Bulletproof vest
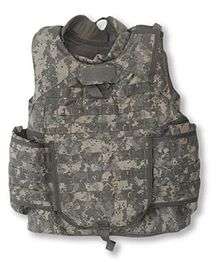
A ballistic vest or bullet-resistant vest, often called a bulletproof vest, is an item of personal armor that helps absorb the impact and reduce or stop penetration to the body from firearm-fired projectiles- and shrapnel from explosions, and is worn on the torso. Soft vests are made of many layers of woven or laminated fibers and can protect the wearer from small-caliber handgun and shotgun projectiles, and small fragments from explosives such as hand grenades.
These vests often have a ballistic plate inserted into the vest. Metal or ceramic plates can be used with a soft vest, providing additional protection against rifle rounds, and metallic components or tightly woven fiber layers can give soft armour resistance to stab and slash attacks from knives and similar close-quarter weapons. Soft vests are commonly worn by police forces, private citizens who are at risk of being shot (e.g., national leaders), security guards, and bodyguards, whereas hard-plate reinforced vests are mainly worn by combat soldiers, police tactical units, and hostage rescue teams.
Body armor may combine a ballistic vest with other items of protective clothing, such as a combat helmet. Vests intended for police and military use may also include ballistic shoulder and side protection armor components, and bomb disposal officers wear heavy armor and helmets with face visors and spine protection.
Overview
Ballistic vests use layers of very strong fibers to "catch" and deform a bullet, mushrooming it into a dish shape, and spreading its force over a larger portion of the vest fiber. The vest absorbs the energy from the deforming bullet, bringing it to a stop before it can completely penetrate the textile matrix. Some layers may be penetrated but as the bullet deforms, the energy is absorbed by a larger and larger fiber area.
While a vest can prevent bullet penetration, the vest and wearer still absorb the bullet's energy. Even without penetration, modern pistol bullets contain enough energy to cause blunt force trauma under the impact point. Vest specifications will typically include both penetration resistance requirements and limits on the amount of impact energy that is delivered to the body.
Vests designed for bullets offer little protection against blows from sharp implements, such as knives, arrows or ice picks, or from bullets manufactured of non-deformable materials, e.g., those containing a steel core instead of lead. This is because the impact force of these objects stays concentrated in a relatively small area, allowing them to puncture the fiber layers of most bullet-resistant fabrics. By contrast, stab vests provide better protection against sharp implements, but are generally less effective against bullets.
Textile vests may be augmented with metal (steel or titanium), ceramic or polyethylene plates that provide extra protection to vital areas. These hard armor plates have proven effective against all handgun bullets and a range of rifles. These upgraded ballistic vests have become standard in military use, as soft body armor vests are ineffective against military rifle rounds. Prison guards and police often wear vests which are designed specifically against bladed weapons and sharp objects. These vests may incorporate coated and laminated para-aramid textiles or metallic components.[1]
History
Early Modern era
In 1538, Francesco Maria della Rovere commissioned Filippo Negroli to create a bulletproof vest. In 1561, Maximilian II, Holy Roman Emperor is recorded as testing his armor against gun-fire. Similarly, in 1590 Sir Henry Lee expected his Greenwich armor to be "pistol proof". Its actual effectiveness was controversial at the time.[2] The etymology of "bullet" and the adjective form of "proof" in the late 16th century would suggest that the term "bulletproof" originated shortly thereafter.
During the English Civil War Oliver Cromwell's Ironside cavalry were equipped with Capeline helmets and musket-proof cuirasses which consisted of two layers of armor plate (in later studies involving X-ray a third layer was discovered which was placed in between the outer and inner layer). The outer layer was designed to absorb the bullet's energy and the thicker inner layer stopped further penetration. The armor would be left badly dented but still serviceable.[3] One of the first recorded descriptions of soft armor use was found in medieval Japan, with the armor having been manufactured from silk.[4]
Industrial era
One of the first commercially sold bulletproof armour was produced by a tailor in Dublin, Ireland in the 1840s. The Cork Examiner reported on his line of business in December 1847:[5]
- The daily melancholy announcements of assassination that are now disgracing the country, and the murderers permitted to walk quietly away and defy the law, have induced me to get constructed a garment, shot and ball proof, so that every man can be protected, and enabled to return the fire of the assassin, and thus soon put a stop to the cowardly conduct which has deprived society of so many excellent and valuable lives, spreading terror and desolation through the country. I hope in a few days to have a specimen garment on view at my warerooms.
Another soft ballistic vest, Myeonje baegab, was invented in Joseon, Korea in the 1860s shortly after the French campaign against Korea. The Heungseon Daewongun ordered development of bullet-proof armor because of increasing threats from Western armies. Kim Gi-Doo and Gang Yoon found that cotton could protect against bullets if 10 layers of cotton fabric were used. The vests were used in battle during the United States expedition to Korea, when the US Navy attacked Ganghwa Island in 1871. The US Navy captured one of the vests and took it to the US, where it was stored at the Smithsonian Museum until 2007. The vest has since been sent back to Korea and is currently on display to the public.[6]
Simple ballistic armor was sometimes constructed by criminals. During the 1880s, a gang of Australian bushrangers led by Ned Kelly made basic armour from plough blades. By this time the Victorian Government had a reward for the capture of a member of the Kelly Gang at £8,000 (equivalent to $2 million Australian dollars in 2005). One of the stated aims of Kelly was the establishment of a Republic in North East Victoria. Each of the four Kelly gang members had fought a siege at a hotel clad in suits of armour made from the mouldboards of ploughs. The maker's stamp (Lennon Number 2 Type) was found inside several of the plates. The men used the armour to cover their torsos, upper arms, and upper legs, and was worn with a helmet. The suits were roughly made on a creek bed using a makeshift forge and a stringy-bark log as a muffled anvil. They had a mass of around 44 kg (96 lb), making the wearer a spectacular sight yet proved too unwieldy during a police raid at Glenrowan. Their armour deflected many hits with none penetrating, but eventually was of no use as the suits lacked protection for the legs and hands. American outlaw and gunfighter Jim Miller, was infamous for wearing a steel breastplate over his frock coat as a form of body armor.[7] This plate saved Miller on two occasions; and it proved to be highly resistant to pistol bullets and shotguns. One example can be seen in his gun battle with a sheriff named George A. "Bud" Frazer, where the plate managed to deflect all bullets from the lawmen's six shooter after he tried to empty on Miller's chest.[8]
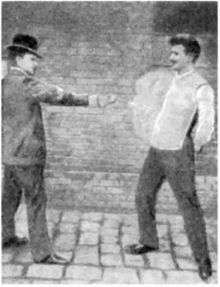
In 1881, Tombstone physician George E. Goodfellow noticed that a faro dealer Charlie Storms who was shot twice by Luke Short had one bullet stopped by a silk handkerchief in his breast pocket that prevented that bullet from penetrating.[9][10] In 1887, he wrote an article titled Impenetrability of Silk to Bullets[11] for the Southern California Practitioner documenting the first known instance of bulletproof fabric. He experimented with[12] silk vests resembling medieval gambesons, which used 18 to 30 layers of silk fabric to protect the wearers from penetration.
Fr. Kazimierz Żegleń used Goodfellow's findings to develop a bulletproof vest made of silk fabric at the end of the 19th century, which could stop the relatively slow rounds from black powder handguns. The vests cost $800 USD each in 1914, a small fortune given the $20/1oz-Au exchange-rate back then, equivalent to ~$50,000 circa 2016, exceeding mean annual income. On 28 June 1914, Archduke Franz Ferdinand of Austria, heir to the throne of Austria-Hungary was fatally shot; despite owning a silk bulletproof vest, which tests by Britain's Royal Armouries indicate would likely have stopped a bullet of that era, and despite being aware of potential threats to his life including an attempted assassination of his uncle a few years earlier, Ferdinand was not wearing his on that fateful day.[13][14]
A similar vest, made by Polish inventor Jan Szczepanik in 1901, saved the life of Alfonso XIII of Spain when he was shot by an attacker. By 1900, gangsters were wearing $800 silk vests to protect themselves.[15]
First World War

The combatants of World War I started the war without any attempt at providing the soldiers with body armor. Various private companies advertised body protection suits such as the Birmingham Chemico Body Shield, although these products were generally far too expensive for an average soldier.
The first official attempts at commissioning body armor were made in 1915 by the British Army Design Committee, in particular a 'Bomber's Shield' for the use of bomber pilots who were notoriously under-protected in the air from anti-aircraft bullets and shrapnel. The Experimental Ordnance Board also reviewed potential materials for bullet and fragment proof armor, such as steel plate. A 'necklet' was successfully issued on a small scale (due to cost considerations), which protected the neck and shoulders from bullets traveling at 600 feet per second with interwoven layers of silk and cotton stiffened with resin. The Dayfield body shield entered service in 1916 and a hardened breastplate was introduced the following year.[16]
The British army medical services calculated towards the end of the War, that three quarters of all battle injuries could have been prevented if an effective armor had been issued.
