Leading-edge slats
Slats are aerodynamic surfaces on the leading edge of the wings of fixed-wing aircraft which, when deployed, allow the wing to operate at a higher angle of attack. A higher coefficient of lift is produced as a result of angle of attack and speed, so by deploying slats an aircraft can fly at slower speeds, or take off and land in shorter distances. They are usually used while landing or performing maneuvers which take the aircraft close to the stall, but are usually retracted in normal flight to minimize drag.
Slats are one of several high-lift devices used on airliners, such as flap systems running along the trailing edge of the wing.
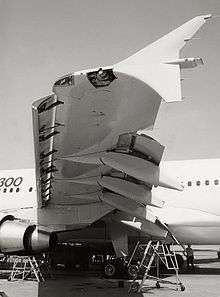

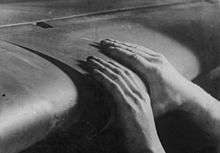
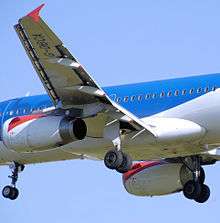
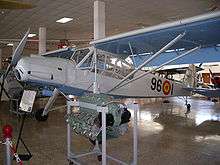
Types
Types include:
- Automatic
- The slat lies flush with the wing leading edge until reduced aerodynamic forces allow it to extend by way of aerodynamics when needed. Sometimes referred to as Handley-Page slats.
- Fixed
- The slat is permanently extended. This is sometimes used on specialist low-speed aircraft (these are referred to as slots) or when simplicity takes precedence over speed.
- Powered
- The slat extension can be controlled by the pilot. This is commonly used on airliners.
Operation
The chord of the slat is typically only a few percent of the wing chord. The slats may extend over the outer third of the wing, or they may cover the entire leading edge. Many early aerodynamicists, including Ludwig Prandtl believed that slats work by inducing a high energy stream to the flow of the main airfoil thus re-energizing its boundary layer and delaying stall.[1] In reality, the slat does not give the air in the slot high velocity (it actually reduces its velocity) and also it cannot be called high-energy air since all the air outside the actual boundary layers has the same total heat. The actual effects of the slat are:[2][3]
- The slat effect
- The velocities at the leading edge of the downstream element (main airfoil) are reduced due to the circulation of the upstream element (slat) thus reducing the pressure peaks of the downstream element.
- The circulation effect
- The circulation of the downstream element increases the circulation of the upstream element thus improving its aerodynamic performance.
- The dumping effect
- The discharge velocity at the trailing edge of the slat is increased due to the circulation of the main airfoil thus alleviating separation problems or increasing lift.
- Off the surface pressure recovery
- The deceleration of the slat wake occurs in an efficient manner, out of contact with a wall.
- Fresh boundary layer effect
- Each new element starts out with a fresh boundary layer at its leading edge. Thin boundary layers can withstand stronger adverse gradients than thick ones.[3]
The slat has a counterpart found in the wings of some birds, the alula, a feather or group of feathers which the bird can extend under control of its "thumb".
History

Slats were first developed by Gustav Lachmann in 1918. A crash in August 1917, with a Rumpler C aeroplane on account of stalling caused the idea to be put in a concrete form, and a small wooden model was built in 1917 in Cologne. In 1918, Lachmann presented a patent for leading-edge slats in Germany. However, the German patent office at first rejected it as the office did not believe in the possibility of increasing lift by dividing the wing.[4][5]
Independently of Lachmann, Handley Page Ltd in Great Britain also developed the slotted wing as a way to postpone stall by reducing the turbulence over the wing at high angles of attack, and applied for a patent in 1919; to avoid a patent challenge, they reached an ownership agreement with Lachmann. That year a De Havilland D.H.9 was fitted with slats and flown.[6] Later, a D.H.4 was modified as a monoplane with a large wing fitted with full span leading edge and back ailerons (i.e. what would later be called flaps) that could be deployed in conjunction with the leading-edge slats to test improved low speed performance.[7] Several years later, having subsequently taken employment at the Handley-Page aircraft company, Lachmann was responsible for a number of aircraft designs, including the Handley Page Hampden.
Licensing the design became one of the company's major sources of income in the 1920s. The original designs were in the form of a fixed slot in the front of the wing, a design that was found on a number of STOL aircraft.
During World War II, German aircraft commonly fitted a more advanced version that pushed back flush against the wing by air pressure to reduce drag, popping out when the angle of attack increased during slower flight. Notable slats of that time belonged to the German Fieseler Fi 156 Storch. These were similar in design to retractable slats, but were fixed non-retractable slots. The slotted wing allowed this aircraft to take off into a light wind in less than 45 m (150 ft), and land in 18 m (60 ft). Aircraft designed by the Messerschmitt company did NOT employ automatic with spring-loaded leading-edge slats as a general believed, except for the Alexander Lippisch-designed Messerschmitt Me 163B Komet rocket fighter, which used fixed slots built integrally with, and just behind the wing panel's outer leading edges instead.
Post World War II, slats have generally been operated by hydraulics or electricity on larger aircraft.
In 1993, China Eastern Airlines Flight 583 had to make an emergency landing after accidentally deploying the slats at cruise speed, which caused severe oscillations.
Research
Several technology research and development efforts exist to integrate the functions of flight control systems such as ailerons, elevators, elevons, flaps, and flaperons into wings to perform the aerodynamic purpose with the advantages of less: mass, cost, drag, inertia (for faster, stronger control response), complexity (mechanically simpler, fewer moving parts or surfaces, less maintenance), and radar cross section for stealth. These may be used in many unmanned aerial vehicles (UAVs) and 6th generation fighter aircraft. One promising approach that could rival slats are flexible wings.
In flexible wings, much or all of a wing surface can change shape in flight to deflect air flow. The X-53 Active Aeroelastic Wing is a NASA effort. The Adaptive Compliant Wing is a military and commercial effort.[8][9][10]
See also
References
- ↑ Theory of wing sections, Abbott and Doenhoff, Dover Publications
- ↑ High-Lift Aerodynamics, A.M.O. Smith, Journal of Aircraft, 1975
- 1 2 High-Lift Aerodynamics, by A. M. O. Smith, McDonnell Douglas Corporation, Long Beach, June 1975
- ↑ NACA Technical notes, No. 71. Experiments with slotted wings. 1921.
- ↑ http://naca.central.cranfield.ac.uk/reports/1921/naca-tn-71.pdf
- ↑ F. Handley Page "Developments In Aircraft Design By The Use Of Slotted Wings" Flight, December 22, 1921, photo page 844 of converted D.H.9 for testing of slotted wings
- ↑ F. Handley Page "Developments In Aircraft Design By The Use Of Slotted Wings" Flight, December 22nd 1921, photo page 845 of converted D.H.4 for testing of slotted wings
- ↑ Scott, William B. (27 November 2006), "Morphing Wings", Aviation Week & Space Technology
- ↑ "FlexSys Inc.: Aerospace". Retrieved 26 April 2011.
- ↑ Kota, Sridhar; Osborn, Russell; Ervin, Gregory; Maric, Dragan; Flick, Peter; Paul, Donald. "Mission Adaptive Compliant Wing – Design, Fabrication and Flight Test" (PDF). Ann Arbor, MI; Dayton, OH, U.S.A.: FlexSys Inc., Air Force Research Laboratory. Retrieved 26 April 2011.
External links
![]() |
Wikimedia Commons has media related to Leading-edge flaps. |