Polylactic acid
![]() | |
Identifiers | |
---|---|
26100-51-6 | |
ECHA InfoCard | 100.128.355 |
Properties | |
(C3H4O2)n | |
Density | 1.210–1.430 g·cm−3 [1] |
Melting point | 150–160 °C (302–320 °F; 423–433 K)[1] |
Insoluble in water[2] | |
Hazards | |
NFPA 704 | |
Except where otherwise noted, data are given for materials in their standard state (at 25 °C [77 °F], 100 kPa). | |
Infobox references | |
Poly(lactic acid) or polylactic acid or polylactide (PLA) is a biodegradable and bioactive thermoplastic aliphatic polyester derived from renewable resources, such as corn starch (in the United States and Canada), tapioca roots, chips or starch (mostly in Asia), or sugarcane (in the rest of the world). In 2010, PLA had the second highest consumption volume of any bioplastic of the world.[3]
The name "polylactic acid" does not comply with IUPAC standard nomenclature, and is potentially ambiguous or confusing, because PLA is not a polyacid (polyelectrolyte), but rather a polyester.[4]
Production
Producers have several industrial routes to usable (i.e. high molecular weight) PLA. Two main monomers are used: lactic acid, and the cyclic di-ester, lactide. The most common route to PLA is the ring-opening polymerization of lactide with various metal catalysts (typically tin octoate) in solution, in the melt, or as a suspension. The metal-catalyzed reaction tends to cause racemization of the PLA, reducing its stereoregularity compared to the starting material (usually corn starch).[5]
Another route to PLA is the direct condensation of lactic acid monomers. This process needs to be carried out at less than 200 °C; above that temperature, the entropically favored lactide monomer is generated. This reaction generates one equivalent of water for every condensation (esterification) step, and that is undesirable because water causes chain-transfer leading to low molecular weight material. The direct condensation is thus performed in a stepwise fashion, where lactic acid is first oligomerized to PLA oligomers. Thereafter, polycondensation is done in the melt or as a solution, where short oligomeric units are combined to give a high molecular weight polymer strand. Water removal by application of a vacuum or by azeotropic distillation is crucial to favor polycondensation over transesterification. Molecular weights of 130 kDa can be obtained this way. Even higher molecular weights can be attained by carefully crystallizing the crude polymer from the melt. Carboxylic acid and alcohol end groups are thus concentrated in the amorphous region of the solid polymer, and so they can react. Molecular weights of 128–152 kDa are obtainable thus.[5]
Polymerization of a racemic mixture of L- and D-lactides usually leads to the synthesis of poly-DL-lactide (PDLLA), which is amorphous. Use of stereospecific catalysts can lead to heterotactic PLA which has been found to show crystallinity. The degree of crystallinity, and hence many important properties, is largely controlled by the ratio of D to L enantiomers used, and to a lesser extent on the type of catalyst used. Apart from lactic acid and lactide, lactic acid O-carboxyanhydride ("lac-OCA"), a five-membered cyclic compound has been used academically as well. This compound is more reactive than lactide, because its polymerization is driven by the loss of one equivalent of carbon dioxide per equivalent of lactic acid. Water is not a co-product.[6]
The direct biosynthesis of PLA similar to the poly(hydroxyalkanoate)s has been reported as well.[7]
Manufacturers
As of June 2010, NatureWorks was the primary producer of PLA (bioplastic) in the United States. Other companies involved in PLA manufacturing are Evonik Industries (Germany), Corbion PURAC Biomaterials (The Netherlands) who have announced a new 75,000 ton PLA plant in Thailand by 2018, and several Chinese manufacturers. The primary producer of PDLLA is Evonik Industries and Corbion PURAC. Evonik Industries is a specialty chemical company that is industry leading in approximately 80% of the markets they participate. The Resomer brand of PDLLA is produced in the Health and Nutrition business segment. Corbion PURAC is a listed company in the Netherlands, and operating plants worldwide, and the only producer of PDLA, produced from the D-isomer of lactid acid. Galactic and Total Petrochemicals operate a joint venture, Futerro, which is developing a second generation polylactic acid product. This project includes the building of a PLA pilot plant in Belgium capable of producing 1,500 tonnes/year.
Chemical and physical properties
Due to the chiral nature of lactic acid, several distinct forms of polylactide exist: poly-L-lactide (PLLA) is the product resulting from polymerization of L,L-lactide (also known as L-lactide). PLLA has a crystallinity of around 37%, a glass transition temperature 60–65 °C, a melting temperature 173–178 °C and a tensile modulus 2.7–16 GPa.[8][9] Heat-resistant PLA can withstand temperatures of 110 °C.[10] PLA is soluble in chlorinated solvents, hot benzene, tetrahydrofuran, and dioxane.[11]
Polylactic acid can be processed like most thermoplastics into fiber (for example, using conventional melt spinning processes) and film. PLA has similar mechanical properties to PETE polymer, but has a significantly lower maximum continuous use temperature.[12] The tensile strength for 3-D printed PLA was previously determined.[13] It was found to range widely depending on printing conditions, which were obtained using RepRap 3-D printers.[14] Results of a recent study gave a printed tensile strength of around 50 MPa and show that the act of 3-D printing PLA affects its properties—they showed a strong relationship between tensile strength and percent crystallinity of a 3-D printed sample and a strong relationship between percent crystallinity and the extruder temperature.[15]
The melting temperature of PLLA can be increased by 40–50 °C and its heat deflection temperature can be increased from approximately 60 °C to up to 190 °C by physically blending the polymer with PDLA (poly-D-lactide). PDLA and PLLA form a highly regular stereocomplex with increased crystallinity. The temperature stability is maximised when a 1:1 blend is used, but even at lower concentrations of 3–10% of PDLA, there is still a substantial improvement. In the latter case, PDLA acts as a nucleating agent, thereby increasing the crystallization rate. Biodegradation of PDLA is slower than for PLA due to the higher crystallinity of PDLA.