The French also experimented with steel visors attached to the Adrian helmet and 'abdominal armor' designed by General Adrian. These failed to be practical, because they severely impeded the soldier's mobility. The Germans officially issued body armor in the shape of nickel and silicon armor plates that was called 'Lobster armor' from late 1916. These were similarly too heavy to be practical for the rank-and-file, but were used by static units, such as sentries and occasionally the machine-gunners. An improved version, the Infantrie-Panzer, was introduced in 1918, with hooks for equipment.[17]

The United States developed several types of body armor, including the chrome nickel steel Brewster Body Shield, which consisted of a breastplate and a headpiece and could withstand Lewis Gun bullets at 2,700 ft/s (820 m/s), but was clumsy and heavy at 40 lb (18 kg). A scaled waistcoat of overlapping steel scales fixed to a leather lining was also designed; this armor weighed 11 lb (5.0 kg), fit close to the body, and was considered more comfortable.[18]
During the late 1920s through the early 1930s, gunmen from criminal gangs in the United States began wearing less-expensive vests made from thick layers of cotton padding and cloth. These early vests could absorb the impact of handgun rounds such as .22 Long Rifle, .25 ACP, .32 S&W Long, .32 S&W, .380 ACP, .38 Special and .45 ACP traveling at speeds of up to 300 m/s (980 ft/s). To overcome these vests, law enforcement agents such as the FBI began using the newer and more powerful .38 Super, and later the .357 Magnum cartridge.
Second World War

In 1940, the Medical Research Council in Britain proposed the use of a lightweight suit of armor for general use by infantry, and a heavier suit for troops in more dangerous positions, such as anti-aircraft and naval gun crews. By February 1941, trials had begun on body armor made of manganese steel plates. Two plates covered the front area and one plate on the lower back protected the kidneys and other vital organs. Five thousand sets were made and evaluated to almost unanimous approval - as well as providing adequate protection, the armor didn't severely impede the mobility of the soldier and were reasonably comfortable to wear. The armor was introduced in 1942 although the demand for it was later scaled down.[19] The Canadian Army in northwestern Europe also adopted this armor for the medical personnel of the 2nd Canadian Infantry Division.
The British company Wilkinson Sword began to produce flak jackets for bomber crew in 1943 under contract with the Royal Air Force. It was realised that the majority of pilot deaths in the air was due to low velocity fragments rather than bullets. Surgeon of the United States Army Air Forces, Colonel M. C. Grow, stationed in Britain, thought that many wounds he was treating could have been prevented by some kind of light armor. Two types of armor were issued for different specifications. These jackets were made of nylon fabric[20] and capable of stopping flak and shrapnel, but were not designed to stop bullets. Although they were considered too bulky for pilots using the Avro Lancaster bombers, they were adopted by United States Army Air Forces.
In the early stages of World War II, the United States also designed body armor for infantrymen, but most models were too heavy and mobility-restricting to be useful in the field and incompatible with existing required equipment. Near the middle of 1944, development of infantry body armor in the United States restarted. Several vests were produced for the US military, including but not limited to the T34, the T39, the T62E1, and the M12. The United States developed a vest using Doron Plate, a fiberglass-based laminate. These vests were first used in the Battle of Okinawa in 1945.[21]
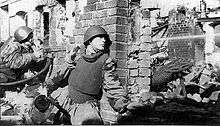
The Soviet Armed Forces used several types of body armor, including the SN-42 ("Stalnoi Nagrudnik" is Russian for "steel breastplate", and the number denotes the design year). All were tested, but only the SN-42 was put in production. It consisted of two pressed steel plates that protected the front torso and groin. The plates were 2 mm thick and weighed 3.5 kg (7.7 lb). This armor was supplied to SHISBr (assault engineers). The SN armor protected wearers from 9×19mm bullets fired by an MP 40 at around 100 meters, which made it useful in urban battles such as the Battle of Stalingrad. However, the SN's weight made it impractical for infantry in the open.
Postwar
During the Korean War several new vests were produced for the United States military, including the M-1951, which made use of fibre-reinforced plastic or aluminium segments woven into a nylon vest. These vests represented "a vast improvement on weight, but the armor failed to stop bullets and fragments very successfully," although officially they were claimed to be able to stop 7.62×25mm Tokarev pistol rounds at the muzzle. Developed by Natick Laboratories and introduced in 1967, T65-2 plate carriers were the first vests designed to hold hard ceramic plates, making them capable of stopping 7 mm rifle rounds.

These "Chicken Plates" were made of either boron carbide, silicon carbide, or aluminium oxide. They were issued to the crew of low-flying aircraft, such as the UH-1 and UC-123, during the Vietnam War.[22][23]
In 1969, American Body Armor was founded and began to produce a patented combination of quilted nylon faced with multiple steel plates. This armor configuration was marketed to American law enforcement agencies by Smith & Wesson under the trade name "Barrier Vest." The Barrier Vest was the first police vest to gain wide use during high threat police operations.
In 1971, research chemist Stephanie Kwolek discovered a liquid crystalline polymer solution. Its exceptional strength and stiffness led to the invention of Kevlar®, a synthetic fibre, woven into a fabric and layered, that, by weight, has five times the tensile strength of steel.[24] In the mid-1970s, DuPont the company which employed Kwolek introduced Kevlar. Immediately Kevlar was incorporated into a National Institute of Justice (NIJ) evaluation program to provide lightweight, able body armor to a test pool of American law enforcement officers to ascertain if everyday able wearing was possible. Lester Shubin, a program manager at the NIJ, managed this law enforcement feasibility study within a few selected large police agencies, and quickly determined that Kevlar body armor could be comfortably worn by police daily, and would save lives.
In 1975 Richard A. Armellino, the founder of American Body Armor, marketed an all Kevlar vest called the K-15, consisting of 15 layers of Kevlar that also included a 5" × 8" ballistic steel "Shok Plate" positioned vertically over the heart and was issued US Patent #3,971,072 for this innovation.[25] Similarly sized and positioned "trauma plates" are still used today on the front ballistic panels of most able vests, reducing blunt trauma and increasing ballistic protection in the center-mass heart/sternum area.
In 1976, Richard Davis, founder of Second Chance Body Armor, designed the company's first all-Kevlar vest, the Model Y. The lightweight, able vest industry was launched and a new form of daily protection for the modern police officer was quickly adapted. By the mid-to-late 1980s, an estimated 1/3 to 1/2 of police patrol officers wore able vests daily. By 2006, more than 2,000 documented police vest "saves" were recorded, validating the success and efficiency of lightweight able body armor as a standard piece of everyday police equipment.
Recent years
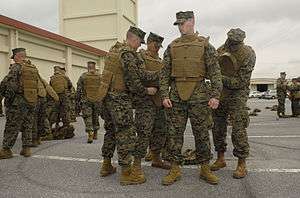
During the 1980s, the US military issued the PASGT kevlar vest, rated at NIJ level IIA,being able to stop pistol rounds (including 9 mm FMJ) and fragmentation. West Germany issued a similar rated vest called the Splitterschutzweste.
Kevlar soft armor had its shortcomings because if "large fragments or high velocity bullets hit the vest, the energy could cause life-threatening, blunt trauma injuries" in selected, vital areas. Ranger Body Armor was developed for the American military in 1991. Although it was the second modern US body armor that was able to stop rifle caliber rounds and still be light enough to be worn by infantry soldiers in the field, it still had its flaws: "it was still heavier than the concurrently issued PASGT (Personal Armor System for Ground Troops) anti-fragmentation armor worn by regular infantry and ... did not have the same degree of ballistic protection around the neck and shoulders." The format of Ranger Body Armor (and more recent body armor issued to US special operations units) highlights the trade-offs between force protection and mobility that modern body armor forces organizations to address.

Newer armor issued by the United States armed forces to large numbers of troops includes the United States Army's Improved Outer Tactical Vest and the United States Marine Corps Modular Tactical Vest. All of these systems are designed with the vest intended to provide protection from fragments and pistol rounds. Hard ceramic plates, such as the Small Arms Protective Insert, as used with Interceptor Body Armor, are worn to protect the vital organs from higher level threats. These threats mostly take the form of high velocity and armor-piercing rifle rounds. Similar types of protective equipment have been adopted by modern armed forces over the world.
Since the 1970s, several new fibers and construction methods for bulletproof fabric have been developed besides woven Kevlar, such as DSM's Dyneema, Honeywell's Gold Flex and Spectra, Teijin Twaron's Twaron, Pinnacle Armor's Dragon Skin, and Toyobo's Zylon. These newer materials are advertised as being lighter, thinner and more resistant than Kevlar, although they are much more expensive. The US military has developed body armor for the working dogs who aid GIs in battle.[26]
Since 2004, U.S. Special Operations Command has been at work on a new full-body armor that will rely on rheology, or the technology behind the elasticity of liquids in skin care and automotive products. Named TALOS, this new technology may be used in the future.[27]
Performance standards
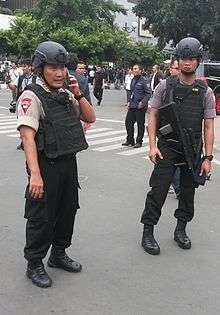
Due to the various types of projectile, it is often inaccurate to refer to a particular product as "bulletproof" because this implies that it will protect against any and all threats. Instead, the term bullet resistant is generally preferred.
