Staged combustion cycle
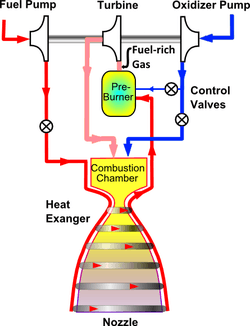
The staged combustion cycle, also called topping cycle or preburner cycle,[1] is a thermodynamic cycle used in some bipropellant rocket engines. In staged combustion, one propellant is sent through a preburner and partially burned using a small portion of the second propellant. The resulting hot gas is used to power the engine's turbines and pumps, then injected into the main combustion chamber along with the remainder of the second propellant to complete combustion. There are two main variants of the cycle depending on which propellant is sent through the preburner: oxidizer-rich staged combustion (ORSC) and fuel-rich staged combustion (FRSC).[2]
The advantage of staged, or "closed", combustion is that all of the cycle's gases and heat go through the combustion chamber. (An alternative design, called the gas-generator cycle, is an "open" cycle where the gas used to drive the turbopumps is exhausted overboard without passing through the main combustion chamber, reducing efficiency.) Since no propellant is dumped overboard, staged combustion allows for high power turbopumps which permit very high chamber pressures, allowing the use of high expansion ratio nozzles at low altitude for better performance. Disadvantages of staged combustion include harsh turbine conditions, exotic plumbing to carry the hot gases, and complicated feedback and control. In particular, ORSC requires advanced metallurgy due to extremely corrosive oxidizer-rich gas, while FRSC requires use of a fuel that will not coke, such as liquid hydrogen.
History
Staged combustion (Замкнутая схема) was first proposed by Alexey Isaev in 1949. The first staged combustion engine was the S1.5400 (11D33) used in the Soviet planetary rocket, designed by Melnikov, a former assistant to Isaev.[3] About the same time (1959), Nikolai Kuznetsov began work on the closed cycle engine NK-9 for Korolev's orbital ICBM, GR-1. Kuznetsov later evolved that design into the NK-15 and NK-33 engines for the unsuccessful Lunar N1 rocket. The non-cryogenic N2O4/UDMH engine RD-253 using staged combustion was developed by Valentin Glushko around 1963 for the Proton rocket.
After the failure of the N-1, Kuznetsov had been ordered to destroy the NK-33 technology, but instead he warehoused dozens of the engines. In the 1990s, Aerojet was contacted and eventually visited Kuznetsov's plant. Upon meeting initial skepticism about the high specific impulse and other specifications, Kuznetsov shipped an engine to the US for testing. Oxidizer-rich staged combustion had been considered by American engineers, but deemed impossible.[4] The Russian RD-180 engine, purchased by Lockheed Martin (subsequently by United Launch Alliance) for the Atlas III and V rockets, also employs this technique.
The first laboratory staged-combustion test engine in the West was built in Germany in 1963, by Ludwig Boelkow.
Hydrogen peroxide/kerosene fueled engines such as the British Gamma of the 1950s may use a closed-cycle process by catalytically decomposing the peroxide to drive turbines before combustion with the kerosene in the combustion chamber proper. This gives the efficiency advantages of staged combustion, while avoiding major engineering problems.
The Space Shuttle Main Engine is another example of a staged combustion engine, and the first to use liquid oxygen and liquid hydrogen. Its counterpart in the Soviet shuttle was the RD-0120, similar in specific impulse, thrust, and chamber pressure specification to the SSME, but with some differences that reduced complexity and cost at the expense of increased engine weight.
Full-flow staged combustion cycle

Full-flow staged combustion (FFSC) is a variation on the staged combustion cycle which uses both an oxidizer-rich and fuel-rich preburner, allowing use of the full flow of both propellants to power the turbines.[5] The fuel turbopump is driven by the fuel-rich preburner, while the oxidizer-rich preburner drives the oxidizer turbopump.[2][5] This eliminates the need for an interpropellant turbine seal normally required to separate oxidizer-rich gas from the fuel turbopump or fuel-rich gas from the oxidizer turbopump.[6] The increased mass flow from FFSC allows both turbines to run cooler and at lower pressure, leading to a longer engine life and higher reliability. Up to 25 flights were anticipated for one particular engine design studied by the DLR (German Aerospoace Center) in the frame of the SpaceLiner project.[5]
Since the use of both fuel and oxidizer preburners results in full gasification of each propellant before entering the combustion chamber, FFSC engines are sometimes called gas-gas engines.[6] Full gasification of components leads to faster chemical reactions in the combustion chamber.
Early demonstration tests
Only three full-flow staged combustion rocket engines have ever progressed sufficiently to be tested on test stands: the Soviet Energomash RD-270 project in the 1960s, the US government-funded Aerojet Rocketdyne Integrated powerhead demonstration project in the mid-2000s,[6] and SpaceX's Raptor engine on 26 September 2016.[7]
Applications
Oxidizer-rich staged combustion engines include the following:
- S1.5400 - First staged combustion rocket engine.[3]
- NK-33 —Soviet engine developed for the never-flown upgraded version of the N-1 launch vehicle. Later sold to Aerojet Rocketdyne and refurbished/remarketed as the AJ-26 (used on Antares block 1 launch vehicles in 2013–2014). In use on the Soyuz 2.1v.
- RD-170
- RD-180 —1990s Russian engine currently used on the Atlas V and previously on the Atlas III. Derivative of RD-170.