There is also poly(L-lactide-co-D,L-lactide) (PLDLLA) – used as PLDLLA/TCP scaffolds for bone engineering.[16][17]
Applications
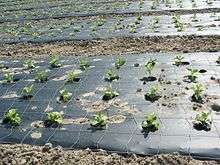

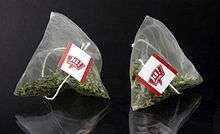

PLA can be processed by extrusion such as 3d printing, injection molding, film and sheet casting, and spinning, providing access to a wide range of materials.

PLA is used as a feedstock material in desktop fused filament fabrication-based 3D printers (e.g. RepRap).[19][20] PLA printed solids can be encased in plaster-like moulding materials, then burned out in a furnace, so that the resulting void can be filled with molten metal. This is known as "lost PLA casting", a type of investment casting.
Being able to degrade into innocuous lactic acid, PLA is used as medical implants in the form of anchors, screws, plates, pins, rods, and as a mesh.[21] Depending on the exact type used, it breaks down inside the body within 6 months to 2 years. This gradual degradation is desirable for a support structure, because it gradually transfers the load to the body (e.g. the bone) as that area heals. The strength characteristics of PLA and PLLA implants are well documented.[22]
PLA can also be used as a decomposable packaging material, either cast, injection-molded, or spun.[21] Cups and bags have been made from this material. In the form of a film, it shrinks upon heating, allowing it to be used in shrink tunnels. It is useful for producing loose-fill packaging, compost bags, food packaging, and disposable tableware. In the form of fibers and nonwoven fabrics, PLA also has many potential uses, for example as upholstery, disposable garments, awnings, feminine hygiene products, and diapers.
Racemic and regular PLLA has a low glass transition temperature, which is undesirable. A stereocomplex of PDLA and PLLA has a higher glass transition temperatures, lending it more mechanical strength. It has a wide range of applications, such as woven shirts (ironability), microwavable trays, hot-fill applications and even engineering plastics (in this case, the stereocomplex is blended with a rubber-like polymer such as ABS). Such blends also have good form stability and visual transparency, making them useful for low-end packaging applications. Pure poly-L-lactic acid (PLLA), on the other hand, is the main ingredient in Sculptra, a long-lasting facial volume enhancer, primarily used for lipoatrophy of cheeks. Progress in biotechnology has resulted in the development of commercial production of the D enantiomer form, something that was not possible until recently.[23]
Recycling

Currently, the SPI resin identification code 7 ("others") is applicable for PLA. In Belgium, Galactic started the first pilot unit to chemically recycle PLA (Loopla). Unlike mechanical recycling, waste material can hold various contaminants. Polylactic acid can be recycled to monomer by thermal depolymerization or hydrolysis. When purified, the monomer can be used for the manufacturing of virgin PLA with no loss of original properties (cradle-to-cradle recycling).
Degradation
Amycolatopsis and Saccharotrix are able to degrade PLA. A purified protease from Amycolatopsis sp., PLA depolymerase, can also degrade PLA. Enzymes such as pronase and most effectively proteinase K from Tritirachium album degrade PLA.[24]
Pure PLLA foams undergo selective hydrolysis when placed in an environment of Dulbecco’s modified Eagle's medium (DMEM) supplemented with fetal bovine serum (FBS) (a solution mimicking body fluid). After 30 days of submersion in DMEM+FBS, a PLLA scaffold lost about 20% of its weight.[25]
See also
- Cellophane, polyglycolide, plastarch material, poly-3-hydroxybutyrate – biologically derived polymers
- Polycaprolactone
- Zein, shellac – biologically derived coating materials
References
- 1 2 "Matbase". Retrieved 6 February 2012.
- ↑ PLA MSDS. ampolymer.com
- ↑ Market Study Bioplastics, Ceresana, Dec 2011
- ↑ Martin, O; Avérous, L (2001). "Poly(lactic acid): plasticization and properties of biodegradable multiphase systems". Polymer. 42 (14): 6209–6219. doi:10.1016/S0032-3861(01)00086-6.