Body armor standards are regional. Around the world ammunition varies and as a result the armor testing must reflect the threats found locally. Law enforcement statistics show that many shootings where officers are injured or killed involve the officer's own weapon.[28] As a result, each law enforcement agency or para-military organization will have their own standard for armor performance if only to ensure that their armor protects them from their own weapons. While many standards exist, a few standards are widely used as models. The US National Institute of Justice ballistic and stab documents are examples of broadly accepted standards. In addition to the NIJ, the UK Home Office Scientific Development Branch (HOSDB – formerly the Police Scientific Development Branch (PSDB)) standards are used by a number of other countries and organizations. These "model" standards are usually adapted by other counties by incorporation of the basic test methodologies with modification of the bullets that are required for test. NIJ Standard-0101.06 has specific performance standards for bullet resistant vests used by law enforcement. This rates vests on the following scale against penetration and also blunt trauma protection (deformation):[29]
Armor Level | Protection |
---|---|
Type I | This armor would protect against
It is no longer part of the standard. |
Type IIA | New armor protects against:
Conditioned armor protects against
It also provides protection against the threats mentioned in [Type I]. |
Type II | New armor protects against
Conditioned armor protects against
It also provides protection against the threats mentioned in [Types I and IIA]. |
Type IIIA | New armor protects against
Conditioned armor protects against
It also provides protection against most handgun threats, as well as the threats mentioned in [Types I, IIA, and II]. |
Type III | Conditioned armor protects against
It also provides protection against the threats mentioned in [Types I, IIA, II, and IIIA]. |
Type IV
|
Conditioned armor protects against
It also provides at least single hit protection against the threats mentioned in [Types I, IIA, II, IIIA, and III]. |
NIJ standards are used for law enforcement armors. The US and NATO military armor designs are tested using a standard set of test methods under ARMY MIL-STD-662F and STANAG 2920 Ed2.[32] This approach defines the test process under the 662F/2920 standard. Each armor program can select a unique series of projectiles and velocities as required. The DOD and MOD armor programs-of-record (MTV for example) procure armor using these test standards. In addition, special requirements can be defined under this process for armors for flexible rifle protection, fragment protection for the extremities, etc. These military procurement requirements do not relate to NIJ, HOSDB or ISO law enforcement armor standards, test methods, garment size, projectiles or velocities.
In addition to the NIJ and HOSDB law enforcement armor standards, other important standards include German Police TR-Technische Richtlinie, Draft ISO prEN ISO 14876, and Underwriters Laboratories (UL Standard 752).
Textile armor is tested for both penetration resistance by bullets and for the impact energy transmitted to the wearer. The "backface signature," or transmitted impact energy, is measured by shooting armor mounted in front of a backing material, typically oil-based modeling clay. The clay is used at a controlled temperature and verified for impact flow before testing. After the armor is impacted with the test bullet, the vest is removed from the clay and the depth of the indentation in the clay is measured.[29]
The backface signature allowed by different test standards can be difficult to compare. Both the clay materials and the bullets used for the test are not common. In general the British, German and other European standards allow 20–25 mm of backface signature, while the US-NIJ standards allow for 44 mm, which can potentially cause internal injury.[33] The allowable backface signature for body armor has been controversial from its introduction in the first NIJ test standard and the debate as to the relative importance of penetration-resistance vs. backface signature continues in the medical and testing communities.
In general a vest's textile material temporarily degrades when wet. Neutral water at room temp does not affect para-aramid or UHMWPE but acidic, basic and some other solutions can permanently reduce para-aramid fiber tensile strength.[34] (As a result of this, the major test standards call for wet testing of textile armor.[35]) Mechanisms for this wet loss of performance are not known. Vests that will be tested after ISO type water immersion tend to have heat sealed enclosures and those that are tested under NIJ type water spray methods tend to have water resistant enclosures.
From 2003 to 2005, a large study of the environmental degradation of Zylon armor was undertaken by the US-NIJ. This concluded that water, long-term use, and temperature exposure significantly affect tensile strength and the ballistic performance of PBO or Zylon fiber. This NIJ study on vests returned from the field demonstrated that environmental effects on Zylon resulted in ballistic failures under standard test conditions.[36]
Ballistic testing V50 and V0
Measuring the ballistic performance of armor is based on determining the kinetic energy of a bullet at impact (Ek = ½ mv2). Because the energy of a bullet is a key factor in its penetrating capacity, velocity is used as the primary independent variable in ballistic testing. For most users the key measurement is the velocity at which no bullets will penetrate the armor. Measuring this zero penetration velocity (v0) must take into account variability in armor performance and test variability. Ballistic testing has a number of sources of variability: the armor, test backing materials, bullet, casing, powder, primer and the gun barrel, to name a few.
Variability reduces the predictive power of a determination of V0. If for example, the v0 of an armor design is measured to be 1,600 ft/s (490 m/s) with a 9 mm FMJ bullet based on 30 shots, the test is only an estimate of the real v0 of this armor. The problem is variability. If the v0 is tested again with a second group of 30 shots on the same vest design, the result will not be identical.
Only a single low velocity penetrating shot is required to reduce the v0 value. The more shots made the lower the v0 will go. In terms of statistics, the zero penetration velocity is the tail end of the distribution curve. If the variability is known and the standard deviation can be calculated, one can rigorously set the V0 at a confidence interval. Test Standards now define how many shots must be used to estimate a v0 for the armor certification. This procedure defines a confidence interval of an estimate of v0. (See "NIJ and HOSDB test methods".)
v0 is difficult to measure, so a second concept has been developed in ballistic testing called the ballistic limit (v50). This is the velocity at which 50 percent of the shots go through and 50 percent are stopped by the armor. US military standard MIL-STD-662F V50 Ballistic Test define a commonly used procedure for this measurement. The goal is to get three shots that penetrate that are slower than a second faster group of three shots that are stopped by the armor. These three high stops and three low penetrations can then be used to calculate a v50 velocity.
In practice this measurement of v50 requires 1–2 vest panels and 10–20 shots. A very useful concept in armor testing is the offset velocity between the v0 and v50. If this offset has been measured for an armor design, then v50 data can be used to measure and estimate changes in v0. For vest manufacturing, field evaluation and life testing both v0 and v50 are used. However, as a result of the simplicity of making v50 measurements, this method is more important for control of armor after certification.
Military testing: fragment ballistics
After the Vietnam War, military planners developed a concept of “Casualty Reduction”.[37] The large body of casualty data made clear that in a combat situation, fragments, not bullets, were the most important threat to soldiers. After WWII, vests were being developed and fragment testing was in its early stages.[38] Artillery shells, mortar shells, aerial bombs, grenades, and antipersonnel mines are all fragmentation devices. They all contain a steel casing that is designed to burst into small steel fragments or shrapnel, when their explosive core detonates. After considerable effort measuring fragment size distribution from various NATO and Soviet bloc munitions, a fragment test was developed. Fragment simulators were designed, and the most common shape is a right circular cylinder or RCC simulator. This shape has a length equal to its diameter. These RCC Fragment Simulation Projectiles (FSPs) are tested as a group. The test series most often includes 2 grain (0.13 g), 4 grain (0.263 g), 16 grain (1.0 g), and 64 grain (4.2 g) mass RCC FSP testing. The 2-4-16-64 series is based on the measured fragment size distributions.
The second part of “Casualty Reduction” strategy is a study of velocity distributions of fragments from munitions.[39] Warhead explosives have blast speeds of 20,000 ft/s (6,100 m/s) to 30,000 ft/s (9,100 m/s). As a result, they are capable of ejecting fragments at very high speeds of over 3,300 ft/s (1,000 m/s), implying very high energy (where the energy of a fragment is ½ mass × velocity2, neglecting rotational energy). The military engineering data showed that, like the fragment size, the fragment velocities had characteristic distributions. It is possible to segment the fragment output from a warhead into velocity groups. For example, 95% of all fragments from a bomb blast under 4 grains (0.26 g) have a velocity of 3,000 ft/s (910 m/s) or less. This established a set of goals for military ballistic vest design.
