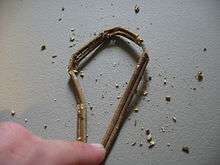
Plasticizers for energetic materials
Energetic material pyrotechnic compositions, especially solid rocket propellants and smokeless powders for guns, often employ plasticizers to improve physical properties of the propellant binder or of the overall propellant, to provide a secondary fuel, and ideally, to improve specific energy yield (e.g. specific impulse, energy yield per gram of propellant, or similar indices) of the propellant. An energetic plasticizer improves the physical properties of an energetic material while also increasing its specific energy yield. Energetic plasticizers are usually preferred to non-energetic plasticizers, especially for solid rocket propellants. Energetic plasticizers reduce the required mass of propellant, enabling a rocket vehicle to carry more payload or reach higher velocities than would otherwise be the case. However, safety or cost considerations may demand that non-energetic plasticizers be used, even in rocket propellants. The solid rocket propellant used to fuel the Space Shuttle solid rocket booster employs HTPB, a synthetic rubber, as a non-energetic plasticizer/binder/secondary fuel.
Effect on health
Substantial concerns have been expressed over the safety of some plasticizers, especially because some low molecular weight ortho-phthalates have been classified as potential endocrine disruptors with some developmental toxicity reported.[15]
Appendix: various specific plasticizers
Dicarboxylic/tricarboxylic ester-based plasticizers
- Phthalate-based plasticizers are used in situations where good resistance to water and oils is required. Some common phthalate plasticizers are:
- Bis(2-ethylhexyl) phthalate (DEHP), used in construction materials and medical devices
- Bis(2-propylheptyl) phthalate (DPHP), used in cables, wires and roofing materials
- Diisononyl phthalate (DINP), used in flooring materials, found in garden hoses, shoes, toys, and building materials
- Di-n-butyl phthalate (DnBP, DBP), used for cellulose plastics, food wraps, adhesives, perfumes, and cosmetics - about a third of nail polishes, glosses, enamels, and hardeners contain it, together with some shampoos, sunscreens, skin emollients, and insect repellents
- Butyl benzyl phthalate (BBzP) is found in vinyl tiles, traffic cones, food conveyor belts, artificial leather, and plastic foams
- Diisodecyl phthalate (DIDP), used for insulation of wires and cables, car undercoating, shoes, carpets, pool liners
- Dioctyl phthalate (DOP or DnOP), used in flooring materials, carpets, notebook covers, and high explosives, such as Semtex. Together with DEHP it was the most common plasticizers
- Diisooctyl phthalate (DIOP), all-purpose plasticizer for polyvinyl chloride, polyvinyl acetate, rubbers, cellulose plastics, and polyurethane.
- Diethyl phthalate (DEP)
- Diisobutyl phthalate (DIBP)
- Di-n-hexyl phthalate, used in flooring materials, tool handles, and automobile parts
Trimellitates
- Trimellitates are used in automobile interiors and other applications where resistance to high temperature is required. They have extremely low volatility.
- Trimethyl trimellitate (TMTM)
- Tri-(2-ethylhexyl) trimellitate (TEHTM-MG)
- Tri-(n-octyl,n-decyl) trimellitate (ATM)
- Tri-(heptyl,nonyl) trimellitate (LTM)
- n-octyl trimellitate (OTM)
Adipates, sebacates, maleates
- Adipate-based plasticizers are used for low-temperature or resistance to ultraviolet light. Some examples are:
- Bis(2-ethylhexyl)adipate (DEHA)
- Dimethyl adipate (DMAD)
- Monomethyl adipate (MMAD)
- Dioctyl adipate (DOA)
- Dibutyl sebacate (DBS)
- Dibutyl maleate (DBM)
- Diisobutyl maleate (DIBM)
Other plasticizers
- Azelates
- Benzoates
- Terephthalates such as Dioctyl terephthalate/DEHT (Eastman Chemical Company Trademark: Eastman 168).
- 1,2-Cyclohexane dicarboxylic acid diisononyl ester (BASF trademark: Hexamoll DINCH).
- Epoxidized vegetable oils
- alkyl sulphonic acid phenyl ester (ASE).