- YF-100 — Chinese engine developed in the 2000s; used on the Long March 7 and planned for use on the Long March 5 and Long March 6.[8]
- AR-1 An Aerojet Rocketdyne project partially funded by the United States Air Force as a potential replacement for the RD-180 Russian engine.[9]
- BE-4 — Blue Origin LCH4/LOX engine planned to be used on the ULA Vulcan launch vehicle, which will replace the Atlas V and Delta IV, first flight test in 2019[10][11] and also on the Blue Origin orbital launch vehicle, with first flight test no earlier than 2020.[12]
- RD-253 —Soviet engine developed in the 1960s and used on the Proton launch vehicle's first stage. Later variants include the RD-275 and RD-275M.
- SCE-200 - Indian RP-1/LOX main stage engine in development.
Fuel-rich staged combustion engines include the following:
- RS-25 (SSME) - US developed 1970–1980s, flown on the Space Shuttle through 2011, and planned for further use on the Space Launch System after 2018.
- RD-0120 - LH2/LOX engine used in the Energia rocket.
- LE-7/7A
- KVD-1 - LH2/LOX upper stage engine.
- CE-7.5 - Indian LH2/LOX upper stage engine, used on the GSLV Mk2[13]
Full-flow staged combustion engines include the following:
- RD-270 [6] - Soviet engine under development 1962–1970; never flown.
- Integrated powerhead demonstrator - Demonstration project for the front part of a full flow engine, with no combustion chamber or other backend subsystems.[6] US project to develop a part of a new rocket engine technology in the early 2000s; no full engine ever built; never flown.
- Raptor - SpaceX LCH4/LOX engine in development since the 2010s.[6][14]
Staged combustion engines have been used in:
- Space Shuttle
- Atlas III
- Atlas V
- Antares (rocket)
- N1 (rocket)
- H-II
- H-IIA
- H-IIB
- GSLV
- Proton (rocket family)
- Zenit (rocket family)
- Energia
- Long March 6
Staged combustion engines are planned for:
See also
References
- ↑ United States General Accounting Office (1994). Aerospace Plane Technologies: R&D in Japan & Australia. DIANE Publishing. p. 145. ISBN 1-56806-059-9.
- 1 2 Emdee, Jeff (2004). "Launch Vehicle Propulsion" (PDF). Crosslink. Vol. 5 no. 1 (2004 Winter ed.). Aerospace Corp. pp. 12–19. Archived from the original on 2016-03-08. Retrieved 2016-09-30.
- 1 2 George Sutton, "History of Liquid Propellant Rocket Engines", 2006
- ↑ Cosmodrome History Channel, interviews with Aerojet and Kuznetsov engineers about the history of staged combustion
- 1 2 3 Sippel, Martin; Yamashiro, Ryoma; Cremaschi, Francesco (2012-05-10). "Staged Combustion Cycle Rocket Engine Design Trade-offs for Future Advanced Passenger Transport" (PDF). Space Propulsion 2012. ST28-5. DLR-SART. Retrieved 2014-03-19.
- 1 2 3 4 5 6 7 Belluscio, Alejandro G. (2014-03-07). "SpaceX advances drive for Mars rocket via Raptor power". NASAspaceflight.com. Retrieved 2014-03-09.
- ↑ "Elon Musk on Twitter: "SpaceX propulsion just achieved first firing of the Raptor interplanetary transport engine "". Twitter. 2009-06-02. Retrieved 2016-09-28.
- ↑ Rui C. Barbosa (2016-06-25). "China successfully debuts Long March 7 – Recovers capsule". NASASpaceFlight.com. Retrieved 2016-09-28.
- ↑ "AR1 Booster Engine | Aerojet Rocketdyne". Rocket.com. Retrieved 2016-09-28.
- ↑ Clark, Stephen (2014-09-17). "ULA taps Blue Origin for powerful new rocket engine". Spaceflight Now. Retrieved 2015-04-13.
Blue Origin's BE-4 engine uses an oxygen-rich staged combustion cycle, employs a single nozzle, and burns liquid oxygen and liquefied natural gas, a fuel that makes the engine cheaper, less complex, and easier to reuse, according to a fact sheet released by Blue Origin.
- ↑ Blue Origin. "BE-4 Rocket Engine" (PDF). ULA website 2014. Retrieved 2014-03-19.
- ↑ Berger, Eric (2016-03-09). "Behind the curtain: Ars goes inside Blue Origin's secretive rocket factory". Ars Technica. Retrieved 2016-03-12.
- ↑ "GSLV MkIII, the next milestone". Frontline. 2014-02-07.
- ↑ Todd, David (2012-11-22). "SpaceX's Mars rocket to be methane-fuelled". Flightglobal. Retrieved 2012-12-05.
Musk said Lox and methane would be SpaceX’s propellants of choice on a mission to Mars, which has long been his stated goal. SpaceX’s initial work will be to build a Lox/methane rocket for a future upper stage, codenamed Raptor. The design of this engine would be a departure from the “open cycle” gas generator system that the current Merlin 1 engine series uses. Instead, the new rocket engine would use a much more efficient “staged combustion” cycle that many Russian rocket engines use.
- ↑ "United Launch Alliance Unveils America's New Rocket – Vulcan". Ulalaunch.com. Retrieved 2015-04-13.
External links
- Rocket power cycles
- Nasa's full flow stages combustion cycle demonstrator
- Design Tool for Liquid Rocket Engine Thermodynamic Analysis