The random nature of fragmentation required the military vest specification to trade off mass vs. ballistic-benefit. Hard vehicle armor is capable of stopping all fragments, but military personnel can only carry a limited amount of gear and equipment, so the weight of the vest is a limiting factor in vest fragment protection. The 2-4-16-64 grain series at limited velocity can be stopped by an all-textile vest of approximately 5.4 kg/m2 (1.1 lb/ft2). In contrast to the design of vest for deformable lead bullets, fragments do not change shape; they are steel and can not be deformed by textile materials. The 2-grain (0.13 g) FSP (the smallest fragment projectile commonly used in testing) is about the size of a grain of rice; such small fast moving fragments can potentially slip through the vest, moving between yarns. As a result, fabrics optimized for fragment protection are tightly woven, although these fabrics are not as effective at stopping lead bullets.
Backing materials for testing
Ballistic
One of the critical requirements in soft ballistic testing is measurement of "back side signature" (i.e. energy delivered to tissue by a non-penetrating projectile) in a deformable backing material placed behind the targeted vest. The majority of military and law enforcement standards have settled on an oil/clay mixture for the backing material, known as Roma Plastilena.[40] Although harder and less deformable than human tissue, Roma represents a “worst case” backing material when plastic deformations in the oil/clay are low (less than 20 mm).[41] (Armor placed over a harder surface is more easily penetrated.) The oil/clay mixture of "Roma" is roughly twice the density of human tissue and therefore does not match its specific gravity, however "Roma" is a plastic material that will not recover its shape elastically, which is important for accurately measuring potential trauma through back side signature.
The selection of test backing is significant because in flexible armor, the body tissue of a wearer plays an integral part in absorbing the high energy impact of ballistic and stab events. However the human torso has a very complex mechanical behavior. Away from the rib cage and spine, the soft tissue behavior is soft and compliant.[42] In the tissue over the sternum bone region, the compliance of the torso is significantly lower. This complexity requires very elaborate bio-morphic backing material systems for accurate ballistic and stab armor testing.[43] A number of materials have been used to simulate human tissue in addition to Roma. In all cases, these materials are placed behind the armor during test impacts and are designed to simulate various aspects of human tissue impact behavior.
One important factor in test backing for armor is its hardness. Armor is more easily penetrated in testing when backed by harder materials, and therefore harder materials, such as Roma clay, represent more conservative test methods.[44]
Backer type | Materials | Elastic/plastic | Test type | Specific gravity | Relative hardness vs gelatin | Application |
---|---|---|---|---|---|---|
Roma Plastilina Clay #1 | Oil/Clay mixture | Plastic | Ballistic and Stab | >2 | Moderately hard | Back face signature measurement. Used for most standard testing |
10% gelatin[45] | Animal protein gel | Visco-elastic | Ballistic | ~1 (90% water) | Softer than baseline | Good simulant for human tissue, hard to use, expensive. Required for FBI test methods |
20% gelatin[47] | Animal protein gel | Visco-elastic | Ballistic | ~1 (80% water) | Baseline | Good simulant for skeletal muscle. Provides dynamic view of event. |
HOSDB-NIJ Foam | Neoprene foam, EVA foam, sheet rubber | Elastic | Stab | ~1 | Slightly harder than gelatin | Moderate agreement with tissue, easy to use, low in cost. Used in stab testing |
Silicone gel | Long chain silicone polymer | Visco-elastic | Biomedical | ~1.2 | Similar to gelatin | Biomedical testing for blunt force testing, very good tissue match |
Pig or Sheep animal testing[48] | Live tissue | Various | Research | ~1 | Real tissue is variable[49] | Very complex, requires ethical review for approval |
Stab
Stab and spike armor standards have been developed using 3 different backing materials. The Draft EU norm calls out Roma clay, The California DOC called out 60% ballistic gelatin and the current standard for NIJ and HOSDB calls out a multi-part foam and rubber backing material.
- Using Roma clay backing, only metallic stab solutions met the 109 joule Calif. DOC ice pick requirement
- Using 10% Gelatin backing, all fabric stab solutions were able to meet the 109 joule Calif. DOC ice pick requirement.
- Most recently the Draft ISO prEN ISO 14876 norm selected Roma as the backing for both ballistics and stab testing.
This history helps explain an important factor in Ballistics and Stab armor testing, backing stiffness affects armor penetration resistance. The energy dissipation of the armor-tissue system is Energy = Force × Displacement when testing on backings that are softer and more deformable the total impact energy is absorbed at lower force. When the force is reduced by a softer more compliant backing the armor is less likely to be penetrated. The use of harder Roma materials in the ISO draft norm makes this the most rigorous of the stab standards in use today.
Rifle resistant armor
Because of the limitations of the technology a distinction is made between handgun protection and rifle protection. See NIJ levels 3 and 4 for typical requirements for rifle resistant armor. Broadly rifle resistant armor is of three basic types: ceramic plate-based systems, steel plate with spall fragmentation protective coating, and hard fiber-based laminate systems. Many rifle armor components contain both hard ceramic components and laminated textile materials used together. Various ceramic materials types are in use, however: aluminum oxide, boron carbide and silicon carbide are the most common.[50] The fibers used in these systems are the same as found in soft textile armor. However, for rifle protection high pressure lamination of ultra high molecular weight polyethylene with a Kraton matrix is the most common.
The Small Arms Protective Insert (SAPI) and the enhanced SAPI plate for the US DOD generally has this form.[51] Because of the use of ceramic plates for rifle protection, these vests are 5–8 times as heavy on an area basis as handgun protection. The weight and stiffness of rifle armor is a major technical challenge. The density, hardness and impact toughness are among the materials properties that are balanced to design these systems. While ceramic materials have some outstanding properties for ballistics they have poor fracture toughness. Failure of ceramic plates by cracking must also be controlled.[52] For this reason many ceramic rifle plates are a composite. The strike face is ceramic with the backface formed of laminated fiber and resin materials. The hardness of the ceramic prevents the penetration of the bullet while the tensile strength of the fiber backing helps prevent tensile failure. Examples of rifle resistant outer vests include the Interceptor body armor and the Improved Outer Tactical Vest.
Versus armor-piercing ammunition
The standards for armor-piercing rifle bullets aren't clear-cut, because the penetration of a bullet depends on the hardness of the target armor. However, there are a few general rules. For example, bullets with a soft lead-core and copper jacket are too easily deformed to penetrate hard materials, whereas rifle bullets manufactured with very hard core materials, like tungsten carbide, are designed for maximum penetration into hard armor.[53] Most other core materials would have effects between lead and tungsten carbide. Many common bullets, such as the 7.62×39mm M43 standard cartridge for the AK-47 rifle,[54] have a steel core with hardness rating ranging from Rc35 mild steel up to Rc45 medium hard steel.
Additionally, as the hardness of the bullet core increases, so must the amount of ceramic plating used to stop penetration. Like in soft ballistics, a minimum ceramic material hardness of the bullet core is required to damage their respective hard core materials, however in armor-piercing rounds the bullet core is eroded rather than deformed.[55]
The US Department of Defense uses two classes of protection from armor-piercing rifle bullets. The first, the Small Arms Protective Insert (SAPI), called for ceramic composite plates with a mass of 20–30 kg/m2 (4–5 lb/ft2). Later, the Enhanced SAPI (ESAPI) specification was developed to protect from more penetrative ammunition. ESAPI ceramic plates have a density of 35–45 kg/m2 (7–9 lb/ft2), and are designed to stop bullets like the .30-06 AP (M2) with an engineered hard core.
Cercom, now BAE systems, CoorsTek, Ceradyne, Tencate, Honeywell, DSM, Pinnacle Armor and a number of other engineering companies develop and manufacture the materials for composite ceramic rifle armor.[56]
Explosive protection
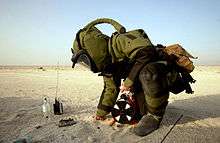
Bomb disposal officers often wear heavy armor[57][58][59] designed to protect against most effects of a moderate sized explosion, such as bombs encountered in terror threats. Full head helmet, covering the face and some degree of protection for limbs is mandatory in addition to very strong armor for the torso. An insert to protect the spine is usually applied to the back, in case an explosion blasts the wearer. Visibility and mobility of the wearer is severely limited, as is the time that can be spent working on the device. Armor designed primarily to counter explosives is often somewhat less effective against bullets than armor designed for that purpose. The sheer mass of most bomb disposal armor usually provides some protection, and bullet-specific trauma plates are compatible with some bomb disposal suits. Bomb disposal technicians try to accomplish their task if possible using remote methods (e.g., robots, line and pulleys). Actually laying hands on a bomb is only done in an extremely life-threatening situation, where the hazards to people and critical structures cannot be lessened by using wheeled robots or other techniques.
Stab and stab-ballistic armor
Early "ice pick" test
In the mid-1980s the state of California Department of Corrections issued a requirement for a body armor using a commercial ice pick as the test penetrator. The test method attempted to simulate the capacity of a human attacker to deliver impact energy with their upper body. As was later shown by the work of the former British PSDB, this test over stated the capacity of human attackers. The test used a drop mass or sabot that carried the ice pick. Using gravitational force, the height of the drop mass above the vest was proportional to the impact energy. This test specified 109 joules (81 ft·lb) of energy and a 7.3 kg (16 lb) drop mass with a drop height of 153 cm (60 in).