- Sulfonamides
- N-ethyl toluene sulfonamide (o/p ETSA), ortho and para isomers
- N-(2-hydroxypropyl) benzene sulfonamide (HP BSA)
- N-(n-butyl) benzene sulfonamide (BBSA-NBBS)
- Organophosphates
- Tricresyl phosphate (TCP)
- Tributyl phosphate (TBP)
- Glycols/polyethers
- Triethylene glycol dihexanoate (3G6, 3GH)
- Tetraethylene glycol diheptanoate (4G7)
- Polymeric plasticizers
- Polybutene
Bio-based plasticizers
Plasticizers with better biodegradability and fewer chemical effects are being developed. Some such plasticizers are:
- Acetylated monoglycerides; these can be used as food additives
- Alkyl citrates, used in food packagings, medical products, cosmetics and children toys
- Triethyl citrate (TEC)
- Acetyl triethyl citrate (ATEC), higher boiling point and lower volatility than TEC
- Tributyl citrate (TBC)
- Acetyl tributyl citrate (ATBC), compatible with PVC and vinyl chloride copolymers
- Trioctyl citrate (TOC), also used for gums and controlled release medicines
- Acetyl trioctyl citrate (ATOC), also used for printing ink
- Trihexyl citrate (THC), compatible with PVC, also used for controlled release medicines
- Acetyl trihexyl citrate (ATHC), compatible with PVC
- Butyryl trihexyl citrate (BTHC, trihexyl o-butyryl citrate), compatible with PVC
- Trimethyl citrate (TMC), compatible with PVC
- Green plasticizers
- Epoxidized soybean oil (ESBO)
Plasticizers for energetic materials
Here are some energetic plasticizers used in rocket propellants and smokeless powders:
- Nitroglycerine (NG, aka "nitro", glyceryl trinitrate)
- Butanetriol trinitrate (BTTN)
- Dinitrotoluene (DNT)
- Trimethylolethane trinitrate (TMETN, aka Metriol trinitrate, METN)
- Diethylene glycol dinitrate (DEGDN, less commonly DEGN)
- Triethylene glycol dinitrate (TEGDN, less commonly TEGN)
- Bis(2,2-dinitropropyl)formal (BDNPF)
- Bis(2,2-dinitropropyl)acetal (BDNPA)
- 2,2,2-Trinitroethyl 2-nitroxyethyl ether (TNEN)
Due to the secondary alcohol groups, NG and BTTN have relatively low thermal stability. TMETN, DEGDN, BDNPF and BDNPA have relatively low energies. NG and DEGN have relatively high vapor pressure.[16]
References
- ↑ Malveda, Michael P (July 2015). "Chemical Economics Handbook Report on Plasticizers".
- ↑ David F. Cadogan and Christopher J. Howick "Plasticizers" in Ullmann's Encyclopedia of Industrial Chemistry 2000, Wiley-VCH, Weinheim. doi: 10.1002/14356007.a20_439
- ↑ Market Study Plasticizers, 3rd ed., Ceresana, Nov. 2013
- ↑ (1) Maeda, Y.; Paul, D. R. J. Polym. Sci. Part B Polym. Phys. 1987, 25, 957–980.
- ↑ (1) Maeda, Y.; Paul, D. R. J. Polym. Sci. Part B Polym. Phys. 1987, 25, 1005–1016.
- ↑ (1) Casalini, R.; Ngai, K. L.; Robertson, C. G.; Roland, C. M. J. Polym. Sci. Part B Polym. Phys. 2000, 38, 1841–1847.
- ↑ Geiss, O.; Tirendi, S.; Barrero-Moreno, J.; Kotzias, D., "Investigation of volatile organic compounds and phthalates present in the cabin air of used private cars", Environment International 2009, 35, 1188-1195. doi:10.1016/j.envint.2009.07.016
- ↑ Chemical and Engineering News, 2002, 80(20), 45; http://pubs.acs.org/cen/whatstuff/stuff/8020stuff.html
- ↑ Archived March 27, 2009, at the Wayback Machine.
- ↑ Cement Admixture Association. "CAA". www.admixtures.org.uk. Retrieved 2008-04-02.
- ↑ C&En: Coverstory - Synthetic Chemistry Moves Into Concrete
- ↑ Cemex Mortars, p. 6 Archived December 7, 2012, at the Wayback Machine.
- ↑ Archived July 24, 2011, at the Wayback Machine.
- ↑ Kirby, Glen H.; Jennifer A. Lewis (2002). "Rheological property evolution in concentrated cement-polyelectrolyte suspensions". Journal of the American Ceramic Society. 85 (12): 2989–2994. doi:10.1111/j.1151-2916.2002.tb00568.x. Retrieved 2008-03-27.
- ↑ Plastics and Health Risks Annual Review of Public Health, Vol. 31: 179-194 (Volume publication date April 2010), First published on January 13, 2010 DOI: 10.1146/annurev.publhealth.012809.103714
- ↑ 2,2,2-trinitroethyl 2-nitroxyethyl ether and a method of preparation - The United States of America as represented by the Secretary of the Navy
External links
- Plasticisers Information Centre
- Glass transition
- DIDP,DINP,DBP,BBP,DEHP, DPHP,DIBP Risk Assessment Reports by the European Chemicals Bureau (ECB).