- 1 2 Anders Södergård, Mikael Stolt. "3. Industrial Production of High Molecular Weight Poly(Lactic Acid)". In Rafael Auras; Loong-Tak Lim; Susan E. M. Selke; Hideto Tsuji. Poly(Lactic Acid): Synthesis, Structures, Properties, Processing, and Applications. doi:10.1002/9780470649848.ch3.
- ↑ Kricheldorf, Hans R.; Jonté, J. Michael (1983). "New polymer syntheses". Polymer Bulletin. 9 (6–7). doi:10.1007/BF00262719.
- ↑ Jung, Yu Kyung; Kim, Tae Yong (2009). "Metabolic Engineering of Escherichia coli for the production of Polylactic Acid and Its Copolymers". Biotechnology and Bioengineering. 105 (1): 161. doi:10.1002/bit.22548. PMID 19937727.
- ↑ Södergård, Anders; Mikael Stolt (February 2002). "Properties of lactic acid based polymers and their correlation with composition". Progress in Polymer Science. 27 (6): 1123–1163. doi:10.1016/S0079-6700(02)00012-6.
- ↑ Middelton, John C.; Arthur J. Tipton (2000). "Synthetic biodegradable polymers as orthopedic devices". Biomaterial. 21 (23): 2335–2346. doi:10.1016/S0142-9612(00)00101-0.
- ↑ Gina L. Fiore; Feng Jing; Victor G. Young, Jr.; Christopher J. Cramer; Marc A. Hillmyer (2010). "High Tg Aliphatic Polyesters by the Polymerization of Spirolactide Derivatives". Polymer Chemistry. 1 (1): 870–877. doi:10.1039/C0PY00029A.
- ↑ Donald Garlotta (2001). "A Literature Review of Poly(Lactic Acid)". Journal of Polymers and the Environment. 9 (2).
- ↑ "Compare Materials: PLA and PETE". Makeitfrom.com. Retrieved 2011-04-11.
- ↑ Giordano, R.A., Wu, B.M., Borland, S.W., Cima, L.G., Sachs, E.M. and Cima, M.J., 1997. Mechanical properties of dense polylactic acid structures fabricated by three dimensional printing. Journal of Biomaterials Science, Polymer Edition, 8(1), pp.63-75.
- ↑ Tymrak, B.M., Kreiger, M. and Pearce, J.M., 2014. Mechanical properties of components fabricated with open-source 3-D printers under realistic environmental conditions. Materials & Design, 58, pp.242-246.
- ↑ Wittbrodt, B., & Pearce, J. M. (2015). The Effects of PLA Color on Material Properties of 3-D Printed Components. Additive Manufacturing. 8, 110–116 (2015). DOI: 10.1016/j.addma.2015.09.006
- ↑ Lam, C. X. F.; Olkowski, R. .; Swieszkowski, W. .; Tan, K. C.; Gibson, I. .; Hutmacher, D. W. (2008). "Mechanical and in vitro evaluations of composite PLDLLA/TCP scaffolds for bone engineering". Virtual and Physical Prototyping. 3 (4): 193–197. doi:10.1080/17452750802551298.
- ↑ Bose, S., Vahabzadeh, S. and Bandyopadhyay, A., 2013. Bone tissue engineering using 3D printing. Materials Today, 16(12), pp.496-504.
- ↑ Guo, Shuang-Zhuang; Yang, Xuelu; Heuzey, Marie-Claude; Therriault, Daniel (2015). "3D printing of a multifunctional nanocomposite helical liquid sensor". Nanoscale. 7 (15): 6451. doi:10.1039/C5NR00278H. PMID 25793923.
- ↑ "PLA". Reprap Wiki. 2011-04-04. Retrieved 2011-04-11.
- ↑ "PLA". MakerBot Industries. Retrieved 2011-04-11.
- 1 2 Rafael Auras; Loong-Tak Lim; Susan E. M. Selke; Hideto Tsuji (eds.). Poly(Lactic Acid): Synthesis, Structures, Properties, Processing, and Applications. doi:10.1002/9780470649848. ISBN 9780470293669.
- ↑ Nazre, A.; Lin, S. (1994). Harvey, J. Paul; Games, Robert F., eds. Theoretical Strength Comparison of Bioabsorbable (PLLA) Plates and Conventional Stainless Steel and Titanium Plates Used in Internal Fracture Fixation. p. 53. ISBN 0-8031-1897-X.
- ↑ "Bioengineers succeed in producing plastic without the use of fossil fuels". Physorg.com. Retrieved 2011-04-11.
- ↑ Yutaka Tokiwa; Buenaventurada P. Calabia; Charles U. Ugwu; Seiichi Aiba (September 2009). "Biodegradability of Plastics". International Journal of Molecular Science. 9 (9): 3722–3742. doi:10.3390/ijms10093722. PMC 2769161
. PMID 19865515.
- ↑ Pavia FC; La Carrubba V; Piccarolo S; Brucato V (August 2008). "Polymeric scaffolds prepared via thermally induced phase separation: tuning of structure and morphology". Journal of Biomedical Materials Research Part A. 2 (2): 459–466. doi:10.1002/jbm.a.31621. PMID 17975822.
External links
![]() |
Wikimedia Commons has media related to Polylactides. |