The ice pick has a 4 mm (0.16 in) diameter with a sharp tip with a 5.4 m/s (17 ft/s) terminal velocity in the test. The California standard did not include knife or cutting edge weapons in the test protocol. The test method used the oil/clay (Roma Plastilena) tissue simulant as a test backing. In this early phase only titanium and steel plate offerings were successful in addressing this requirement. Point Blank developed the first ice pick certified offerings for CA Department of Corrections in shaped titanium sheet metal. Vests of this type are still in service in US corrections facilities as of 2008.
Beginning in the early 1990s, an optional test method was approved by California which permitted the use of 10% ballistic gelatin as a replacement for Roma clay. The transition from hard, dense clay-based Roma to soft low-density gelatin allowed all textile solutions to meet this attack energy requirement. Soft all textile “ice pick” vests began to be adopted by California and other US states as a result of this migration in the test methods. It is important for users to understand that the smooth, round tip of the ice pick does not cut fiber on impact and this permits the use of textile based vests for this application.
The earliest of these “all” fabric vests designed to address this ice pick test was Warwick Mills’s TurtleSkin ultra tightly woven para-aramid fabric with a patent filed in 1993.[60] Shortly after the TurtleSkin work, in 1995 DuPont patented a medium density fabric that was designated as Kevlar Correctional.[61] It should be noted that these textile materials do not have equal performance with cutting-edge threats and these certifications were only with ice pick and were not tested with knives.
HOSDB-Stab and Slash standards
Parallel to the US development of “ice pick” vests, the British police, PSDB, was working on standards for knife-resistant body armor. Their program adopted a rigorous scientific approach and collected data on human attack capacity.[62] Their ergonomic study suggested three levels of threat: 25, 35 and 45 joules of impact energy. In addition to impact energy attack, velocities were measured and were found to be 10–20 m/s (much faster than the California test). Two commercial knives were selected for use in this PSDB test method. In order to test at a representative velocity, an air cannon method was developed to propel the knife and sabot at the vest target using compressed air. In this first version, the PSDB ’93 test also used oil/clay materials as the tissue simulant backing. The introduction of knives which cut fiber and a hard-dense test backing required stab vest manufacturers to use metallic components in their vest designs to address this more rigorous standard. The current standard HOSDB Body Armour Standards for UK Police (2007) Part 3: Knife and Spike Resistance is harmonized with the US NIJ OO15 standard, use a drop test method and use a composite foam backing as a tissue simulant. Both the HOSDB and the NIJ test now specify engineered blades, double-edged S1 and single-edge P1 as well as the spike.
In addition to the stab standards, HOSDB has developed a standard for slash resistance (2006). This standard, like the stab standards, is based on drop testing with a test knife in a mounting of controlled mass. The slash test uses the Stanley Utility knife or box cutter blades. The slash standard tests the cut resistance of the armor panel parallel to the direction of blade travel. The test equipment measures the force at the instant the blade tip produces a sustained slash through the vest. The criteria require that slash failure of the armor be greater than 80 newtons of force.[63]
Combination stab and ballistic vests
Vests that combined stab and ballistic protection were a significant innovation in the 1990s period of vest development. The starting point for this development were the ballistic-only offerings of that time using NIJ Level 2A, 2, and 3A or HOSDB HG 1 and 2, with compliant ballistic vest products being manufactured with areal densities of between 5.5 and 6 kg/m² (1.1 and 1.2 lb/ft² or 18 and 20 oz/ft²). However police forces were evaluating their “street threats” and requiring vests with both knife and ballistic protection. This multi-threat approach is common in the United Kingdom and other European countries and is less popular in the USA. Unfortunately for multi-threat users, the metallic array and chainmail systems that were necessary to defeat the test blades offered little ballistic performance. The multi-threat vests have areal densities are close to the sum of the two solutions separately. These vests have mass values in the 7.5–8.5 kg/m² (1.55–1.75 lb/ft²) range. Ref (NIJ and HOSDB certification listings). Rolls Royce Composites -Megit and Highmark produced metallic array systems to address this HOSDB standard. These designs were used extensively by the London Metropolitan Police Service and other agencies in the United Kingdom.
Standards update US and UK
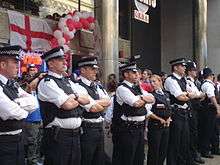
As vest manufactures and the specifying authorities worked with these standards, the UK and US Standards teams began a collaboration on test methods.[64] A number of issues with the first versions of the tests needed to be addressed. The use of commercial knives with inconsistent sharpness and tip shape created problems with test consistency. As a result, two new “engineered blades” were designed that could be manufactured to have reproducible penetrating behavior. The tissue simulants, Roma clay and gelatin, were either unrepresentative of tissue or not practical for the test operators. A composite-foam and hard-rubber test backing was developed as an alternative to address these issues. The drop test method was selected as the baseline for the updated standard over the air cannon option. The drop mass was reduced from the “ice pick test” and a wrist-like soft linkage was engineered into the penetrator-sabot to create a more realistic test impact. These closely related standards were first issued in 2003 as HOSDB 2003 and NIJ 0015. (The Police Scientific Development Branch (PSDB) was renamed the Home Office Scientific Development Branch in 2004.[65]
Stab and spike vests
These new standards created a focus on Level 1 at 25 joules (18 ft·lbf), Level 2 at 35 J (26 ft·lbf), Level 3 at 45 J (33 ft·lbf) protection as tested with the new engineered knives defined in these test documents. The lowest level of this requirement at 25 joules was addressed by a series of textile products of both wovens, coated wovens and laminated woven materials. All of these materials were based on Para-aramid fiber. The co-efficient of friction for ultra high molecular weigh polyethylene (UHMWPE) prevented its use in this application. The TurtleSkin DiamondCoat and Twaron SRM products addressed this requirement using a combination of Para-Aramid wovens and bonded ceramic grain. These ceramic-coated products do not have the flexibility and softness of un-coated textile materials.
For the higher levels of protection L2 and L3, the very aggressive penetration of the small, thin P1 blade has resulted in the continued use of metallic components in stab armor. In Germany, Mehler Vario Systems developed hybrid vests of woven para-aramid and chainmail, and their solution was selected by London's Metropolitan Police Service. Another German company BSST, in cooperation with Warwick Mills, has developed a system to meet the ballistic-stab requirement using Dyneema laminate and an advanced metallic-array system, TurtleSkin MFA. This system is currently implemented in the Netherlands. The trend in multi threat armor continues with requirements for needle protection in the Draft ISO prEN ISO 14876 norm. In many countries there is also an interest to combine military style explosive fragmentation protection with bullet-ballistics and stab requirements.
Vest sizing, carriers and encapsulation
In order for ballistic protection to be wearable the ballistic panels and hard rifle-resistant plates are fitted inside a special carrier. The carrier is the visible part of a ballistic vest. The most basic carrier includes pockets which hold the ballistic panels and straps for mounting the carrier on the user. There are two major types of carriers: military or tactical carriers that are worn over the shirt, and covert law enforcement type carriers that are worn under the shirt.
Military carriers
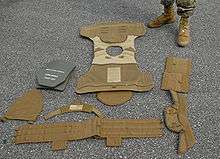
The military type of carrier, English police waistcoat carrier, or police tactical carrier most typically has a series of webbing, hook and loop, and snap type connectors on the front and back face. This permits the wearer to mount various gear to the carrier in many different configurations. This load carriage feature is an important part of uniform and operational design for police weapons teams and the military.
In addition to load carriage, this type of carrier may include pockets for neck protection, side plates, groin plates, and backside protection. Because this style of carrier is not close fitting, sizing in this system is straightforward for both men and women, making custom fabrication unnecessary.
Concealable carriers
Law enforcement carriers in some countries are concealable. The carrier holds the ballistic panels close to the wearer's body and a uniform shirt is worn over the carrier. This type of carrier must be designed to conform closely to the officer's body shape. For concealable armor to conform to the body it must be correctly fitted to a particular individual. Many programs specify full custom measurement and manufacturing of armor panels and carriers to ensure good fit and comfortable armor. Officers who are either female or significantly overweight have more difficulty in getting accurately measured and having comfortable armor fabricated.[66]
Vest slips
A third textile layer is often found between the carrier and the ballistic components. The ballistic panels are covered in a coated pouch or slip. This slip provides the encapsulation of the ballistic materials. Slips are manufactured in two types: heat sealed hermetic slips and simple sewn slips. For some ballistic fibers such as Kevlar the slip is a critical part of the system. The slip prevents moisture from the user's body from saturating the ballistic materials. This protection from moisture cycling increases the useful life of the armor.[67]
Research
Progress in fiber math
In recent years, advances in material science have opened the door to the idea of a literal "bulletproof vest" able to stop handgun and rifle bullets with a soft textile vest, without the assistance of additional metal or ceramic plating. However, progress is moving at a slower rate compared to other technical disciplines. The most recent offering from Kevlar, Protera, was released in 1996. Current soft body armor can stop most handgun rounds (which has been the case for roughly 15 years ), but armor plates are needed to stop rifle rounds and steel-core handgun rounds such as 7.62×25mm. The para-aramids have not progressed beyond the limit of 23 grams per denier in fiber tenacity.
Modest ballistic performance improvements have been made by new producers of this fiber type.[68] Much the same can be said for the UHMWPE material; the basic fiber properties have only advanced to the 30–35 g/d range. Improvements in this material have been seen in the development of cross-plied non-woven laminate, e.g. Spectra Shield. The major ballistic performance advance of fiber PBO is known as a "cautionary tale" in materials science.[69] This fiber permitted the design of handgun soft armor that was 30–50% lower in mass as compared to the aramid and UHMWPE materials. However this higher tenacity was delivered with a well-publicized weakness in environmental durability.
Akzo-Magellan (now DuPont) teams have been working on fiber called M5 fiber; however, its announced startup of its pilot plant has been delayed more than 2 years. Data suggests if the M5 material can be brought to market, its performance will be roughly equivalent to PBO.[70] In May 2008, the Teijin Aramid group announced a “super-fibers” development program. The Teijin emphasis appears to be on computational chemistry to define a solution to high tenacity without environmental weakness.
The materials science of second generation “super” fibers is complex, requires large investments, and represent significant technical challenges. Research aims to develop artificial spider silk which could be super strong, yet light and flexible.[71] Other research has been done to harness nanotechnology to help create super-strong fibers that could be used in future bulletproof vests.
Textile wovens and laminates research
Finer yarns and lighter woven fabrics have been a key factor in improved ballistic results. The cost of ballistic fiber goes up dramatically as yarn size goes down, so it is unclear how long this trend can continue. The current practical limit of fiber size is 200 denier with most wovens limited at the 400 denier level. Three-dimensional weaving with fibers connecting flat wovens together into a 3D system are being considered for both hard and soft ballistics. Team Engineering Inc is designing and weaving these multi layer materials. Dyneema DSM has developed higher performance laminates using a new, higher strength fiber designated SB61, and HB51. DSM feels this advanced material provides some improved performance, however the SB61 “soft ballistic” version has been recalled.[72] At the Shot Show in 2008, a unique composite of interlocking steel plates and soft UHWMPE plate was exhibited by TurtleSkin.[73] In combination with more traditional woven fabrics and laminates a number of research efforts are working with ballistic felts. Tex Tech has been working on these materials. Like the 3D weaving, Tex Tech sees the advantage in the 3-axis fiber orientation.
Fibers used
Ballistic nylon (until the 1970) or Kevlar or Spectra (a competitor for Kevlar) or the polyethylene fiber could be used to manufacture bullet proof vests. The vests of the time were made of ballistic nylon & supplemented by plates of fiber-glass, steel, ceramic, titanium, Doron & composites of ceramic and fiberglass the last being the most effective. One should not forget that there is another known para aramid fiber called Twaron, produced in the Netherlands and is a direct competitor of Kevlar.
Manufacturing process
a. Making the panel cloth- 1. To make Kevlar cloth, the Kevlar yarns are woven in the simplest pattern, plain or tabby weave. which is merely the over & under pattern of threads the interlace alternatively. 2. Unlike Kevlar, the Spectra used in bulletproof vests is usually not woven. instead the strong polyethelene polymer filaments are spun into fibers that are then laid parallel to each other. Resin is used to coat the fibers, sealing them together to form a sheet of Spectra cloth. Two sheets of cloth are then placed at right angles to one another and again bonded, forming a nonwoven fabric that is next sandwiched between two sheets of polyethelene film. The vest shape can then be cut from the material.
b. Cutting The panels-
C. Sewing the ballistic panels-
d. Finishing the vest- The shells for the panels are sewn together in the same standard industrial sewing machines and standard sewing practices. The panels are then slipped inside the shells and the accessories—such as the straps—are sewn on. The finished bulletproof vest is boxed and shipped to the customer.
Working principle
When a hand gun bullet strikes body armor, it is caught in a "web" of very strong fibers. These fibers absorb and disperse the impact energy that is transmitted to the bullet proof vest from the bullet causing the bullet to deform, otherwise known as a "mushroom". Additional energy is absorbed by each successive layer or material in bullet proof vests until such time as the bullet has been stopped.
Ceramic plates work by locally shattering where the projectile strikes, and are capable of dispersing the energy of the projectile to the point where the bullet has been stopped. Unfortunately, this means that ceramic plates become progressively less capable of stopping additional bullets, and may be rendered unusable after a certain number of hits have been taken.
Developments in ceramic armor
Ceramic materials, materials processing and progress in ceramic penetration mechanics are significant areas of academic and industrial activity. This combined field of ceramics armor research is broad and is perhaps summarized best by The American Ceramics Society. ACerS has run an annual armor conference for a number of years and compiled a proceedings 2004–2007.[74] An area of special activity pertaining to vests is the emerging use of small ceramic components. Large torso sized ceramic plates are complex to manufacture and are subject to cracking in use. Monolithic plates also have limited multi hit capacity as a result of their large impact fracture zone These are the motivations for new types of armor plate. These new designs use two- and three-dimensional arrays of ceramic elements that can be rigid, flexible or semi-flexible. Dragon Skin body armor is one of these systems. European developments in spherical and hexagonal arrays have resulted in products that have some flex and multi hit performance.[75] The manufacture of array type systems with flex, consistent ballistic performance at edges of ceramic elements is an active area of research. In addition advanced ceramic processing techniques arrays require adhesive assembly methods. One novel approach is use of hook and loop fasteners to assemble the ceramic arrays.[76]
Nanomaterials in ballistics
Currently, there are a number of methods by which nanomaterials are being implemented into body armor production. The first, developed at University of Delaware is based on nanoparticles within the suit that become rigid enough to protect the wearer as soon as a kinetic energy threshold is surpassed. These coatings have been described as shear thickening fluids.[77] These nano-infused fabrics have been licensed by BAE systems, but as of mid-2008, no products have been released based on this technology.
In 2005 an Israeli company, ApNano, developed a material that was always rigid. It was announced that this nanocomposite based on tungsten disulfide nanotubes was able to withstand shocks generated by a steel projectile traveling at velocities of up to 1.5 km/s.[78] The material was also reportedly able to withstand shock pressures generated by other impacts of up to 250 metric tons-force per square centimeter (24.5 gigapascals; 3,550,000 psi). During the tests, the material proved to be so strong that after the impact the samples remained essentially unmarred. Additionally, a study in France tested the material under isostatic pressure and found it to be stable up to at least 350 tf/cm² (34 GPa; 5,000,000 psi).
As of mid-2008, spider silk bulletproof vests and nano-based armors are being developed for potential market release . Both the British and American militaries have expressed interest in a carbon fiber woven from carbon nanotubes that was developed at University of Cambridge and has the potential to be used as body armor.[79] In 2008, large format carbon nanotube sheets began being produced at Nanocomp.
Graphene composite
In late 2014, researchers began studying and testing graphene as a material for use in body armor. Graphene is manufactured from carbon and is the thinnest, strongest, and most conductive material on the planet. Taking the form of hexagonally-arranged atoms, its tensile strength is known to be 200 times greater than steel, but studies from Rice University have revealed it is also 10 times better than steel at dissipating energy, an ability that had previously not been thoroughly explored. To test its properties, the University of Massachusetts stacked together graphene sheets only a single carbon atom thick, creating layers ranging in thickness from 10 nanometers to 100 nanometers from 300 layers. Microscopic spherical silica "bullets" were fired at the sheets at speeds of up to 3 km (1.9 mi) per second, almost nine times the speed of sound. Upon impact, the projectiles deformed into a cone shape around the graphene before ultimately breaking through. In the three nanoseconds it held together however, the transferred energy traveled through the material at a speed of 22.2 km (13.8 mi) per second, faster than any other known material. If the impact stress can be spread out over a large enough area that the cone moves out at an appreciable velocity compared with the velocity of the projectile, stress will not be localized under where it hit. Although a wide impact hole opened up, a composite mixture of graphene and other materials could be made to create a new, revolutionary armor solution.[80][81]
Legality
Australia
In Australia, it is illegal to import body armour without prior authorisation from Australian Customs and Border Protection Service.[82] It is also illegal to possess body armour without authorization in South Australia,[83] Victoria,[84] Northern Territory,[85] ACT,[86] Queensland [87] & New South Wales.[88] In 2009 Tasmania considered passing control legislation as well.[89]
Canada
In all Canadian provinces except for Alberta, British Columbia and Manitoba, it is legal to wear and to purchase body armour such as ballistic vests. Under the laws of these provinces, it is illegal to possess body armour without a license (unless exempted) issued by the provincial government. Nova Scotia has passed similar laws, but they are not yet in force.
According to the Body Armour Control Act of Alberta which came into force on June 15, 2012, any individual in possession of a valid firearms licence under the Firearms Act of Canada can legally purchase, possess and wear body armour.[90]
The Netherlands
The civilian ownership of body armour is unregulated in the Netherlands and body armour in various ballistic grades is sold by a range of different vendors, mainly aimed at providing to security guards and VIP's. The use of body armour while committing a crime is not an additional offense in itself, but may be interpreted as so under different laws such as resisting arrest.
United States
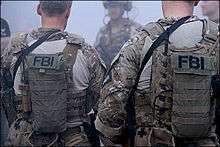
United States law restricts possession of body armor for convicted violent felons. Many U.S. states also have penalties for possession or use of body armor by felons. In other states, such as Kentucky, possession is not prohibited, but probation or parole is denied to a person convicted of committing certain violent crimes while wearing body armor and carrying a deadly weapon. Most states do not have restrictions for non-felons.
Italy
In Italy, the purchase, ownership and wear of ballistic vests and body armor is not subject to any restriction, except for those ballistic protections that are developed under strict military specifications and/or for main military usage, thus considered by the law as "armament materials" and forbidden to civilians. Furthermore, a number of laws and court rulings during the years have rehearsed the concept of a ballistic vest being mandatory to wear for those individuals who work in the private security sector.
European Union
In European Union import and sale of ballistic vests and body armor are allowed in Europe, except protections that are developed under strict military specifications and/or for main military usage, shield above the level of protection NIJ 4, thus considered by the law as "armament materials" and forbidden to civilians. There are many shops in Europe that sell ballistic vests and body armor, used or new.
See also
- Brigandine (an earlier form of vest, used to defend against swords, knives, etc.)
- Buff coat (an early form of ballistic vest, suitable for use only against pistol balls, but not musket balls)
- Flak jacket (a form of ballistic vest used for protection against explosives and shell fragments)
- Hauberk (an earlier form of body armor, used to defend against swords, knives, etc.)
- Mail (armour)
- Terminal ballistics
References
- ↑ http://www.tigerflare.com/component/content/article/1-latest-news/351-ballistic-vest-review
- ↑ Williams, Allan (2003). The Knight and the Blast Furnace: A History of the Metallurgy of Armour in the Middle Ages & the Early Modern Period. Boston: Brill Academic Publishers. ISBN 978-90-04-12498-1.
- ↑ Ricketts, H, Firearms p. 5
- ↑ "Selection and Application guide to Personal Body Armor" (PDF). National Criminal Justice Reference Service. Retrieved 2009-12-30.
- ↑ "The Landlord's Protective Garment". The Cork Examiner. December 6, 1847.
- ↑ Seoul Yonhap News Agency, 1 April 2008
- ↑ O'Neal, Bill (1979). Encyclopedia of Western Gunfighters. University of Oklahoma Press. pp. 230–233. ISBN 0-8061-1508-4
- ↑ Metz, Leon Claire (2003). The Encyclopedia of Lawmen, Outlaws, and Gunfighters. Checkmark Books. pp. 172–173. ISBN 0-8160-4543-7.
- ↑ Erwin, Richard E. (1993). The Truth about Wyatt Earp (2nd ed.). Carpinteria, CA: O.K. Press. ISBN 9780963393029.
- ↑ Edwards, Josh (May 2, 1980). "George Goodfellow's Medical Treatment of Stomach Wounds Became Legendary". The Prescott Courier. pp. 3–5.
- ↑ "Dr. George Goodfellow". Archived from the original on 20 December 2014. Retrieved 8 March 2013.
- ↑ Hollington, Kris. "Staying Alive". Retrieved 4 March 2013.
- ↑ "Tests prove that a bulletproof silk vest could have stopped the first world war". The Guardian. July 29, 2014. Retrieved November 13, 2015.
- ↑ "Could the Bulletproof Silk Vest Stop the Assassination Which Sparked WWI? Tests Say Yes". War History Online. August 8, 2014. Retrieved November 13, 2015.
- ↑ Hollington, Kris (2008). Wolves, Jackals, and Foxes: The Assassins Who Changed History. St. Martin's Press. ISBN 9781429986809.
- ↑ Stephen Bull (2002). World War I Trench Warfare (2): 1916-18. Osprey Publishing. p. 12.
- ↑ David Payne. "Body Armour For The Western Front In The Great War".
- ↑ http://www.westernfrontassociation.com/great-war-on-land/73-weapons-equipment-uniforms/879-body-armour.html
- ↑ "British Body Armour in WW II".
- ↑ Stephan, Restle (1997). Ballistische Schutzwesten und Stichschutzoptionen. Bischofszell: Kabinett Verlag, p.61.
- ↑ King, Ludlow (January–February 1953). "Lightweight Body Armor". Ordnance. Retrieved 2008-11-12.
- ↑ Barron, Edward R.; Park, Alice F; Alesi, Anthony L (January 1969). "Body Armor for Aircrewman" (PDF). U.S. Army Natick Laboratories. Retrieved 2008-11-12.
- ↑ "Who are you calling Chicken?". VietnamGear.com. 2006-07-03. Retrieved 2008-11-12.
- ↑ "Stephanie L. Kwolek". Chemical Heritage Foundation. Retrieved 18 November 2016.
- ↑ "US Patent 3971072 – Lightweight armor and method of fabrication". PatentStorm LLC. 1976-07-27. Retrieved 2008-11-12.
- ↑ Ransford, Cheryl (2005-02-25). "Canine Units in Afghanistan Issued New Protective Vests". DefenseLINK. American Forces Press Service. Archived from the original on 13 January 2008. Retrieved 2008-01-25.
Army Sgt. 1st Class Erika Gordon, kennel master for the 25th Military Police Company, uses a building for cover while her military working dog, Hanna, clears a doorway at the military-operations-in-urban-terrain training site at Bagram Air Base, Afghanistan recently.
- ↑ Slice of MIT (2013). "What's the future of armor: liquid or solid?" http://alum.mit.edu/pages/sliceofmit/2013/08/07/whats-the-future-of-armor-liquid-or-solid/ Retrieved 2013-08-22.
- ↑ Citation:Terry D. Edwards, (1995) "Felonious killings of state police and highway patrol officers: a descriptive and comparative evaluation", American Journal of Police, Vol. 14 Iss: 2, pp.89 - 105
- 1 2 "Ballistic Resistance of Body Armor NIJ Standard-0101.06" (PDF). NIJ Standards. United States Department of Justice. July 2008. Retrieved 2008-11-13.
- ↑ Eger, Chris (21 March 2016). "Extreme penetrator .45-70 rounds at work". Guns.com. Retrieved 2 August 2016.
- ↑ http://www.lehighdefense.com/products/45-70-government-305gr-xtreme-penetrator-ammo?variant=2921393476
- ↑ "MIL-STD-662F V50 Ballistic Test for Armor" Army Research Laboratory, Weapons and Materials Research Directorate Publication Date:Dec 18, 1997
- ↑ Wilhelm, M; Bir, C (2008). "Injuries to law enforcement officers: The backface signature injury". Forensic Science International. 174 (1): 6–11. doi:10.1016/j.forsciint.2007.02.028. ISSN 0379-0738. PMID 17434273.
- ↑ Kevlar, Twaron, Dyneema, Spectra technical data
- ↑ NIJ, HOSDB, US-Army and ISO ballistic test methods
- ↑ "Third Status Report to the Attorney General on Body Armor Safety Initiative Testing and Activities"
- ↑ Dusablon, L V (December 1972). "The Casualty Reduction Analysis Model for Personnel Armor Systems". U.S. Army Natick Research, Development and Engineering Center.
- ↑ Design Information for Construction of Light Personnel Armor. Authors: Willard R. Beye 1950 Midwest Research Inst Kansas City Mo
- ↑ Johnson, W., Collins, C., and Kindred, F., A Mathematical Model for Predicting Residual Velocities of Fragments After Perforating Helmets and Body Armor, Ballistic Research Laboratories Technical Note no. 1705, October 1968
- ↑ "Detail". Sculpture House. Retrieved 2009-04-06.
- ↑ Roberts, Jack C; Ward, Emily E; Merkle, Andrew C; O'Connor, James V (May 2007). "Assessing Behind Armor Blunt Trauma in Accordance With the National Institute of Justice Standard for Personal Body Armor Protection Using Finite Element Modeling". Journal of Trauma-Injury Infection & Critical Care. Lippincott Williams & Wilkins. 62 (5): 1127–1133. doi:10.1097/01.ta.0000231779.99416.ee. PMID 17495712.
- ↑ Wound ballistic simulation : Assessment of the legitimacy of law enforcement firearms ammunition by means of wound ballistic simulation,Jussila, Jorma,University of Helsinki, Faculty of Medicine, Institute of Clinical Medicine 2005-01, Doctoral dissertation
- ↑ Thoracic Model Analysis Using Finite Element Modeling and Vibration Table Testing Dr. Peter Matic, Dr. Alan Leung and Mr. Kirth Simmonds, Multifunctional Materials Branch, Naval Research Laboratory, Code 6350, 4555 Overlook Ave., SW, Washington, DC 20375
- ↑ Fackler, ML. And John A. Malinowski (1988). "Ordnance gelatin for Ballistic Studies – Detrimental Effect of Excess Heat Used in Gelatin Preparation;". The American Journal of Forensic Medicine and Pathology. 9 (3): 218–219. doi:10.1097/00000433-198809000-00008. PMID 3177350.
- ↑ Jussila, Jorma (May 2004). "Preparing Ballistic Gelatine—review and proposal for a standard method". Forensic Science International. 141 (2–3): 91–98. doi:10.1016/j.forsciint.2003.11.036. PMID 15062946.
- ↑ Kenedi, R M; Gibson, T; Evans, J H; Barbenel J C (1975). "Tissue Mechanics". Physics in Medicine and Biology. IOP Publishing Limited. 20 (5): 699–717. doi:10.1088/0031-9155/20/5/001.
- ↑ Prather, Russell; Swann, Conrad L; Hawkinns, Clarence E (1977). "Backface Signatures of Soft Body Armors and the Associated Trauma Effects". ARCSL-TR-77055.
- ↑ Song, Bo; Chen, Weinong; Ge, Yun; Weerasooriya, Tusit (2007). "Dynamic and quasi-static compressive response of porcine muscle". Journal of Biomechanics. Elsevier Ltd. 40 (13): 2999–3005. doi:10.1016/j.jbiomech.2007.02.001. PMID 17448479.
- ↑ Berlin, R.H., B. Janzon,B. Rybeck, J. Sandegård and T. Seeman (1977) Local effects of assault rifle bullets in live tissues. Part II. Further studies in live tissues and relations to some simulant media; Acta Chir. Scand. Suppl. 477, 1–48, 1977
- ↑ Holmquist, T J; Rajendran, A J; Templeton, D W; Bishnoi K D (January 1999). "A Ceramic Armor Material Database". TACOM RD&E Center.
- ↑ Lee, B L; Walsh, T F; Won, S T; Patts, H M; Mayer, A H (2001). "Penetration Failure Mechanisms of Armor-Grade Fiber Composites under Impact". Journal of Composite Materials. 35 (18): 1605–1633. doi:10.1106/YRBH-JGT9-U6PT-L555.
- ↑ Savage, G (August 1990). "Ceramic Armour". Journal of the Institute of Metals. 6 (8): 487–492.
- ↑ Manfred Held "Threats to Military Transport Aircraft:A Technical Review " Journal of Battlefield Technology, Vol 6, No 2, July 2003 11440-5113 © 2003 Argos Press
- ↑ Joe PoyerThe AK-47 and AK-74 Kalashnikov Rifles and their Variations North Cape Publications Copyright 2004
- ↑ Charles E. Anderson, Jr., James D. Walker, "An analytical model for dwell and interface defeat" International Journal of Impact Engineering vol 31 issue 9 2004.
- ↑ "Corporate Member Listing". Ceramics.org. Archived from the original on 28 August 2010. Retrieved 2010-08-12.
- ↑ Stewart, Ian B.; Stewart, Kelly L.; Worringham, Charles J.; Costello, Joseph T. (2014-01-01). "Physiological tolerance times while wearing explosive ordnance disposal protective clothing in simulated environmental extremes". PLOS ONE. 9 (2): e83740. doi:10.1371/journal.pone.0083740. ISSN 1932-6203. PMC 3931617
. PMID 24586228.
- ↑ Costello, Joseph T.; Stewart, Kelly L.; Stewart, Ian B. (2015-08-01). "Inside the 'Hurt Locker': The Combined Effects of Explosive Ordnance Disposal and Chemical Protective Clothing on Physiological Tolerance Time in Extreme Environments". The Annals of Occupational Hygiene. 59 (7): 922–931. doi:10.1093/annhyg/mev029. ISSN 1475-3162. PMID 25878167.
- ↑ Costello, Joseph T.; Stewart, Kelly L.; Stewart, Ian B. (2015-01-01). "The effects of metabolic work rate and ambient environment on physiological tolerance times while wearing explosive and chemical personal protective equipment". BioMed Research International. 2015: 857536. doi:10.1155/2015/857536. ISSN 2314-6141. PMC 4383354
. PMID 25866818.
- ↑ "US Patent 5565264 – Protective fabric having high penetration resistance". PatentStorm LLC. 1996-10-15. Retrieved 2008-11-13.
- ↑ Foy, Brian E. (1996-11-26). "Penetration-resistant aramid article". Google Patents. Google. Retrieved 2008-11-13.
- ↑ Chadwick, E K J; Nicol, A C; Lane, J V; Gray, T G F (1999-11-25). "Biomechanics of knife stab attacks". Forensic Science International. 105 (1): 35–44. doi:10.1016/S0379-0738(99)00117-6. PMID 10605074.
- ↑ http://tna.europarchive.org/20100413151426/http://scienceandresearch.homeoffice.gov.uk/hosdb/publications/protective-equipment/index.html
- ↑ "Taking the Stab Out of Stabbings". TechBeat, Spring 2000 (whole issue), p. 1 (PDF version).
- ↑ The Home Office Departmental Report 2005, p. 19. Home Office, June 2005.
- ↑ Robin H Hooper, Why Do Police Officers Leave Their Body Armour in the Cupboard?, Contemporary Ergonomics 1999, (ed. Margaret Hanson, E. J. Lovesey, S. A. Robertson), (Padstow, UK: T.J. International) pp. 358-362.
- ↑ Journal of Applied Polymer Science "Kinetics for the tensile strength degradation of nylon and Kevlar yarns" I. Auerbach Aerodynamics Department, Sandia National Laboratories, Albuquerque, New Mexico 87185
- ↑ Heterocyclic Aramide Fibers – Production Principles, Properties and Application, Nikolay N. Machalaba and Kirill E. Pekin
- ↑ Morphological study on poly-p-phenylenebenzobisoxazole (PBO) fiber, Tooru Kitagawa *, Hiroki Murase, Kazuyuki Yabuki Toyobo Research Center, Toyobo Co. Ltd., 2-1-1, Katata, Ohtsu 520-02 Japan
- ↑ Cunniff, Philip M.; Auerbach, Margaret; Vetter, Eugene; Sikkema, Doetze J. "High Performance "M5" Fiber for Ballistics/Structural Composites" (PDF).
- ↑ Lazaris, Anthoula; Arcidiacono, Steven; Huang, Yue; Zhou, Jiang-Feng; Duguay, François; Chretien, Nathalie; Welsh, Elizabeth A; Soares, Jason W; Karatza, Costas N (2002). "Spider Silk Fibers Spun from Soluble Recombinant Silk Produced in Mammalian Cells". Science. 295 (5554): 472–476. doi:10.1126/science.1065780. PMID 11799236.
- ↑ NLECTC Body Armor Testing Program Database Archived May 28, 2007, at the Wayback Machine.
- ↑
- ↑ Wiley Advances in Ceramic Armor III ACS
- ↑ Tencate AresShield
- ↑ Foster Miller Last Armor.
- ↑ Lee, Young S; Wetzel, E D; Wagner, N J (July 2003). "The ballistic impact characteristics of Kevlar woven fabrics impregnated with a colloidal shear thickening fluid". Journal of Materials Science. 38 (13): 2825–2833. doi:10.1023/A:1024424200221.
- ↑ "Nano-Armor: Protecting The Soldiers Of Tomorrow". Isracast.com. Archived from the original on 6 April 2009. Retrieved 2009-04-06.
- ↑ Rincon, Paul (2007-10-23). "Science/Nature | Super-strong body armour in sight". BBC News. Retrieved 2009-04-06.
- ↑ World's Strongest Material In Body Armour Trials - Armedforces-Int.com, 1 December 2014
- ↑ Graphene could find use in lightweight ballistic body armor - Gizmag.com, 1 December 2014
- ↑ Import and export controls on law enforcement and military goods – fact sheet
- ↑ S.15A Summary Offences Act 1953
- ↑ Control of Weapons Act 1990
- ↑ Weapons Control Act
- ↑ Prohibited Weapons Regulation 1997
- ↑ Body Armour and Martial Arts
- ↑ Schedule 1 Prohibited Weapons
- ↑ Police Miscellaneous Amendments (No. 2) Bill 59 of 2009
- ↑ https://www.solgps.alberta.ca/programs_and_services/public_security/BACAct/Pages/default.aspx
External links
![]() |
Wikimedia Commons has media related to Bulletproof vests. |
- Ankylosaurus- The bullet proof dinosaur
- NIJ Ballistic Resistance of Body Armor
- Body Armor News and Knowledge Website
- NIJ body armor standard overview